WCH Horizontal Tank Mixer
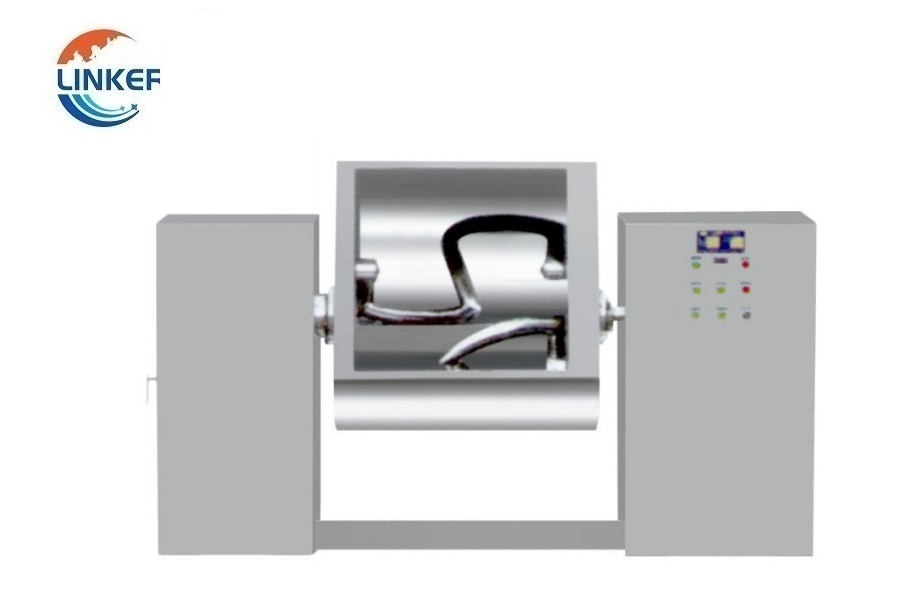
WCH Double Pulp Tank Mixer
- Suitable Blending Material: Dry Powder , Wet Powder, advocate complementary material, suitable for mixed semi-solid liquid materials or viscosity is too large.
- Batch Volumn: 100-600L;
- Stirring Speed: 24 r/min;
- Machine Weight:450-1300(KG);
- Total Power: 4-11kw
- Application: Pharmaceuticals, chemical, food.
- Price: Cost around $188~7659.(Depend on Models and special customization).
- HS code: 8479820090
Parameters of Horizontal Tank Mixer:
Model | WCH-100 | WCH-200 | WCH-300 | WCH-400 | WCH-500 |
Working Volume(L) | 100 | 200 | 300 | 400 | 500 |
Motor Power(KW) | 4 | 5.5 | 5.5 | 7.5 | 11 |
Stirring Speed(r/min) | 24 | 24 | 24 | 24 | 24 |
Pour Material Angle | 45 | 45 | 45 | 45 | 45 |
Weight(KG) | 450 | 650 | 800 | 1000 | 1300 |
Dimension(mm) | 1600*600*1100 | 1800*700*1200 | 2000*800*1200 | 2200*900*1300 | 2300*950*1400 |
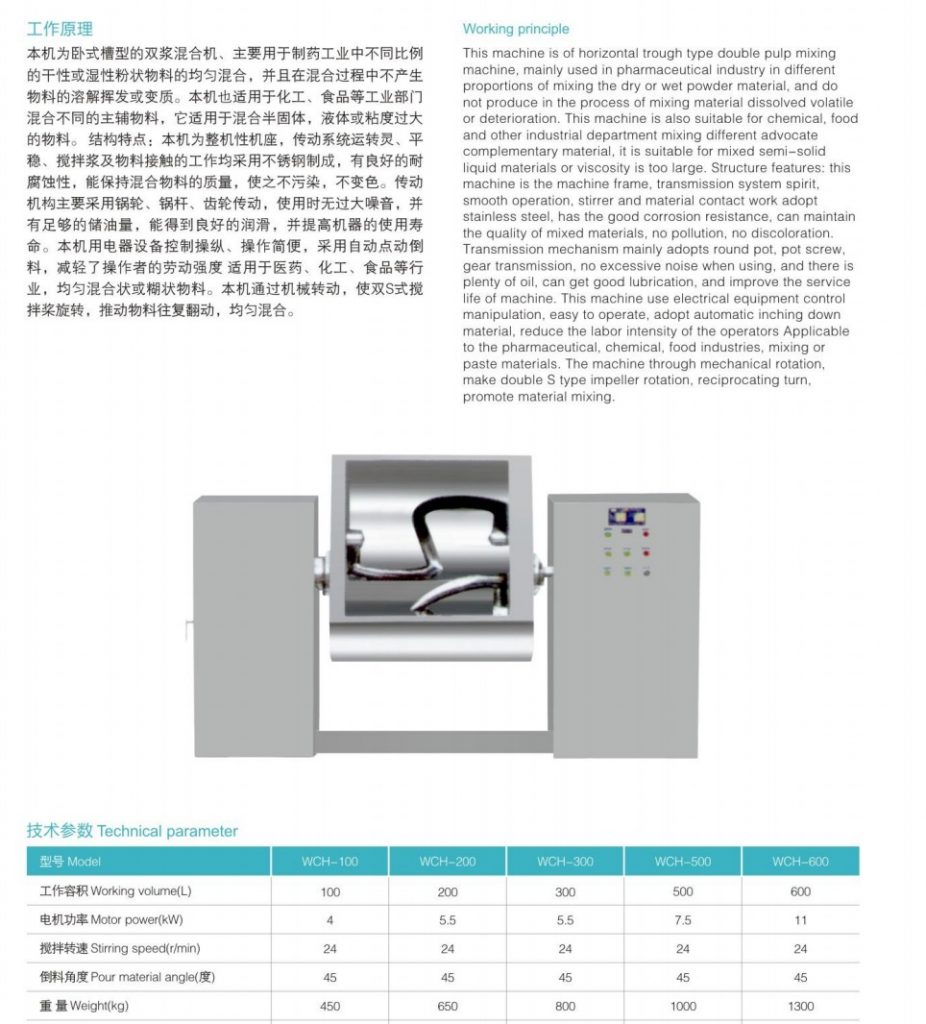
What is Horizontal Tank Mixer?
A horizontal tank mixer is a type of equipment used in various industries to blend or mix substances. Unlike vertical mixers, which stand upright, horizontal tank mixers are designed with a horizontal orientation. They are commonly used in applications such as food processing, chemical manufacturing, and pharmaceutical production.
These mixers typically consist of a tank-shaped container lying on its side, equipped with an agitator or mixing device. The agitator can be customized to suit the specific materials being mixed. It rotates within the tank to thoroughly combine ingredients and create a consistent mixture.
One of the key advantages of horizontal tank mixers is their ability to provide a more uniform blend of materials, which can be crucial for certain applications. Additionally, they are well-suited for incorporating ingredients with low inclusion rates, often as low as 1 kg per metric ton. This precision makes them particularly useful in industries where accurate mixing is essential.
