SBH Drum Blender
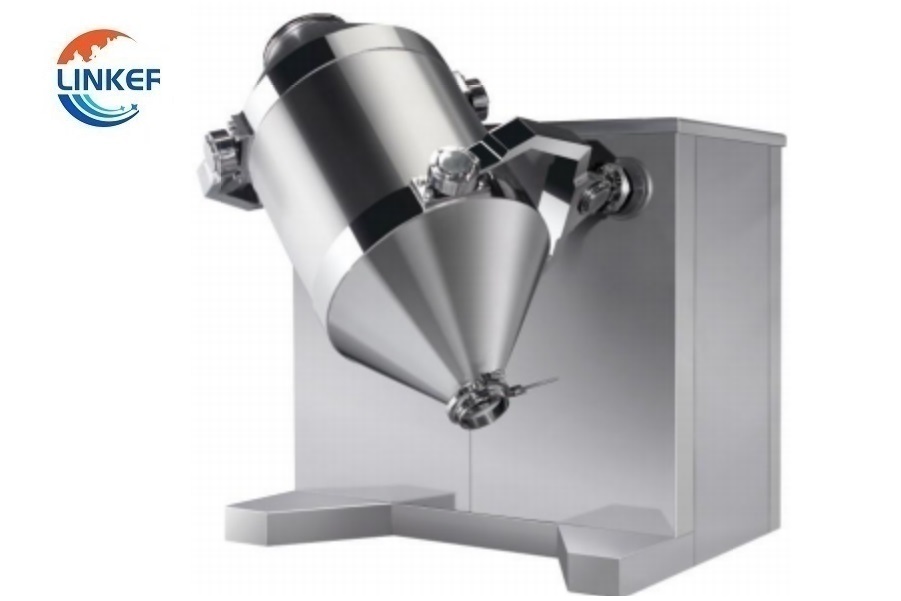
Pharmaceutical Drum Blender Machine
- Also called: Drum Mixer, Barrel Blender, Barrel Mixer, Rotary Drum Blender;
- Material: Dry powder; Dry Granule;
- Maximum mixing volume: 4~1270(kg/time);
- Volumn: 5~1500L;
- Rotating Speed: 3~20r/min;
- Machine Weight:11~37(kw);
- Total Power: 1.5~18.5kg
- Application: pharmaceutcal chemical, meallugy. tood light indusry. agriculture and other industries.
- Price: 125USD~11,000USD(Depend on models).
Parameters of Drum Blender:
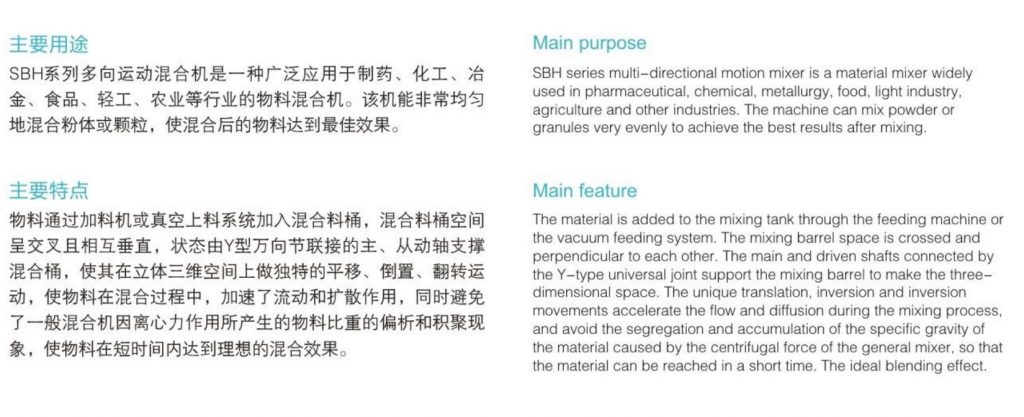
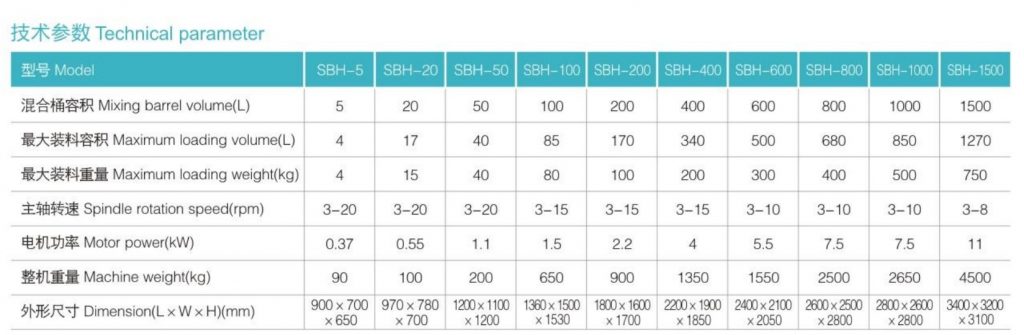
Model | Mixing Barrel Volume(L) | Max Loading Volume(L) | Max Loading Weight(KG) | Rotating Speed(rpm) | Motor Power(KW) | Dimension(mm) |
SBH-5 | 5 | 4 | 4 | 3-20 | 0.37 | 900×700 X650 |
SBH-20 | 20 | 17 | 15 | 3-20 | 0.55 | 970×780 × 700 |
SBH-50 | 50 | 40 | 40 | 3-20 | 1.1 | 1200×110 x1200 |
SBH-100 | 100 | 85 | 80 | 3-15 | 1.5 | 1360×150 X1530 |
SBH-200 | 200 | 170 | 100 | 3-15 | 2.2 | 1800×160 1700 |
SBH-400 | 400 | 340 | 200 | 3-15 | 4 | 220×190 x1850 |
SBH-600 | 600 | 500 | 300 | 3-10 | 5.5 | 240×2100 X2050 |
SBH-800 | 800 | 680 | 400 | 3-10 | 7.5 | 2600×.200 x2800 |
SBH-1000 | 1000 | 850 | 500 | 3-10 | 7.5 | 2800×2600 X2800 |
SBH-1500 | 1500 | 1270 | 750 | 3-8 | 11 | 340×3200 X3100 |
I. What is Drum Blender?
A drum blender, also known as a drum mixer or rotary drum blender, is a type of industrial mixing equipment used to blend and homogenize materials in a rotating drum or cylinder-shaped container. These blenders are commonly used in various industries, including food processing, pharmaceuticals, chemicals, and agriculture.
Here’s how a drum blender typically works:
Loading: Materials to be mixed, such as powders, granules, or solids, are loaded into the drum.
Rotation: The drum is set into motion, usually by a motor or other mechanical means, causing it to rotate horizontally or at an inclined angle.
