WLD Ribbon Blender
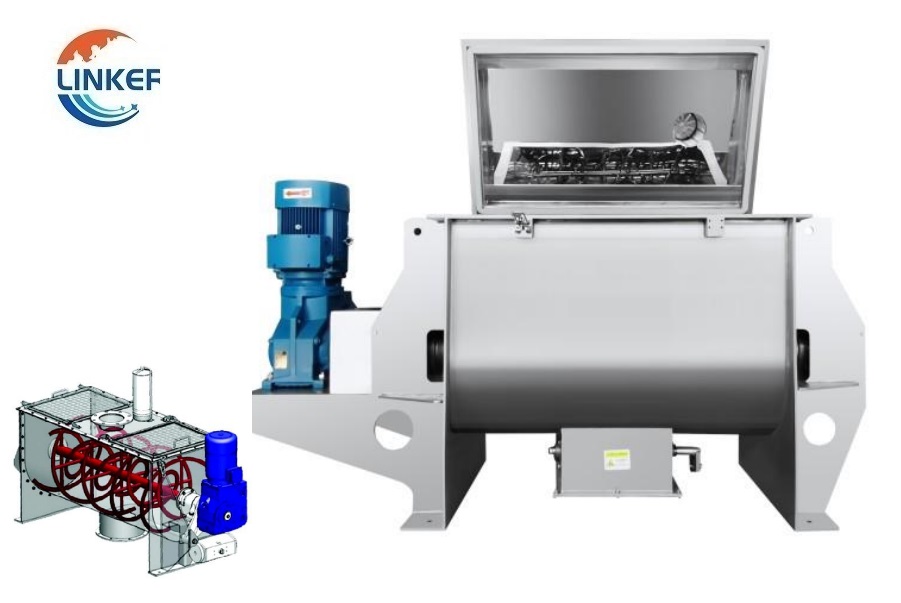
WLD Horizontal Spiral Ribbon Mixer
- Suitable Blending Material: Dry Powder , Liquid glue type
- Maximum mixing volume: 50-10000(kg);
- Volumn: 25-5000L;
- Rotating Speed: 0-18;
- Machine Weight: 250-3800(kg);
- Total Power: 0.55-11kg
- Application: Pharmaceuticals, Nutraceuticals, Food Products, Chemicals, Fertilizer, Stucco, Clay, Potting Soils, Paint, Plastics.
Parameters of Ribbon Blender:
Model | L*W*H(mm) | Max Mixing Volume(L) | Spindle Speed(rpm/min) | Machine Weight(KG) | Total Power(KG) |
WLD-100 | 1190×740× 770 | 50 | 58 | 380 | 2.2 |
WLD-150 | 2030× 630 x 980 | 80 | 53 | 450 | 3 |
WLD-300 | 2320 × 730 × 1130 | 150 | 53 | 560 | 4 |
WLD-500 | 2800 ×920 × 1320 | 300 | 49 | 680 | 7.5 |
WLD-1000 | 3180 × 1020x 1550 | 600 | 42 | 1200 | 11 |
WLD-1500 | 3310× 1120× 1640 | 880 | 42 | 1600 | 15 |
WLD-2000 | 3750× 1290 × 1820 | 1000 | 42 | 2200 | 18.5 |
WLD-3000 | 4220×1400× 1980 | 1500 | 37 | 3300 | 18.5 |
WLD-4000 | 4220× 1500× 2100 | 2000 | 37 | 3800 | 22 |
WLD-5000 | 4700× 1610× 2260 | 3000 | 31 | 4300 | 30 |
WLD-6000 | 4420 x 2150 x2470 | 3500 | 31 | 5500 | 37 |
WLD-8000 | 5520×2360 ×2720 | 4200 | 27 | 6800 | 45 |
WLD-10000 | 5720× 2520×2840 | 5000 | 27 | 7900 | 55 |
WLD-12000 | 5840×2850 ×2940 | 6000 | 23 | 8800 | 55 |
WLD-15000 | 6000× 3040× 3050 | 8000 | 23 | 9600 | 75 |
WLD-20000 | 6100× 3300× 3150 | 10000 | 19 | 13500 | 90 |
WLD-30000 | 6500×3500×3500 | 15000 | 17 | 15000 | 110 |
The Design of Ribbon Blender:
The horizontal ribbon mixer is made up of three main components: a transmission unit, a U-shaped barrel, and a double-layer ribbon mixer. The blender’s shell has a U-shaped design, and at its center, there’s a rotating agitator. This agitator features a double helix design, which enables it to efficiently mix bulk materials in two directions through a convective motion.
