CH Horizontal Mixer
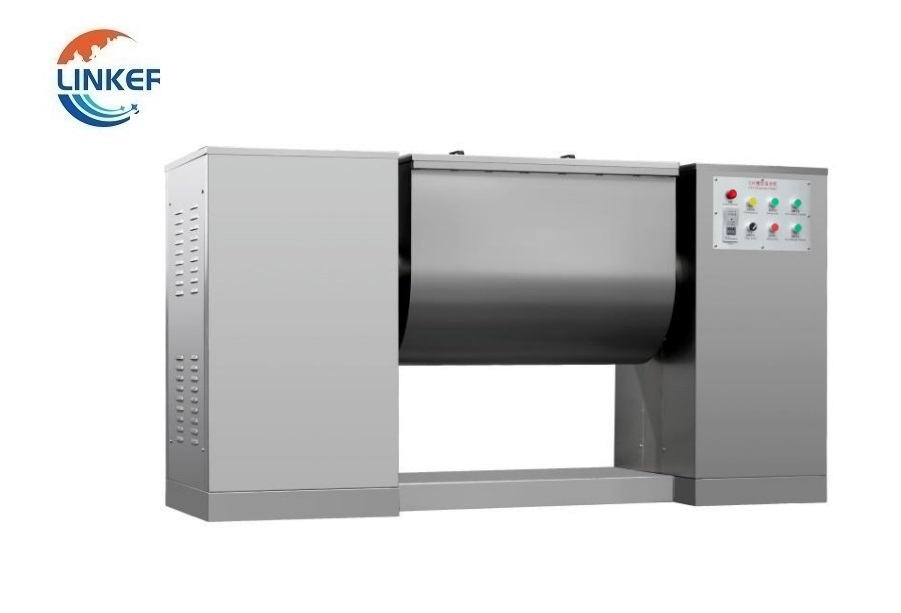
CH Tank Type Horizontal Mixer
- This series machine takes a strong and high effective mixing as its features The two mixing axles fotate reversely at an identical revolution in the horizonta drum body. The paddles specially distyibuted on the axle ensure that the matera move radcally.circulatingly,and axially,so as to form a compound motion,and in an extremely short time the materia is mxed eveny mixed results (ie addition of a few ingredients mixed).
- Mixed amount/bach KG : 40-3600L;
- Machine Weight: 150-3800(kg);
- Total Power: 3-37 KW
- Weight: 440-660KG;
- Application: Chemicals,detergent,fertilizer,feedstuff,additive whcat fiout, milk powder, perfume micro ingredient,coffee gourmet power sall plastic and allkinds ol pulp,powder material.
What is Horizontal Mixer?
A horizontal mixer is a specialized machine used in various industries, especially in baking and food production. Its standout feature is its remarkable capability to handle large volumes of dough in a very short time.
Here’s how it works: As the dough is mixed, a continuous feeding mechanism ensures that the next batch of dough is continually introduced into the machine. This means that as one batch gets mixed, another is already on its way, making the process highly efficient.
Once the mixing is complete, the dough conveniently exits the machine and flows into a trough, ready for transport or further processing. This seamless workflow is a major advantage of horizontal mixers, particularly in commercial settings where large quantities of dough need to be produced swiftly.
However, there is one aspect to be cautious about when using a horizontal mixer. The friction generated as the dough rubs against the walls of the mixing chamber can cause the temperature of the dough to rise. While this may not be an issue for many types of dough, it can be a concern for certain yeast doughs that require precise temperature control.
In summary, a horizontal mixer is a workhorse in the world of dough preparation, known for its exceptional capacity and efficiency in handling sizable batches. It plays a vital role in bakeries and food production facilities, ensuring a smooth and speedy mixing process for a wide range of culinary creations.
Understanding the Working Principle and Applications of Horizontal Mixers:
A horizontal spiral belt mixer operates on a gravity-free working principle. This type of mixer features a horizontal cylinder equipped with double-axis rotating blades that turn in opposite directions. These blades are strategically angled to create circulation and stirring movements along both the axial and radial directions, ensuring a quick and uniform mixture of materials.