Mixing: As the drum rotates, the materials inside are lifted and then allowed to cascade or tumble back down. This tumbling action facilitates mixing and blending as the materials interact with each other.
Homogenization: The continuous rotation of the drum ensures that the materials are thoroughly mixed, resulting in a uniform blend.
Unloading: After the mixing process is complete, the drum is stopped, and the blended materials are discharged from the drum, typically through a discharge chute or opening.
Drum blenders are available in various sizes and configurations to accommodate different production needs. They are valued for their simplicity, reliability, and ability to effectively mix a wide range of dry or solid materials. Drum blenders find applications in mixing food ingredients, fertilizers, pharmaceutical powders, chemicals, and more, making them a versatile tool in industrial processing.
Business Type: | Manufacturer/Factory | Main Products: | Mill, grinder, granulator, mixer, Crushing Equipment |
Number of Employees: | 100 | Year of Establishment: | 2014.05 |
Production Capacity | 5000Set/Year | After-sales Service: | Technical Support; on-line teach lessons |
R&D Capacity: | ODM, OEM | Annual Output Value: | US$5 Million – US$10 Million |
No. of R&D Staff: | 5 | No. of Production Lines: | 6 |
LK Mixer is a professional manufacturer for grinder, mixer and pulverizer. These machines are widely used in pharmaceutical, cosmetic, health care products and chemical industries. Our main product including granulating machine, grinder, mixer, dryer, etc. All mechanical products in accordance with the China GMP design requirements. And also we have other certifications such as CE, UL for motors.
Business Philosophy
“Quality is the main policy of sales” and “integrity is the principle of success” are the business philosophy of our people. We carry out one-year warranty, lifelong maintenance service, with technical consultation, with material test machine and other services, and long-term supply of equipment. Welcome new and old customers to negotiate cooperation!