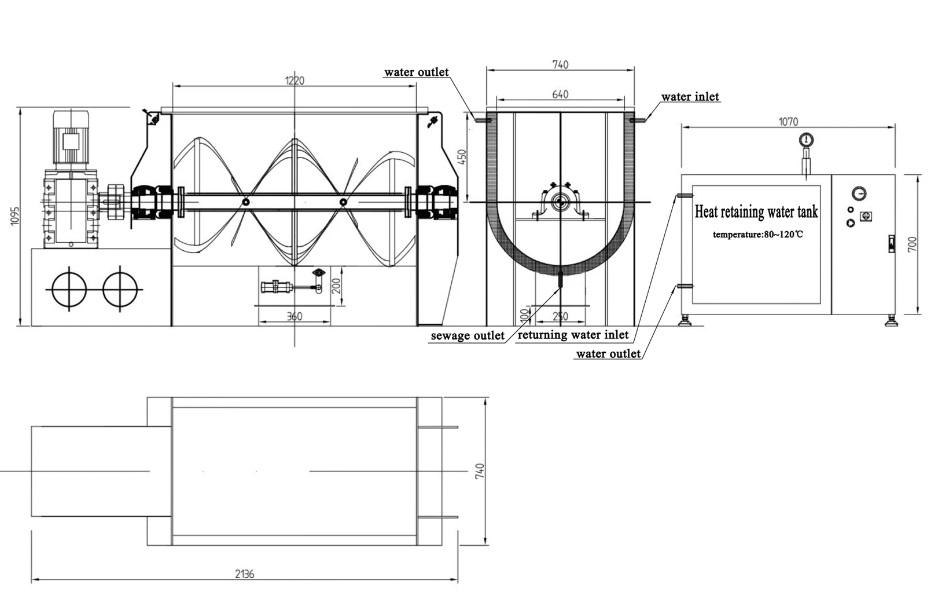
Structure and features:
The U-shaped containers incorporate robust mixing blades and transmission components, featuring a unique U-shaped cylinder structure known as the “ChangTi cylinder.” This design ensures minimal resistance during the movement of mixed materials, which can be in the form of powders or semiliquids, within the cylinder.
To create an efficient mixing environment with low power consumption, both positive and negative rotation ribbons are installed on the same horizontal axis. These ribbons create a dynamic mixing process. Additionally, spiral strip blades, consisting of either a double or triple layer, are placed on the outer spiral surfaces of the cylinder. These spirals facilitate the movement of materials from two sides towards the central pool.
Simultaneously, inner spiral materials are transported from the central pool towards both sides of the cylinder. This dual-directional movement induces a vortex effect within the materials at lower power levels. Consequently, this setup accelerates the mixing speed and significantly enhances the uniformity of the mixing process.
Discharging mode:
The spacious design of this system offers some valuable advantages when working with pneumatic materials. One key benefit is the ability to discharge completely without leaving any residues behind. To handle either finely ground materials or semiliquids, you can choose between manual butterfly valves or pneumatic butterfly valves.
Furthermore, this system can be equipped with a heating or cooling jacket for precise temperature control. The heating options include electric heating and heat conduction oil heating, offering flexibility based on your specific needs. Cooling is achieved either through a direct water jacket or a large heat exchange area, ensuring rapid cooling.
In smaller mixers, a simple reducer direct-drive mechanism is used, characterized by its straightforward structure and high operational reliability. Maintenance is also convenient in these cases. In contrast, larger mixers employ a pulley-driven system with a cycloid speed reducer. This setup features an elastic connection that offers the advantage of overload protection during operation.
What is Ribbon Blender?
