GHJ V Blender High Efficient
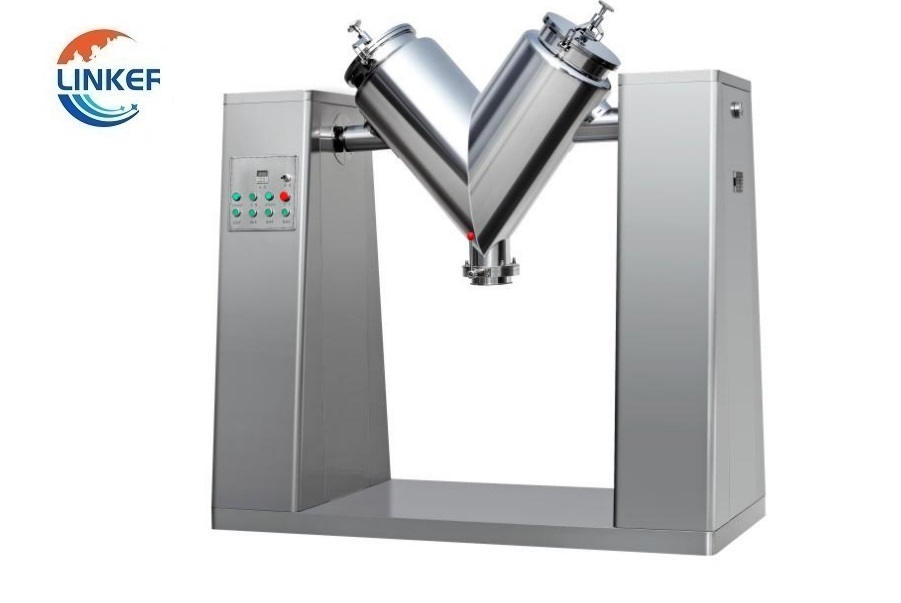
- Suitable Blending Material: Dry Powder , Dry Granule
- Maximum mixing volume: 72-2400(kg/each time);
- Volumn: 0.18~6㎥;
- Mixing Speed: 10~12;
- Machine Weight:280~3580(kg);
- Total Power: 1.1~18.5kg
- Application: Pharmaceuticals, Nutraceuticals, Food