Horizontal mixers also tend to have little or no residue left in the tank after mixing, thanks to their design, which ensures complete discharge of the mixed material. This is a notable advantage in applications where cross-contamination or leftover material can be problematic.
In summary, a horizontal tank mixer is a specialized mixing equipment with a horizontal design, ideal for applications requiring precise and uniform blending of ingredients while minimizing leftover residue in the tank.
Structure(Design):
A Tank Mixer comprises several key components, including a tank cover, tank mixer motor,an agitator, bearings, a driving mechanism, and a sealing device. Depending on your requirements, you can also add heating or cooling equipment to the tank.
Both the tank body and cover come with various features like inlets, outlets, observation ports, temperature and pressure gauges, steam distillation ports, and safety vents. The type of agitator used can vary based on the specific production process, with options such as paddle, anchored, frame, or propeller types. If needed, the factory can customize the design to meet your specific needs.
Application:
A Tank Mixer is a hygienic and clean piece of equipment with a fully enclosed vertical design. It comes equipped with functions for heating, cooling, insulating, and mixing. This versatile tank is specially designed for use in the food, dairy, beverage, pharmaceutical, winemaking, flavor, and chemical industries.
The tanks feature a jacketed layer, allowing you to heat or cool the contents by introducing steam or cooling water. The agitator within the tank ensures that the materials are thoroughly mixed at the most suitable temperature.
What does a tank mixer do?
A tank mixer plays a crucial role in winemaking by ensuring that everything inside the tank, like the grape juice and other ingredients, is mixed thoroughly. This gentle stirring action takes place during fermentation, maintaining an even temperature and making sure yeast and nutrients are evenly distributed. It’s also handy when it comes to creating a uniform blend before the wine is bottled, ensuring that every bottle of wine is consistent in quality.