A ribbon mixer blender is a type of blender designed for lighter mixing tasks, primarily used with pre-processed powder components such as dried granules and pre-sieved powders. This blender operates with low shear, making it ideal for solid-solid mixing. It can also handle solid-liquid mixing when a high shearing force isn’t needed.
One of its advantages is that it takes up less vertical space compared to larger volume mixers, making it a space-efficient choice.
The principle of Ribbon Blender:
Ribbon blenders work based on a combination of convection and diffusion mechanisms.
Convection mixing involves the larger-scale movement of solid materials. This happens when the solids are rotated along the horizontal axis of the agitator assembly.
On the other hand, diffusion mixing focuses on the micro-level blending, where individual particles move relative to the particles around them. In a ribbon blender, diffusion occurs as particles in front of the ribbon move in one direction while nearby particles either remain still or lag behind.
These dual mechanisms, convection and diffusion, work together to effectively mix and blend solid materials in the blender.
Business Type: | Manufacturer/Factory | Main Products: | Mill, grinder, granulator, mixer, Crushing Equipment |
Number of Employees: | 100 | Year of Establishment: | 2014.05 |
Production Capacity | 5000Set/Year | After-sales Service: | Technical Support; on-line teach lessons |
R&D Capacity: | ODM, OEM | Annual Output Value: | US$5 Million – US$10 Million |
No. of R&D Staff: | 5 | No. of Production Lines: | 6 |
LK Mixer is a professional manufacturer for grinder, mixer and pulverizer. These machines are widely used in pharmaceutical, cosmetic, health care products and chemical industries. Our main product including granulating machine, grinder, mixer, dryer, etc. All mechanical products in accordance with the China GMP design requirements. And also we have other certifications such as CE, UL for motors.