Certifications:
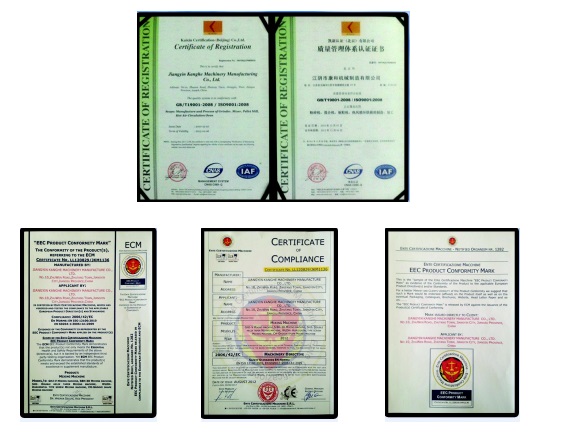
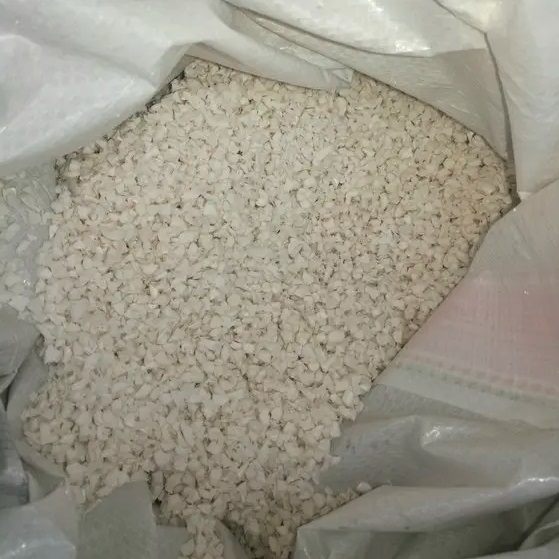
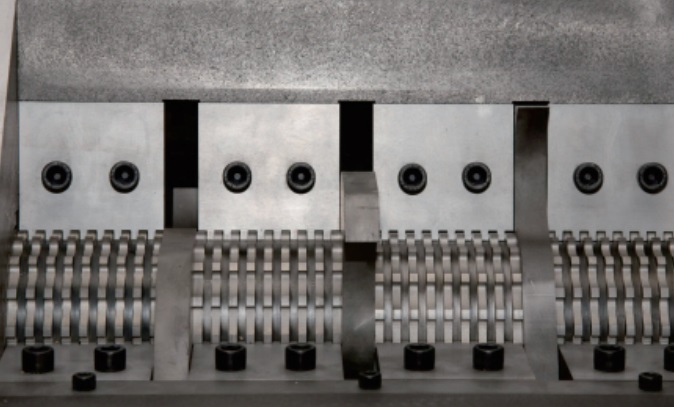
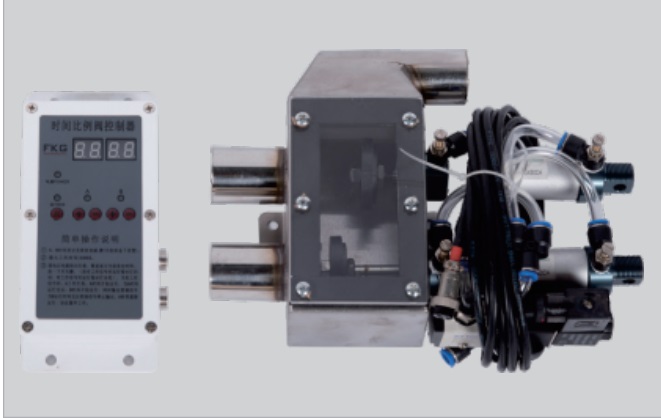
Electric Cabinet with UL Certification
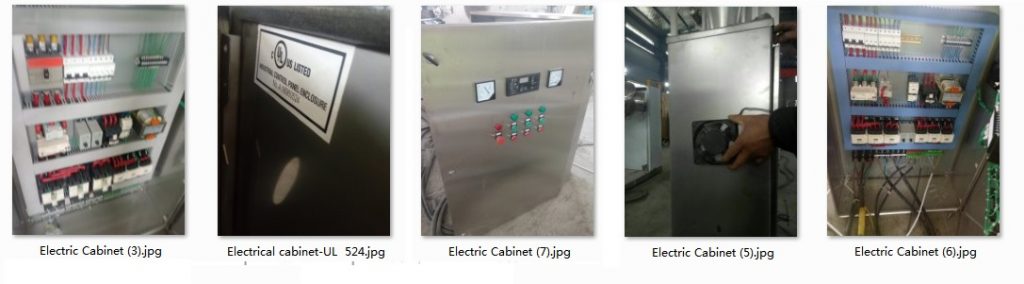
Cyclone Processor and Motors:
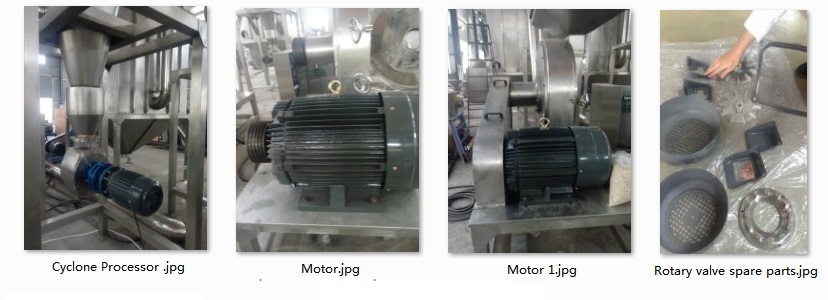
Spare Parts:
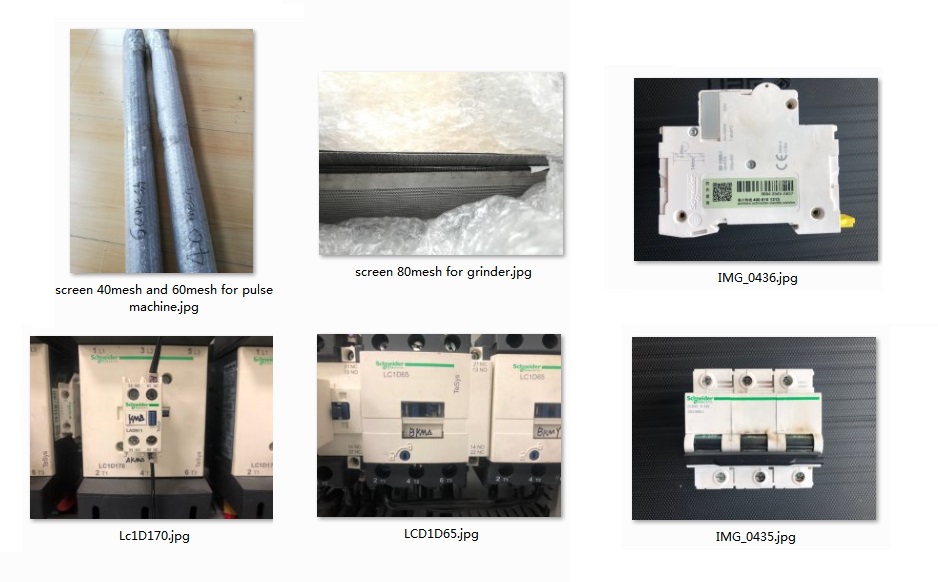
Small Machine Packing:
Small machine packed with export fumigation-free wooden cases, goes with bulk shipment or in container.
When packing small machines for sea shipment, it is important to take measures to ensure that the machines are protected from damage during transit. Here are some general steps that a manufacturer may follow when packing small machines for sea shipment:
- Clean and dry the machine: Before packing, the machine should be thoroughly cleaned and dried to prevent any moisture or debris from causing damage during transit.
- Disassemble the machine: If possible, the machine should be disassembled into its component parts to reduce its overall size and make it easier to pack.
- Wrap the machine in protective material: The machine should be wrapped in a layer of protective material, such as bubble wrap or foam, to protect it from scratches and impact during transit.
- Place the machine in a sturdy box: The wrapped machine should then be placed in a sturdy box that is appropriate for the size and weight of the machine. The box should be made of durable material, such as corrugated cardboard or plywood, and should be able to withstand the rigors of sea transit.
- Add packing material: The box should be filled with packing material, such as packing peanuts or air pillows, to provide cushioning and prevent the machine from shifting during transit.
- Seal the box: The box should be securely sealed with high-quality packing tape to prevent it from opening during transit.
- Label the box: The box should be clearly labeled with the machine’s name, weight, and any other relevant information, as well as the destination address and contact information.
Overall, the goal is to pack the small machine in a way that will protect it from damage during transit and ensure that it arrives at its destination in good condition. It is important to follow proper packing procedures and use high-quality packing materials to minimize the risk of damage during sea shipment.