The key characteristics of a horizontal mixer lie in the rotation speed of the shaft, driven by a reducer, and the unique blade structure. These elements effectively counteract the force of gravity on the materials being mixed. As a result, even when dealing with materials of varying particle sizes and specific gravities, these differences become negligible during the mixing process.
The vigorous stirring action significantly reduces mixing time, making it both faster and more efficient. Even materials with distinct variations in specific gravity and particle size can achieve excellent mixing results thanks to the rapid and forceful flipping and scattering actions of the staggered mixing blades.
Applications of Horizontal Mixers:
Horizontal mixers find wide-ranging applications in various industries due to their efficient and thorough mixing capabilities. Some common uses include:
In summary, horizontal mixers are versatile machines with a gravity-free working principle, making them highly efficient at achieving uniform mixing across a wide range of materials. Their applications span multiple industries, ensuring consistent and quality results in various manufacturing processes.
Horizontal mixers offer several advantages that can make them the preferred choice in specific situations:
- Uniform Mixing: Horizontal mixers excel at achieving a more uniform mix of feed. This is crucial for certain animals that receive smaller, carefully measured meals, ensuring consistent nutrition.
- Lower Inclusion Rates: They can incorporate premixes at lower inclusion rates, often as low as 1 kg per metric ton of feed. In contrast, most vertical mixers require a minimum inclusion rate of 3 kg per metric ton, providing greater flexibility.
- Minimal Feed Residue: Horizontal mixers operate at an angle or feature bottom trap doors, facilitating complete discharge of the mixed feed. In contrast, vertical mixers tend to leave a small but unavoidable residue.
However, the choice between horizontal and vertical mixers depends on the specific needs and circumstances:
For Small to Medium Farm Mixers: These farms, typically focusing on one animal species, often choose vertical mixers due to cost considerations. They aim to minimize expenses as they may not be expanding production. Additionally, they often buy low-inclusion products locally, which are usually up-mixed, eliminating the need for horizontal mixers.
For Large Farm Mixers: Larger farms with substantial purchasing power can secure micro-ingredients at lower prices, such as tightly packed vitamin premixes at 1 kilogram per metric ton. In such cases, precision in mixing becomes essential, and the extra cost of a vertical mixer can be offset by reduced raw material expenses.
For Local Feed Plants: Local feed plants usually focus on producing complete feeds for end-users. They tend to avoid very low-inclusion micro-ingredients and concentrate on one or two animal species. The exception is when handling feeds for animals with specific copper tolerance requirements, where the absence of feed residue becomes crucial.
For Local Premix Plants: In markets where home mixing is common, local premix suppliers often provide premix packages for various species. Investing in a horizontal mixer can be advantageous for achieving uniformity and reducing feed residue, potentially serving as a marketing differentiator.
In summary, the choice between horizontal and vertical mixers depends on factors such as farm size, purchasing power, specific ingredient needs, and mixing precision requirements. Smaller farms often opt for vertical mixers for cost reduction, while larger farms and facilities prioritize horizontal mixers for various reasons, including uniform mixing and reduced feed residue. Ultimately, the selection should align with the specific goals and circumstances of the operation.
Universal Grinder Youtube Video (See More)
About LKMixer
LKMixer is a professional manufacturer for fertilizer production line, grinder, mixer and granulator, shredder. These machines are widely used in food, pharmaceutical, cosmetic, health care products and chemical industries. The Food materials like Peanut, mushroom, seeds, potato, bean, tobacco, salt, cannabis, tea, Sugar, corn, Coffee, rice, pepper, grain as so on. Grinders have many types such as Pulse Dust Grinder which suitable for zero pollution environment, Turbine Mill which is suitable for coffee bean, 12-120mesh all can meet, Ultrafine Grinding Mill covers 80-200mesh, and also Winnowing Dust Grinder or other grinding machines like SF Hammer. Welcome to contact us for details. Contact us for more information. Proposal, catalog, quotation. Mobile/WhatsApp: +86 18019763531 Tel: +86 21 66037855 Email: sales@lkmixer.com