Business Philosophy
“Quality is the main policy of sales” and “integrity is the principle of success” are the business philosophy of our people. We carry out one-year warranty, lifelong maintenance service, with technical consultation, with material test machine and other services, and long-term supply of equipment. Welcome new and old customers to negotiate cooperation!
Certifications:
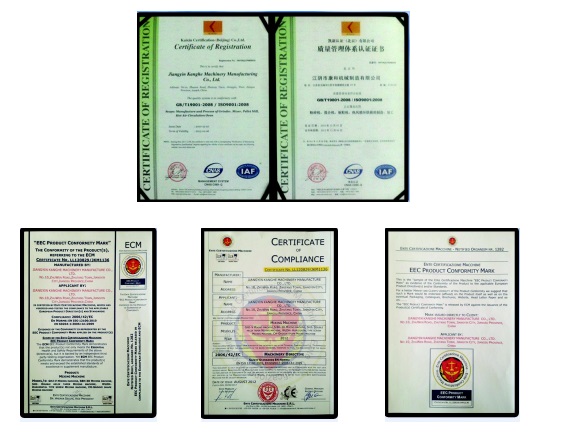
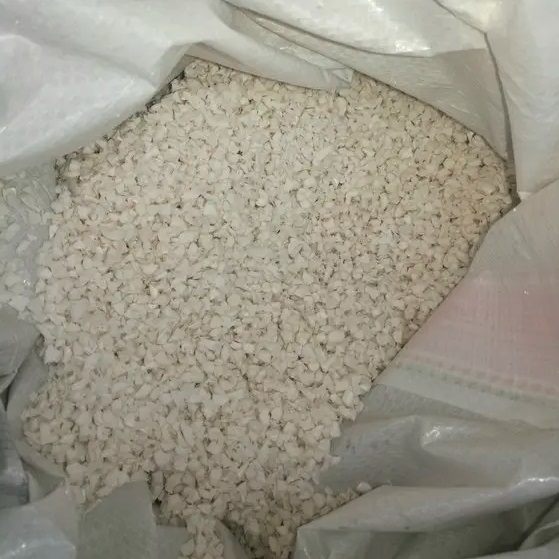
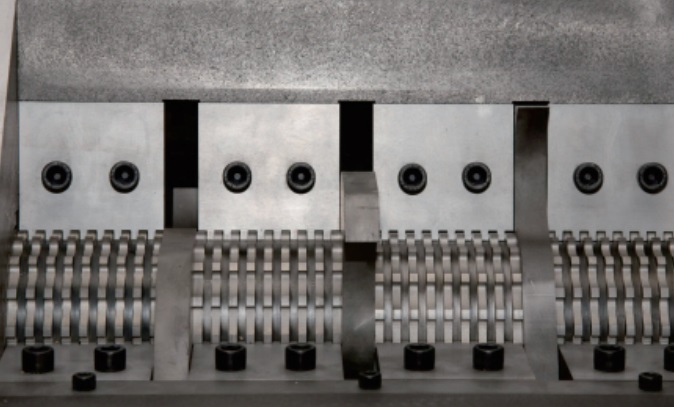
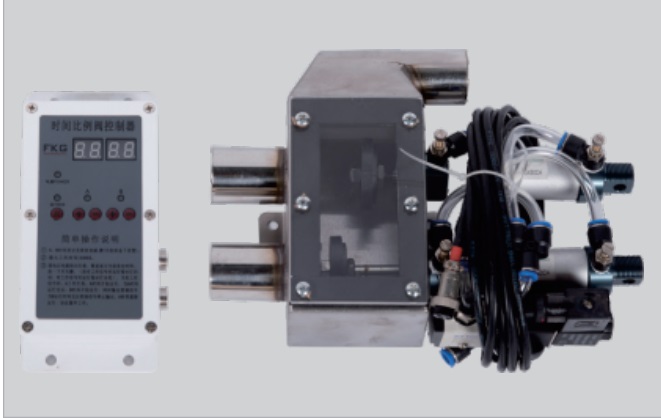
Electric Cabinet with UL Certification
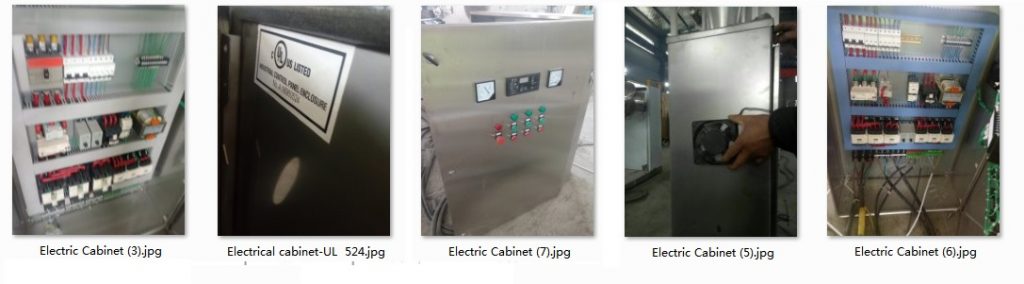
Cyclone Processor and Motors:
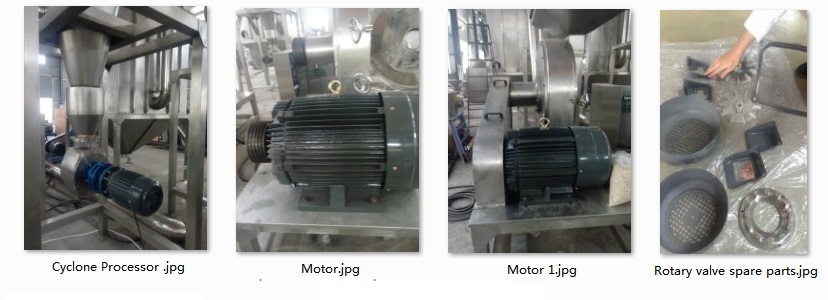
Spare Parts:
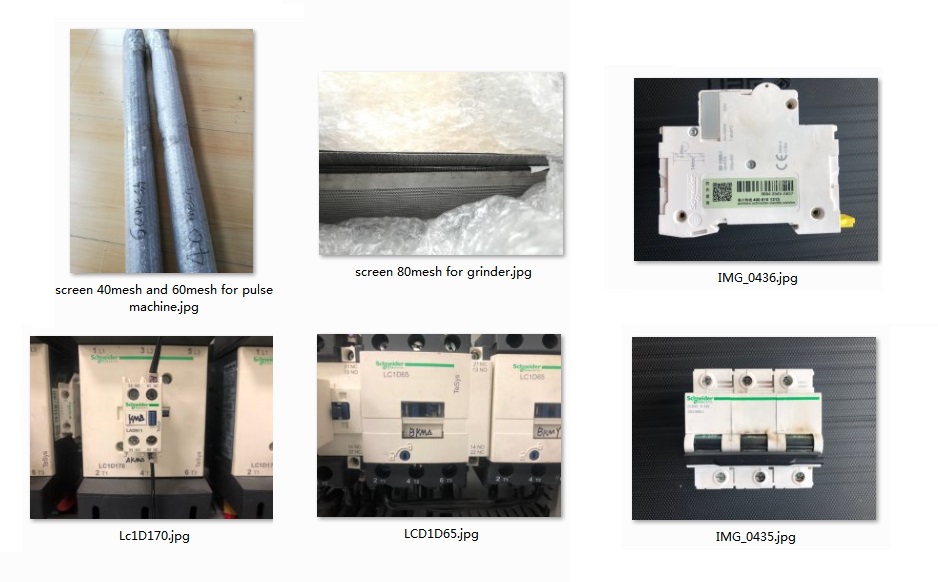
Small Machine Packing:
Small machine packed with export fumigation-free wooden cases, goes with bulk shipment or in container.
When packing small machines for sea shipment, it is important to take measures to ensure that the machines are protected from damage during transit. Here are some general steps that a manufacturer may follow when packing small machines for sea shipment:
- Clean and dry the machine: Before packing, the machine should be thoroughly cleaned and dried to prevent any moisture or debris from causing damage during transit.
- Disassemble the machine: If possible, the machine should be disassembled into its component parts to reduce its overall size and make it easier to pack.
- Wrap the machine in protective material: The machine should be wrapped in a layer of protective material, such as bubble wrap or foam, to protect it from scratches and impact during transit.