Products, Chemicals, Fertilizer, Stucco, Clay, Potting Soils, Paint, Plastics
- Price: $300~12,000. (According to different models)
Universal Grinder Youtube Video (See More)
Small V Blender Pictures:
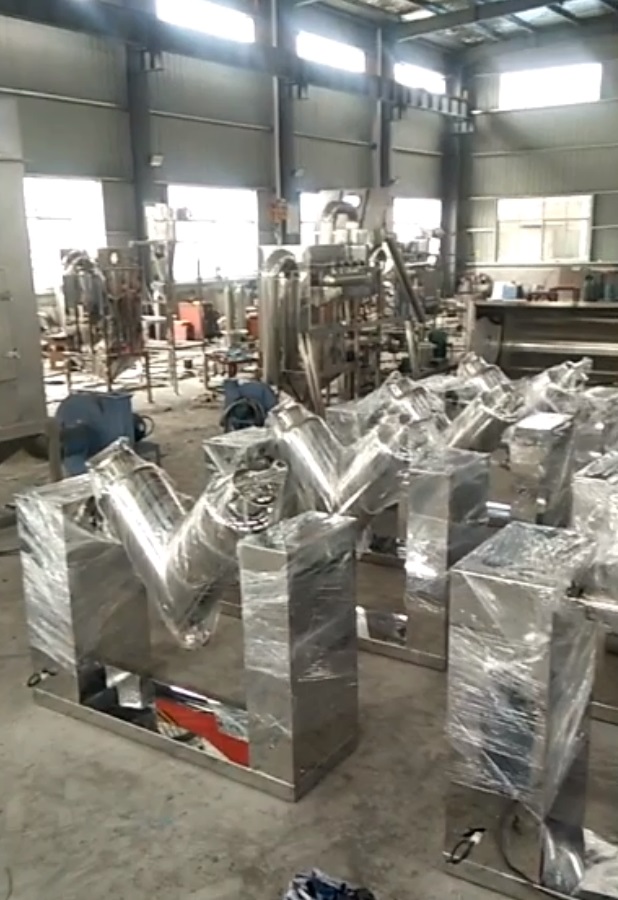
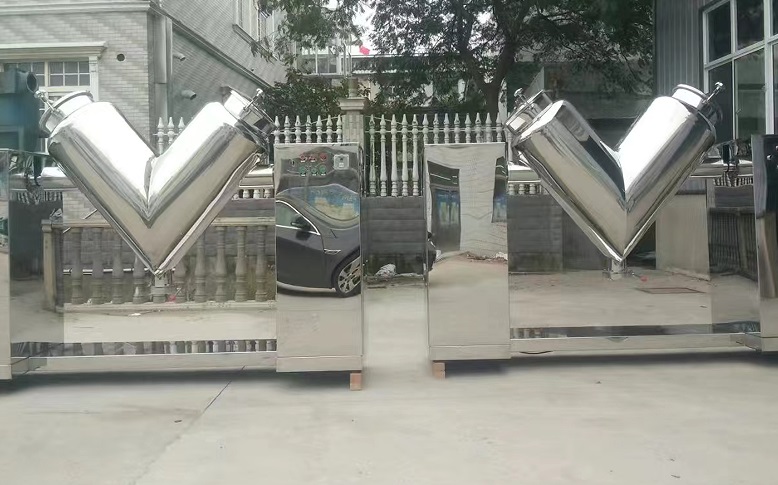
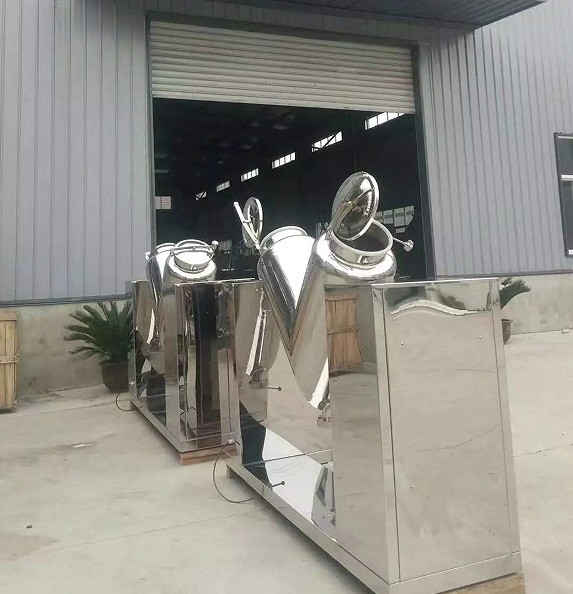