Horizontal Tank Mixer is ideal for blending various ingredients, such as short doughs, tortillas, fillings, pie doughs, health breads, cheesecakes, muffin batter, and a range of other recipes. These mixers come with different mixing arms that can be tailored to the specific type of dough or mixture you’re working with, offering a high degree of customization.
Technical Performance:
Heating Method: The tank can be heated using either steam or electrical heating to generate heat for material sterilization.
Working Principle(tank mixer design):
This machine is a horizontal trough-type double-paddle mixer, primarily used in the pharmaceutical industry to uniformly mix dry or wet powdered materials in different proportions. During the mixing process, it does not cause material dissolution, evaporation, or deterioration. The machine is also suitable for the chemical and food industries, where it mixes different main and auxiliary materials, making it ideal for mixing semi-solids, liquids, or highly viscous materials.
Structural features: The machine has an integral frame, and its transmission system operates smoothly. The mixing paddles and parts that come into contact with materials are made of stainless steel, providing excellent corrosion resistance to maintain the quality of the mixed materials without contamination or discoloration. The transmission mechanism mainly uses pot wheels, pot rods, and gear drives, resulting in minimal noise during operation. It also has sufficient oil storage capacity for effective lubrication, enhancing the machine’s lifespan. The machine is equipped with electrical controls for easy operation and utilizes automatic incremental feeding, reducing the operator’s workload. It is suitable for the pharmaceutical, chemical, and food industries for mixing uniform or pasty materials. The machine achieves uniform mixing through mechanical rotation, causing the dual-S-shaped mixing blades to rotate, propelling the materials to flip back and forth evenly.
How to Calculate the Volume of tank mixer (gallon to liter)?
To convert gallons to liters, you can use the conversion factor of 1 US gallon being approximately equal to 3.78541 liters. Here are the conversions for the given tank mixers:
- 5 gallon tank mixer:
5 gallons × 3.78541 liters/gallon ≈ 18.93 liters - 30 gallon tank mixer:
30 gallons × 3.78541 liters/gallon ≈ 113.56 liters - 300 gallon tank mixer:
300 gallons × 3.78541 liters/gallon ≈ 1,135.14 liters - 500 gallon tank mixer:
500 gallons × 3.78541 liters/gallon ≈ 1,892.71 liters - 1000 gallon tank mixer:
1000 gallons × 3.78541 liters/gallon ≈ 3,785.41 liters
So, the tank mixers in liters are approximately as follows:
- 1000 gallon tank mixer ≈ 3,785.41 liters
- 30 gallon tank mixer ≈ 113.56 liters
- 300 gallon tank mixer ≈ 1,135.14 liters
- 5 gallon tank mixer ≈ 18.93 liters
- 500 gallon tank mixer ≈ 1,892.71 liters
Business Type: | Manufacturer/Factory | Main Products: | Mill, grinder, granulator, mixer, Crushing Equipment |
Number of Employees: | 100 | Year of Establishment: | 2014.05 |
Production Capacity | 5000Set/Year | After-sales Service: | Technical Support; on-line teach lessons |
R&D Capacity: | ODM, OEM | Annual Output Value: | US$5 Million – US$10 Million |
No. of R&D Staff: | 5 | No. of Production Lines: | 6 |
LK Mixer is a professional manufacturer for grinder, mixer and pulverizer. These machines are widely used in pharmaceutical, cosmetic, health care products and chemical industries. Our main product including granulating machine, grinder, mixer, dryer, etc. All mechanical products in accordance with the China GMP design requirements. And also we have other certifications such as CE, UL for motors.
Business Philosophy
“Quality is the main policy of sales” and “integrity is the principle of success” are the business philosophy of our people. We carry out one-year warranty, lifelong maintenance service, with technical consultation, with material test machine and other services, and long-term supply of equipment. Welcome new and old customers to negotiate cooperation!