- Place the machine in a sturdy box: The wrapped machine should then be placed in a sturdy box that is appropriate for the size and weight of the machine. The box should be made of durable material, such as corrugated cardboard or plywood, and should be able to withstand the rigors of sea transit.
- Add packing material: The box should be filled with packing material, such as packing peanuts or air pillows, to provide cushioning and prevent the machine from shifting during transit.
- Seal the box: The box should be securely sealed with high-quality packing tape to prevent it from opening during transit.
- Label the box: The box should be clearly labeled with the machine’s name, weight, and any other relevant information, as well as the destination address and contact information.
Overall, the goal is to pack the small machine in a way that will protect it from damage during transit and ensure that it arrives at its destination in good condition. It is important to follow proper packing procedures and use high-quality packing materials to minimize the risk of damage during sea shipment.
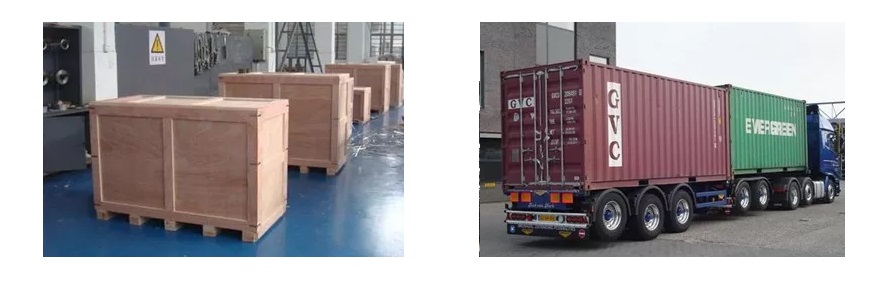
Large Machine Packing:
Packing a large machine for sea shipment can be a complex and challenging task. However, with careful planning and attention to detail, it is possible to pack a large machine for sea shipment in a way that will ensure that it arrives at its destination in good condition. Here are some general steps that a manufacturer may follow when packing up a large machine for sea shipment:
- Clean and prepare the machine: Before packing, the machine should be thoroughly cleaned and prepared. All fluids, such as oil or coolant, should be drained, and any loose or detachable parts should be removed.