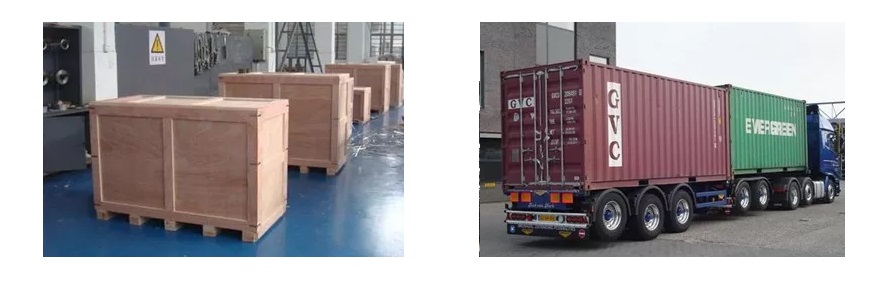
Large Machine Packing:
Packing a large machine for sea shipment can be a complex and challenging task. However, with careful planning and attention to detail, it is possible to pack a large machine for sea shipment in a way that will ensure that it arrives at its destination in good condition. Here are some general steps that a manufacturer may follow when packing up a large machine for sea shipment:
- Clean and prepare the machine: Before packing, the machine should be thoroughly cleaned and prepared. All fluids, such as oil or coolant, should be drained, and any loose or detachable parts should be removed.
- Disassemble the machine: If possible, the machine should be disassembled into its component parts to reduce its overall size and make it easier to pack. Each part should be carefully labeled and numbered to ensure that it can be easily reassembled at the destination.
- Protect delicate parts: Delicate or fragile parts should be wrapped in protective material, such as bubble wrap or foam, to protect them from damage during transit.
- Build a custom crate: A custom crate should be built around the machine to provide a secure and sturdy enclosure. The crate should be made of durable material, such as plywood, and should be designed to fit the machine snugly. The crate should also include braces or supports to prevent the machine from shifting during transit.
- Add cushioning material: The crate should be filled with cushioning material, such as packing peanuts or air pillows, to provide extra protection and prevent the machine from moving or shifting during transit.