Certifications:
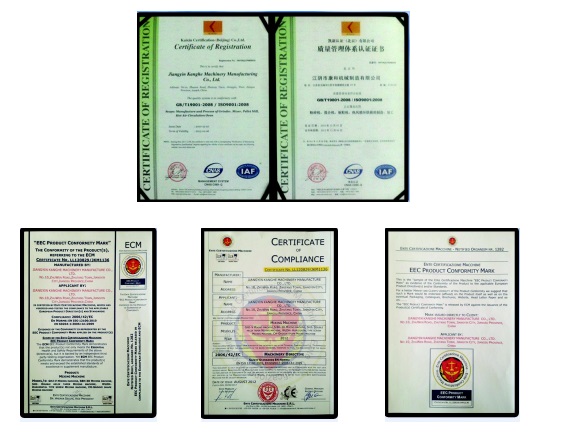
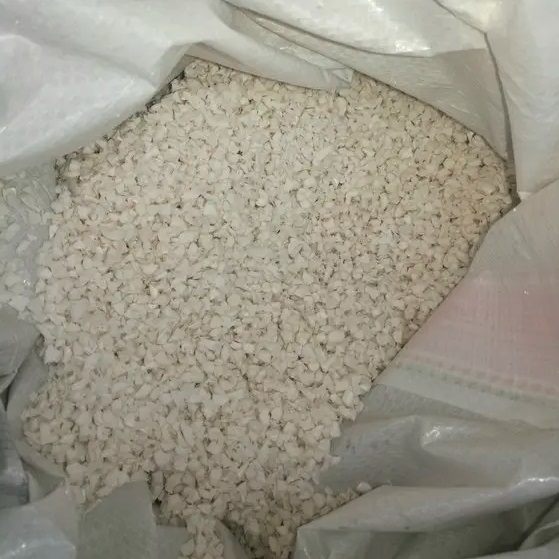
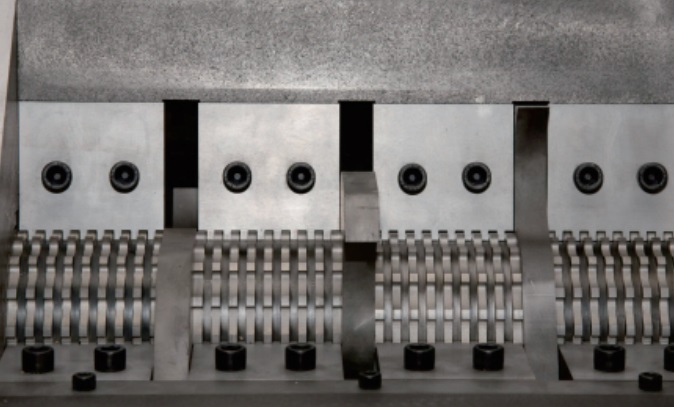
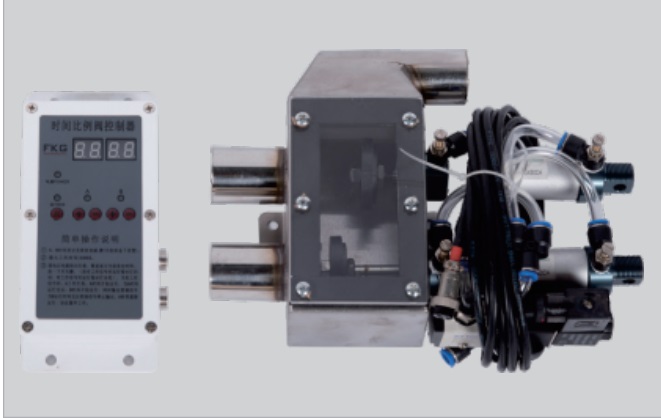
Electric Cabinet with UL Certification
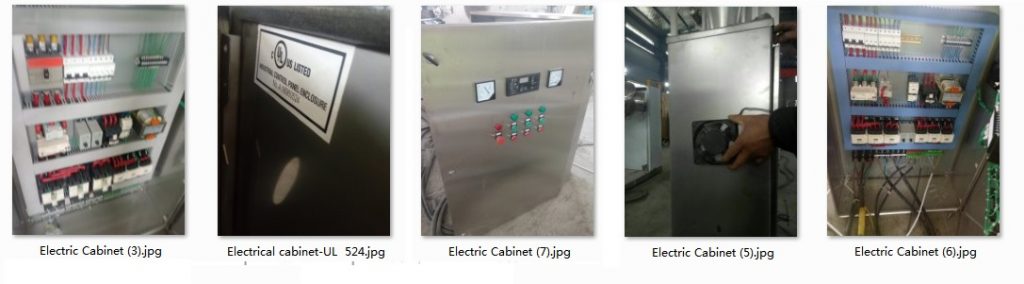
Cyclone Processor and Motors:
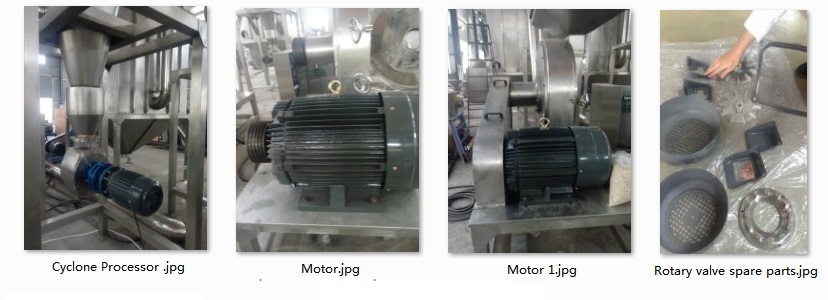
Spare Parts:
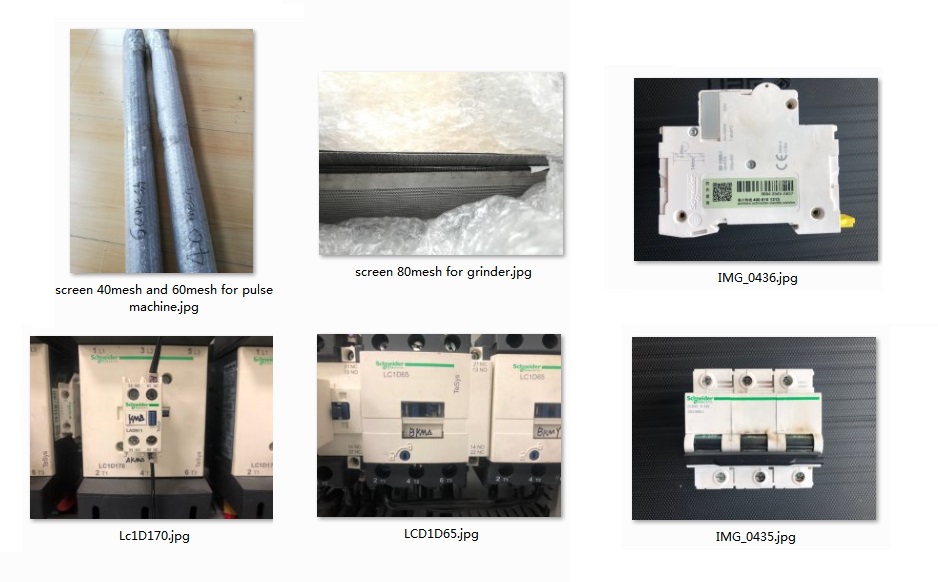
Small Machine Packing:
Small machine packed with export fumigation-free wooden cases, goes with bulk shipment or in container.
When packing small machines for sea shipment, it is important to take measures to ensure that the machines are protected from damage during transit. Here are some general steps that a manufacturer may follow when packing small machines for sea shipment:
- Clean and dry the machine: Before packing, the machine should be thoroughly cleaned and dried to prevent any moisture or debris from causing damage during transit.
- Disassemble the machine: If possible, the machine should be disassembled into its component parts to reduce its overall size and make it easier to pack.
- Wrap the machine in protective material: The machine should be wrapped in a layer of protective material, such as bubble wrap or foam, to protect it from scratches and impact during transit.
- Place the machine in a sturdy box: The wrapped machine should then be placed in a sturdy box that is appropriate for the size and weight of the machine. The box should be made of durable material, such as corrugated cardboard or plywood, and should be able to withstand the rigors of sea transit.
- Add packing material: The box should be filled with packing material, such as packing peanuts or air pillows, to provide cushioning and prevent the machine from shifting during transit.
- Seal the box: The box should be securely sealed with high-quality packing tape to prevent it from opening during transit.
- Label the box: The box should be clearly labeled with the machine’s name, weight, and any other relevant information, as well as the destination address and contact information.
Overall, the goal is to pack the small machine in a way that will protect it from damage during transit and ensure that it arrives at its destination in good condition. It is important to follow proper packing procedures and use high-quality packing materials to minimize the risk of damage during sea shipment.