- Disassemble the machine: If possible, the machine should be disassembled into its component parts to reduce its overall size and make it easier to pack. Each part should be carefully labeled and numbered to ensure that it can be easily reassembled at the destination.
- Protect delicate parts: Delicate or fragile parts should be wrapped in protective material, such as bubble wrap or foam, to protect them from damage during transit.
- Build a custom crate: A custom crate should be built around the machine to provide a secure and sturdy enclosure. The crate should be made of durable material, such as plywood, and should be designed to fit the machine snugly. The crate should also include braces or supports to prevent the machine from shifting during transit.
- Add cushioning material: The crate should be filled with cushioning material, such as packing peanuts or air pillows, to provide extra protection and prevent the machine from moving or shifting during transit.
- Securely fasten the machine: The machine should be securely fastened to the crate to prevent it from moving or shifting during transit. This may involve using straps, bolts, or other fasteners to hold the machine in place.
- Seal and label the crate: The crate should be securely sealed with high-quality packing tape, and should be clearly labeled with the machine’s name, weight, and any other relevant information. The destination address and contact information should also be clearly marked on the crate.
Overall, packing a large machine for sea shipment requires careful planning and attention to detail. It is important to use high-quality materials and follow proper packing procedures to ensure that the machine arrives at its destination in good condition. A professional packing and shipping company may be consulted to ensure that the machine is properly packed and prepared for sea shipment.
Customer Side Machine Groups Showcase Videos:
Dust Collector Shipment
Shipment – Packing Method
Two Large Industrial Grinder Ready to Ship
Domestic Shipment Show Case:
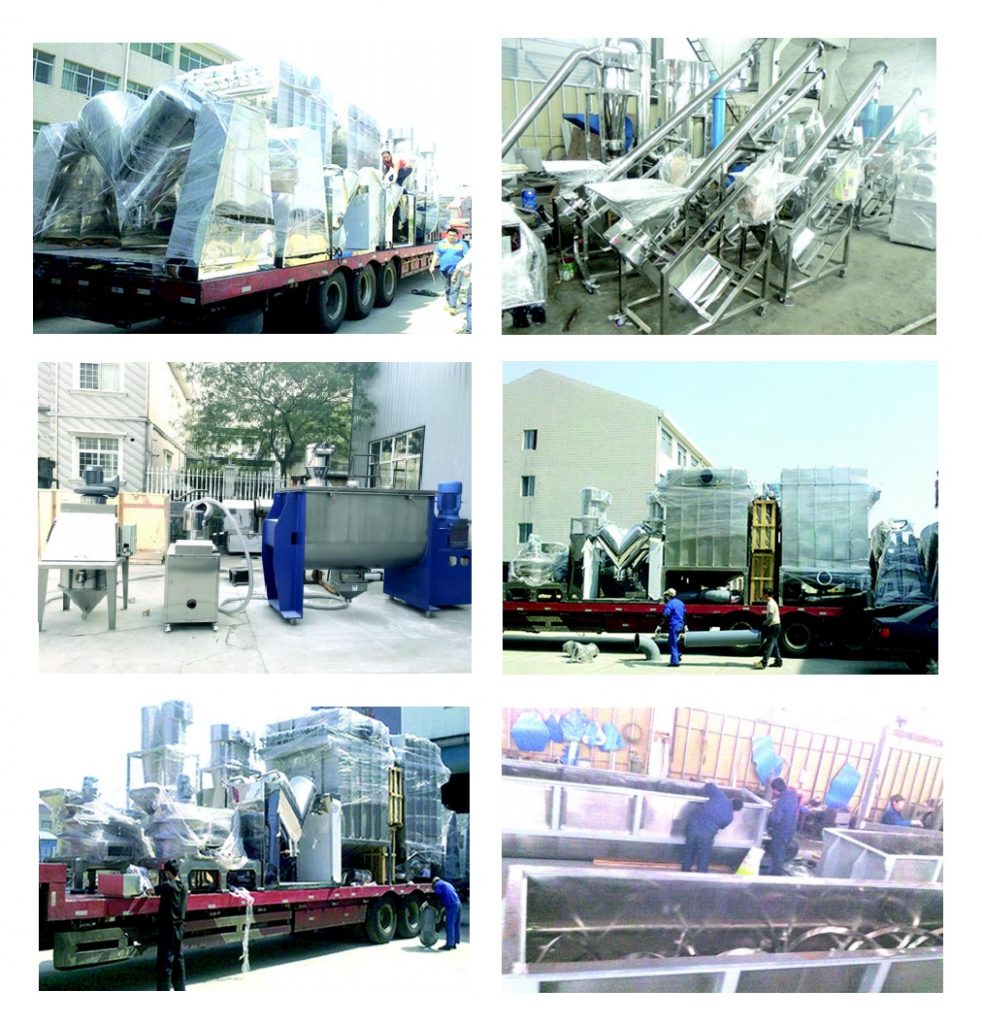
Installation Layout:
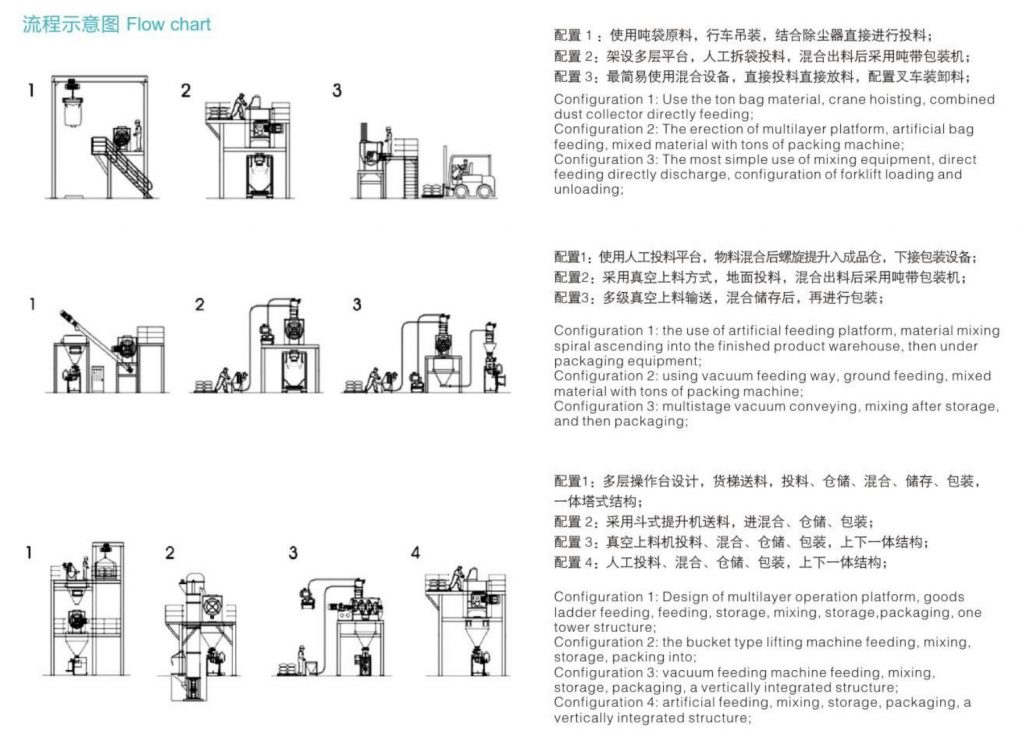
Maintenance and Safety Measures
Proper maintenance practices for the machine
Proper maintenance practices are essential for ensuring the efficient and safe operation of a universal grinder. Here are some maintenance practices that should be followed:
- Regular cleaning – The machine should be cleaned regularly to remove any debris, dust, or coolant that may accumulate on the machine’s surfaces. This can be done using a soft brush, air hose, or a cleaning solution.
- Lubrication – The machine’s moving parts should be lubricated regularly to reduce friction and wear. The manufacturer’s recommendations for lubrication intervals and types should be followed.
- Inspection – The machine should be inspected regularly for any signs of wear, damage, or misalignment. Any issues should be addressed immediately to prevent further damage or safety hazards.