- Securely fasten the machine: The machine should be securely fastened to the crate to prevent it from moving or shifting during transit. This may involve using straps, bolts, or other fasteners to hold the machine in place.
- Seal and label the crate: The crate should be securely sealed with high-quality packing tape, and should be clearly labeled with the machine’s name, weight, and any other relevant information. The destination address and contact information should also be clearly marked on the crate.
Overall, packing a large machine for sea shipment requires careful planning and attention to detail. It is important to use high-quality materials and follow proper packing procedures to ensure that the machine arrives at its destination in good condition. A professional packing and shipping company may be consulted to ensure that the machine is properly packed and prepared for sea shipment.
Customer Side Machine Groups Showcase Videos:
Dust Collector Shipment
Shipment – Packing Method
Two Large Industrial Grinder Ready to Ship
Domestic Shipment Show Case:
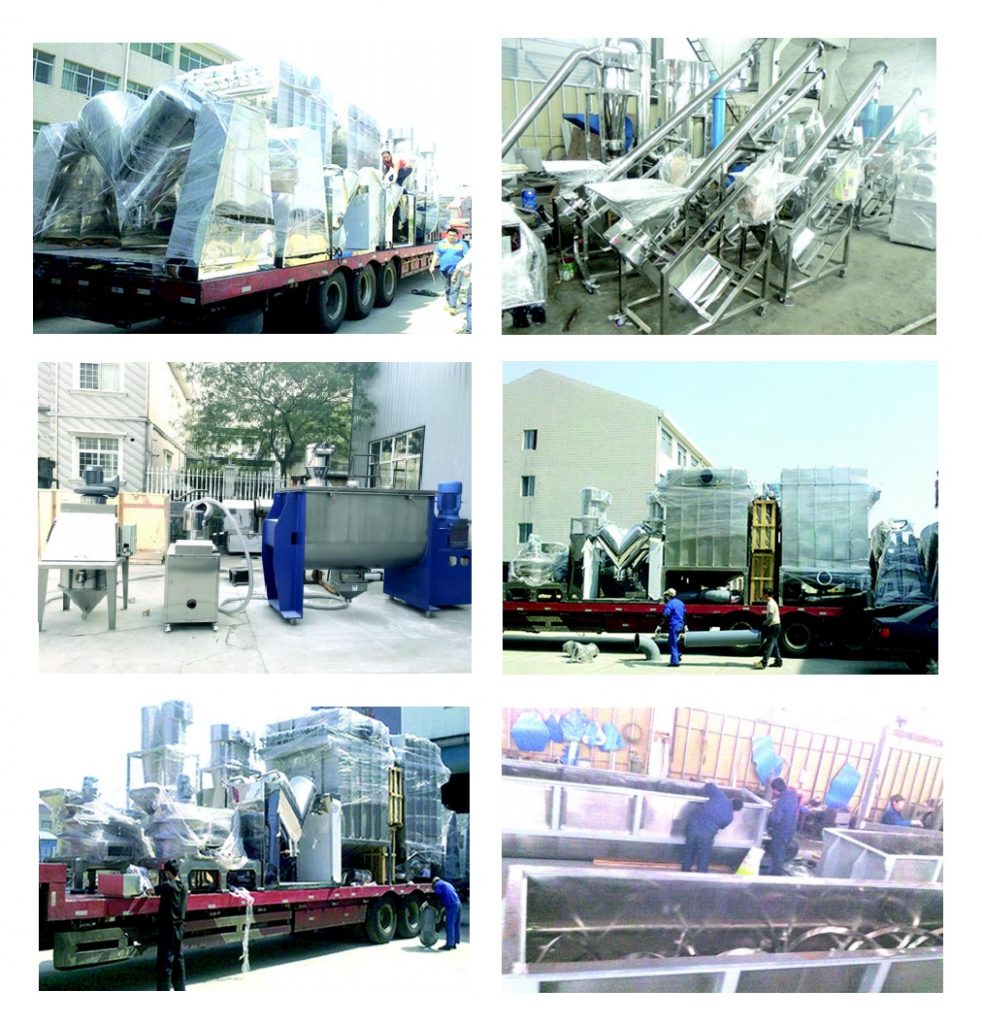
Installation Layout:
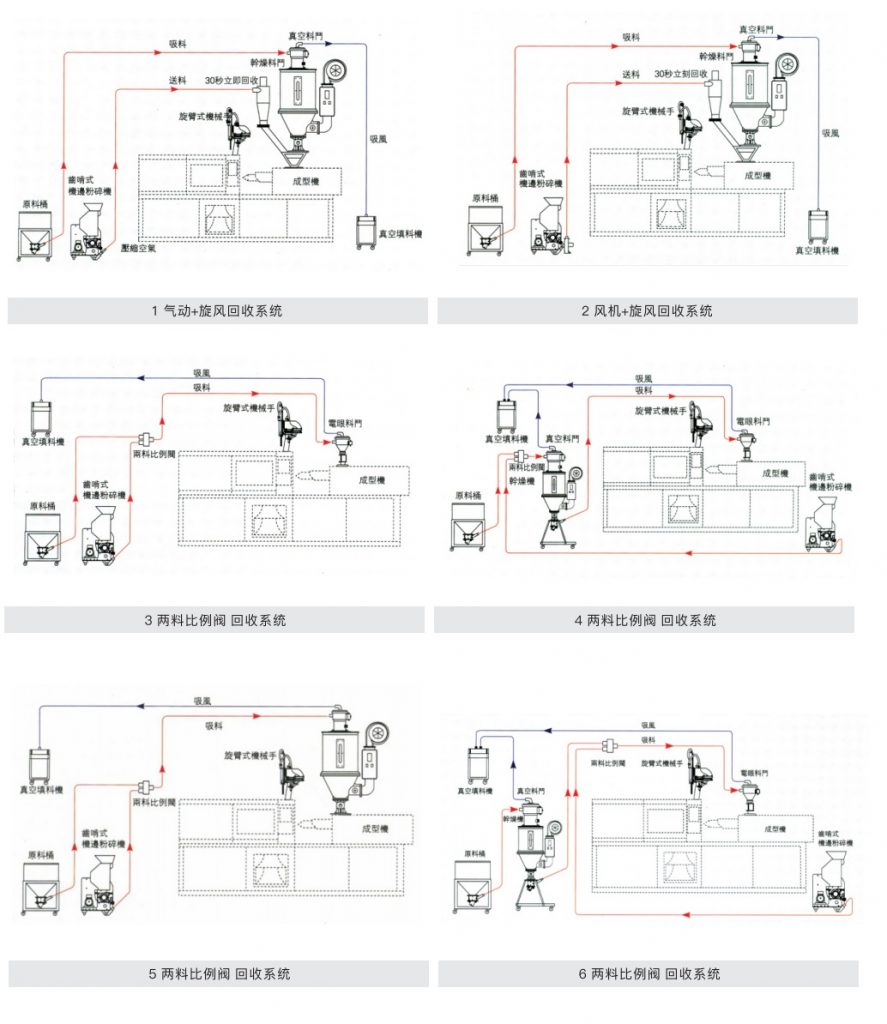
Maintenance and Safety Measures
Proper maintenance practices for the machine
Proper maintenance practices are essential for ensuring the efficient and safe operation of a universal grinder. Here are some maintenance practices that should be followed:
- Regular cleaning – The machine should be cleaned regularly to remove any debris, dust, or coolant that may accumulate on the machine’s surfaces. This can be done using a soft brush, air hose, or a cleaning solution.