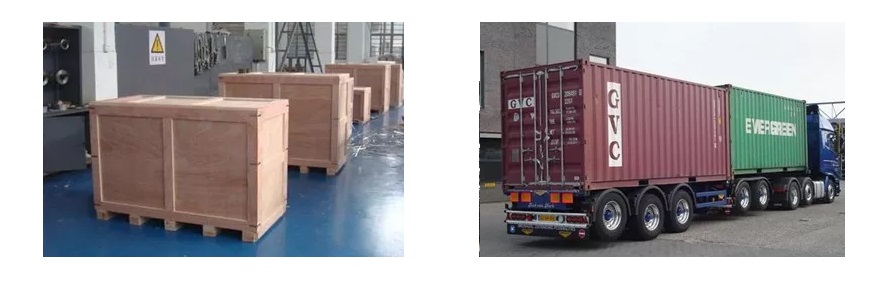
Large Machine Packing:
Packing a large machine for sea shipment can be a complex and challenging task. However, with careful planning and attention to detail, it is possible to pack a large machine for sea shipment in a way that will ensure that it arrives at its destination in good condition. Here are some general steps that a manufacturer may follow when packing up a large machine for sea shipment:
- Clean and prepare the machine: Before packing, the machine should be thoroughly cleaned and prepared. All fluids, such as oil or coolant, should be drained, and any loose or detachable parts should be removed.
- Disassemble the machine: If possible, the machine should be disassembled into its component parts to reduce its overall size and make it easier to pack. Each part should be carefully labeled and numbered to ensure that it can be easily reassembled at the destination.
- Protect delicate parts: Delicate or fragile parts should be wrapped in protective material, such as bubble wrap or foam, to protect them from damage during transit.
- Build a custom crate: A custom crate should be built around the machine to provide a secure and sturdy enclosure. The crate should be made of durable material, such as plywood, and should be designed to fit the machine snugly. The crate should also include braces or supports to prevent the machine from shifting during transit.
- Add cushioning material: The crate should be filled with cushioning material, such as packing peanuts or air pillows, to provide extra protection and prevent the machine from moving or shifting during transit.