- Replacement of worn or damaged parts – Worn or damaged parts should be replaced immediately with genuine parts from the manufacturer.
- Calibration – The machine should be calibrated regularly to ensure that it is operating within the specified tolerances and accuracy.
- Operator training – Proper operator training is essential for ensuring the safe and efficient operation of the machine. Operators should be trained on the proper operation, maintenance, and safety procedures for the machine.
- Record keeping – A maintenance log should be kept to track the machine’s maintenance history, including cleaning, lubrication, inspection, and repairs. This can help identify any trends or issues that need to be addressed.
Following these maintenance practices can help ensure the safe and efficient operation of a universal grinder, prolong its lifespan, and reduce the risk of downtime and costly repairs.
Safety measures for operators and workers
Safety measures for operators and workers are crucial when using a universal grinder. Here are some safety measures that should be followed:
- Personal protective equipment (PPE) – Operators and workers should wear appropriate PPE, including safety glasses, hearing protection, gloves, and safety shoes.
- Machine guards – The machine should be equipped with proper machine guards to prevent access to the grinding wheel during operation. The guards should be in good condition and properly installed.
- Lockout/tagout procedures – Lockout/tagout procedures should be followed to ensure that the machine is not accidentally started or energized during maintenance or repair.
- Training – Operators and workers should receive proper training on the safe operation of the machine, including the use of PPE, machine guards, and lockout/tagout procedures.
- Inspection – The machine should be inspected regularly for any signs of wear, damage, or misalignment that may pose a safety hazard.
- Proper use of grinding wheels – Operators should ensure that the grinding wheel is properly installed, dressed, and aligned. The grinding wheel should not be overloaded or forced into the material being ground.
- Proper handling of coolant – If coolant is used, operators should ensure that it is properly mixed, applied, and contained. Coolant should not be allowed to accumulate on the floor, as it can create a slipping hazard.
- Emergency procedures – Emergency procedures should be established and communicated to all operators and workers in case of an accident or injury.
Following these safety measures can help prevent accidents and injuries when using a universal grinder. It is important to prioritize safety and ensure that all operators and workers are trained and informed about the potential hazards of the machine.
Features of Ribbon Blender:
Our equipment comes in two distinct shapes to suit different volume needs: U-shape, ideal for low to medium capacity operations with a single shaft, and W-shape, designed for large to mega-volume operations with double shafts.
To maintain the highest standards of hygiene, all components that come into contact with materials are made of stainless steel 316. We’ve taken extra precautions by mounting bearings on lanterns outside the mixing zone to prevent any cross-contamination.
Our design also simplifies material handling by offering a convenient side discharge feature for processed materials. Rest assured, our equipment complies with all cGMP/cGEP standards to meet industry requirements.
To ensure even better control over cross-contamination, we’ve incorporated air purges on the side entry seals. Additionally, our continuous ribbon design ensures thorough discharge of the finished product.
For a quieter working environment and reduced maintenance needs, our power transmission is belt-driven. For those handling fragile materials, we offer a paddle-style agitator option instead of a ribbon, providing gentler blending.
Our equipment’s capacity ranges from 125 liters to 8,400 liters, and we can even provide larger volumes of up to 20,000 liters if needed.
Universal Grinder Youtube Video (See More)
About LKMixer
LKMixer is a professional manufacturer for fertilizer production line, grinder, mixer and granulator, shredder. These machines are widely used in food, pharmaceutical, cosmetic, health care products and chemical industries. The Food materials like Peanut, mushroom, seeds, potato, bean, tobacco, salt, cannabis, tea, Sugar, corn, Coffee, rice, pepper, grain as so on. Grinders have many types such as Pulse Dust Grinder which suitable for zero pollution environment, Turbine Mill which is suitable for coffee bean, 12-120mesh all can meet, Ultrafine Grinding Mill covers 80-200mesh, and also Winnowing Dust Grinder or other grinding machines like SF Hammer. Welcome to contact us for details. Contact us for more information. Proposal, catalog, quotation. Mobile/WhatsApp: +86 18019763531 Tel: +86 21 66037855 Email: sales@lkmixer.com