- Lubrication – The machine’s moving parts should be lubricated regularly to reduce friction and wear. The manufacturer’s recommendations for lubrication intervals and types should be followed.
- Inspection – The machine should be inspected regularly for any signs of wear, damage, or misalignment. Any issues should be addressed immediately to prevent further damage or safety hazards.
- Replacement of worn or damaged parts – Worn or damaged parts should be replaced immediately with genuine parts from the manufacturer.
- Calibration – The machine should be calibrated regularly to ensure that it is operating within the specified tolerances and accuracy.
- Operator training – Proper operator training is essential for ensuring the safe and efficient operation of the machine. Operators should be trained on the proper operation, maintenance, and safety procedures for the machine.
- Record keeping – A maintenance log should be kept to track the machine’s maintenance history, including cleaning, lubrication, inspection, and repairs. This can help identify any trends or issues that need to be addressed.
Following these maintenance practices can help ensure the safe and efficient operation of a universal grinder, prolong its lifespan, and reduce the risk of downtime and costly repairs.
Safety measures for operators and workers
Safety measures for operators and workers are crucial when using a universal grinder. Here are some safety measures that should be followed:
- Personal protective equipment (PPE) – Operators and workers should wear appropriate PPE, including safety glasses, hearing protection, gloves, and safety shoes.
- Machine guards – The machine should be equipped with proper machine guards to prevent access to the grinding wheel during operation. The guards should be in good condition and properly installed.
- Lockout/tagout procedures – Lockout/tagout procedures should be followed to ensure that the machine is not accidentally started or energized during maintenance or repair.
- Training – Operators and workers should receive proper training on the safe operation of the machine, including the use of PPE, machine guards, and lockout/tagout procedures.
- Inspection – The machine should be inspected regularly for any signs of wear, damage, or misalignment that may pose a safety hazard.
- Proper use of grinding wheels – Operators should ensure that the grinding wheel is properly installed, dressed, and aligned. The grinding wheel should not be overloaded or forced into the material being ground.
- Proper handling of coolant – If coolant is used, operators should ensure that it is properly mixed, applied, and contained. Coolant should not be allowed to accumulate on the floor, as it can create a slipping hazard.
- Emergency procedures – Emergency procedures should be established and communicated to all operators and workers in case of an accident or injury.
Following these safety measures can help prevent accidents and injuries when using a universal grinder. It is important to prioritize safety and ensure that all operators and workers are trained and informed about the potential hazards of the machine.
Universal Grinder Youtube Video (See More)
About LKMixer
LKMixer is a professional manufacturer for fertilizer production line, grinder, mixer and granulator, shredder. These machines are widely used in food, pharmaceutical, cosmetic, health care products and chemical industries. The Food materials like Peanut, mushroom, seeds, potato, bean, tobacco, salt, cannabis, tea, Sugar, corn, Coffee, rice, pepper, grain as so on. Grinders have many types such as Pulse Dust Grinder which suitable for zero pollution environment, Turbine Mill which is suitable for coffee bean, 12-120mesh all can meet, Ultrafine Grinding Mill covers 80-200mesh, and also Winnowing Dust Grinder or other grinding machines like SF Hammer. Welcome to contact us for details. Contact us for more information. Proposal, catalog, quotation. Mobile/WhatsApp: +86 18019763531 Tel: +86 21 66037855 Email: sales@lkmixer.com