- Securely fasten the machine: The machine should be securely fastened to the crate to prevent it from moving or shifting during transit. This may involve using straps, bolts, or other fasteners to hold the machine in place.
- Seal and label the crate: The crate should be securely sealed with high-quality packing tape, and should be clearly labeled with the machine’s name, weight, and any other relevant information. The destination address and contact information should also be clearly marked on the crate.
Overall, packing a large machine for sea shipment requires careful planning and attention to detail. It is important to use high-quality materials and follow proper packing procedures to ensure that the machine arrives at its destination in good condition. A professional packing and shipping company may be consulted to ensure that the machine is properly packed and prepared for sea shipment.
Customer Side Machine Groups Showcase Videos:
Dust Collector Shipment
Shipment – Packing Method
Two Large Industrial Grinder Ready to Ship
Domestic Shipment Show Case:
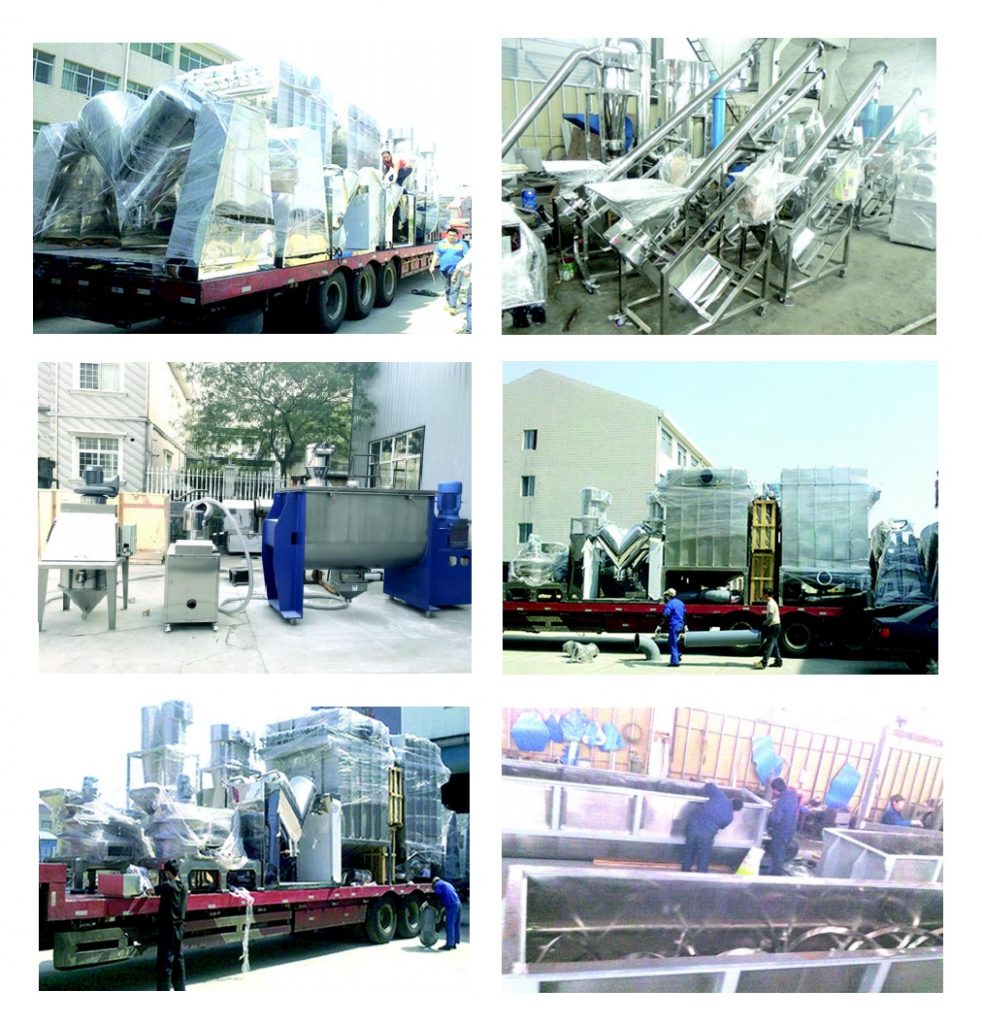
Installation Layout:
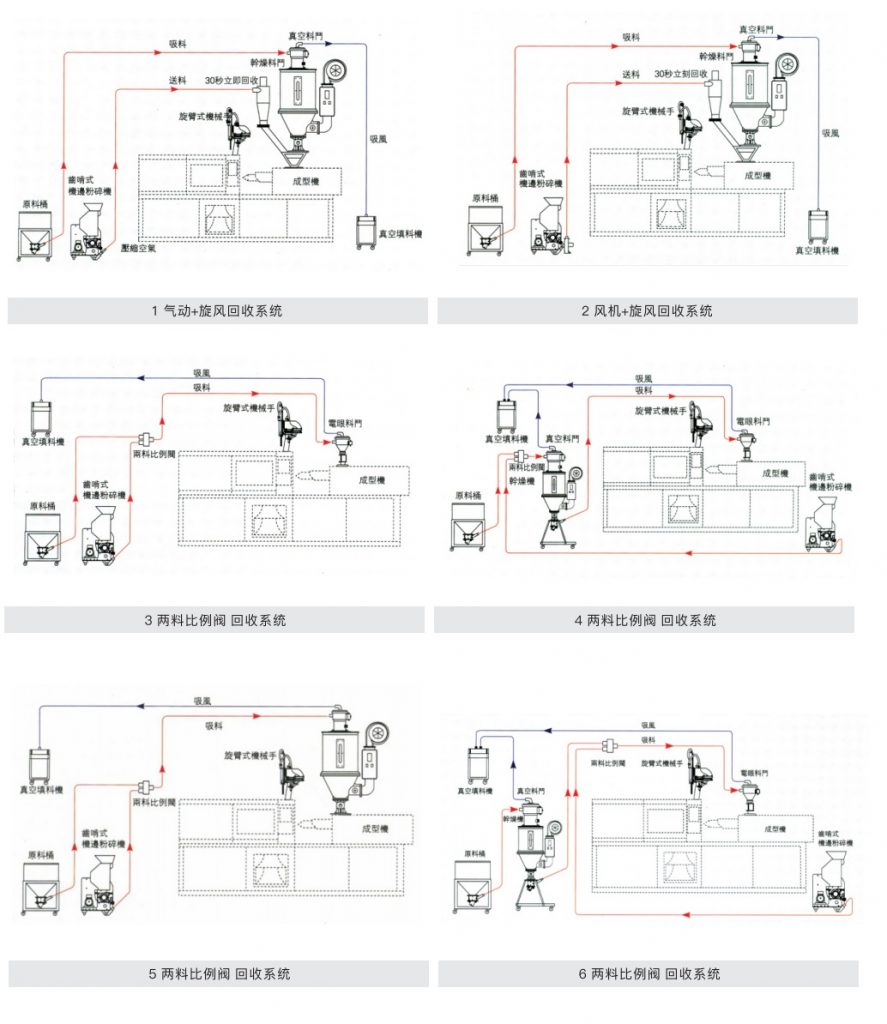
Maintenance and Safety Measures
Proper maintenance practices for the machine
Proper maintenance practices are essential for ensuring the efficient and safe operation of a universal grinder. Here are some maintenance practices that should be followed:
- Regular cleaning – The machine should be cleaned regularly to remove any debris, dust, or coolant that may accumulate on the machine’s surfaces. This can be done using a soft brush, air hose, or a cleaning solution.
- Lubrication – The machine’s moving parts should be lubricated regularly to reduce friction and wear. The manufacturer’s recommendations for lubrication intervals and types should be followed.
- Inspection – The machine should be inspected regularly for any signs of wear, damage, or misalignment. Any issues should be addressed immediately to prevent further damage or safety hazards.
- Replacement of worn or damaged parts – Worn or damaged parts should be replaced immediately with genuine parts from the manufacturer.
- Calibration – The machine should be calibrated regularly to ensure that it is operating within the specified tolerances and accuracy.
- Operator training – Proper operator training is essential for ensuring the safe and efficient operation of the machine. Operators should be trained on the proper operation, maintenance, and safety procedures for the machine.
- Record keeping – A maintenance log should be kept to track the machine’s maintenance history, including cleaning, lubrication, inspection, and repairs. This can help identify any trends or issues that need to be addressed.
Following these maintenance practices can help ensure the safe and efficient operation of a universal grinder, prolong its lifespan, and reduce the risk of downtime and costly repairs.
Safety measures for operators and workers
Safety measures for operators and workers are crucial when using a universal grinder. Here are some safety measures that should be followed:
- Personal protective equipment (PPE) – Operators and workers should wear appropriate PPE, including safety glasses, hearing protection, gloves, and safety shoes.
- Machine guards – The machine should be equipped with proper machine guards to prevent access to the grinding wheel during operation. The guards should be in good condition and properly installed.
- Lockout/tagout procedures – Lockout/tagout procedures should be followed to ensure that the machine is not accidentally started or energized during maintenance or repair.
- Training – Operators and workers should receive proper training on the safe operation of the machine, including the use of PPE, machine guards, and lockout/tagout procedures.
- Inspection – The machine should be inspected regularly for any signs of wear, damage, or misalignment that may pose a safety hazard.
- Proper use of grinding wheels – Operators should ensure that the grinding wheel is properly installed, dressed, and aligned. The grinding wheel should not be overloaded or forced into the material being ground.
- Proper handling of coolant – If coolant is used, operators should ensure that it is properly mixed, applied, and contained. Coolant should not be allowed to accumulate on the floor, as it can create a slipping hazard.
- Emergency procedures – Emergency procedures should be established and communicated to all operators and workers in case of an accident or injury.
Following these safety measures can help prevent accidents and injuries when using a universal grinder. It is important to prioritize safety and ensure that all operators and workers are trained and informed about the potential hazards of the machine.
Electric Mixer Tank for Sale (Stainless Steel):
Universal Grinder Youtube Video (See More)
About LKMixer
LKMixer is a professional manufacturer for fertilizer production line, grinder, mixer and granulator, shredder. These machines are widely used in food, pharmaceutical, cosmetic, health care products and chemical industries. The Food materials like Peanut, mushroom, seeds, potato, bean, tobacco, salt, cannabis, tea, Sugar, corn, Coffee, rice, pepper, grain as so on. Grinders have many types such as Pulse Dust Grinder which suitable for zero pollution environment, Turbine Mill which is suitable for coffee bean, 12-120mesh all can meet, Ultrafine Grinding Mill covers 80-200mesh, and also Winnowing Dust Grinder or other grinding machines like SF Hammer. Welcome to contact us for details. Contact us for more information. Proposal, catalog, quotation. Mobile/WhatsApp: +86 18019763531 Tel: +86 21 66037855 Email: sales@lkmixer.com