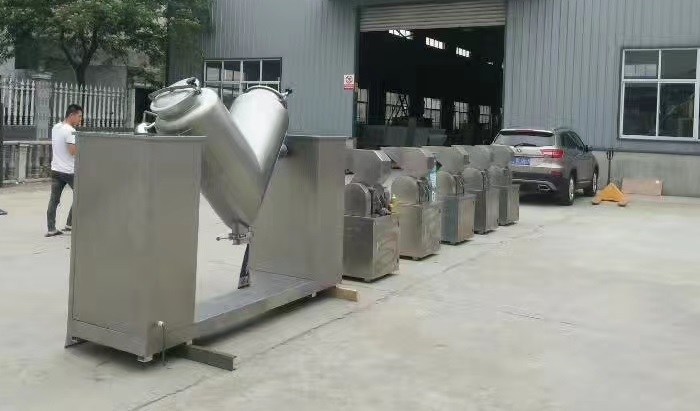
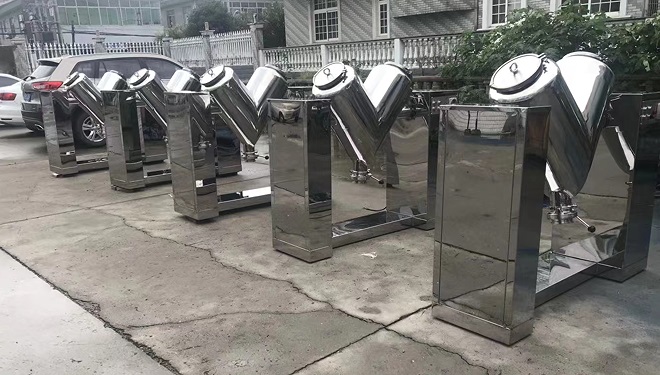
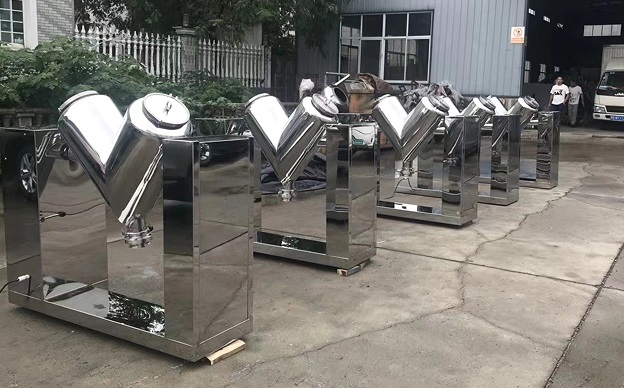
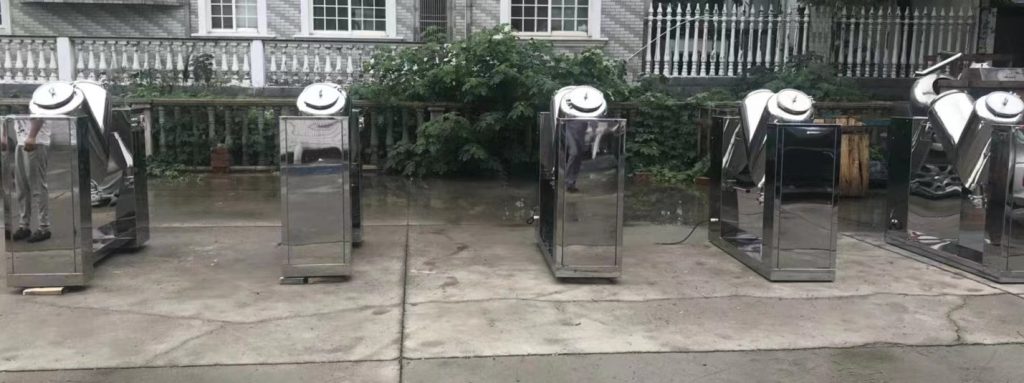
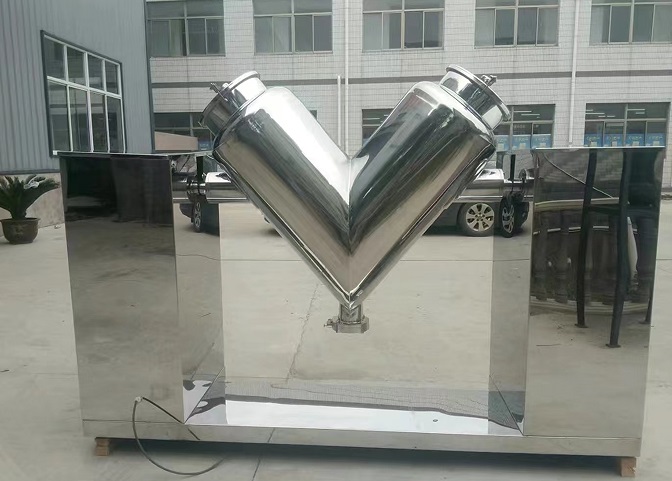
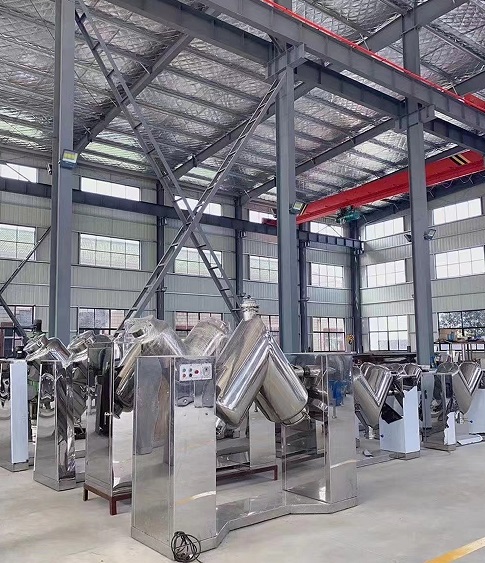
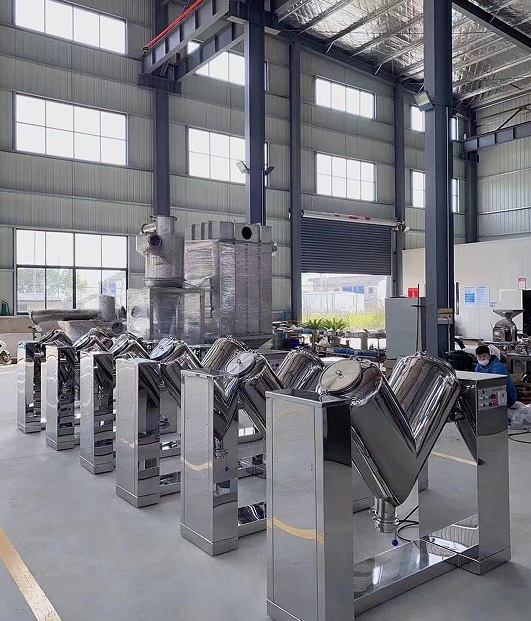
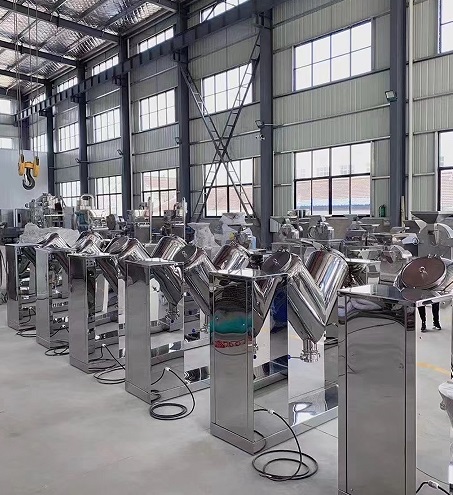
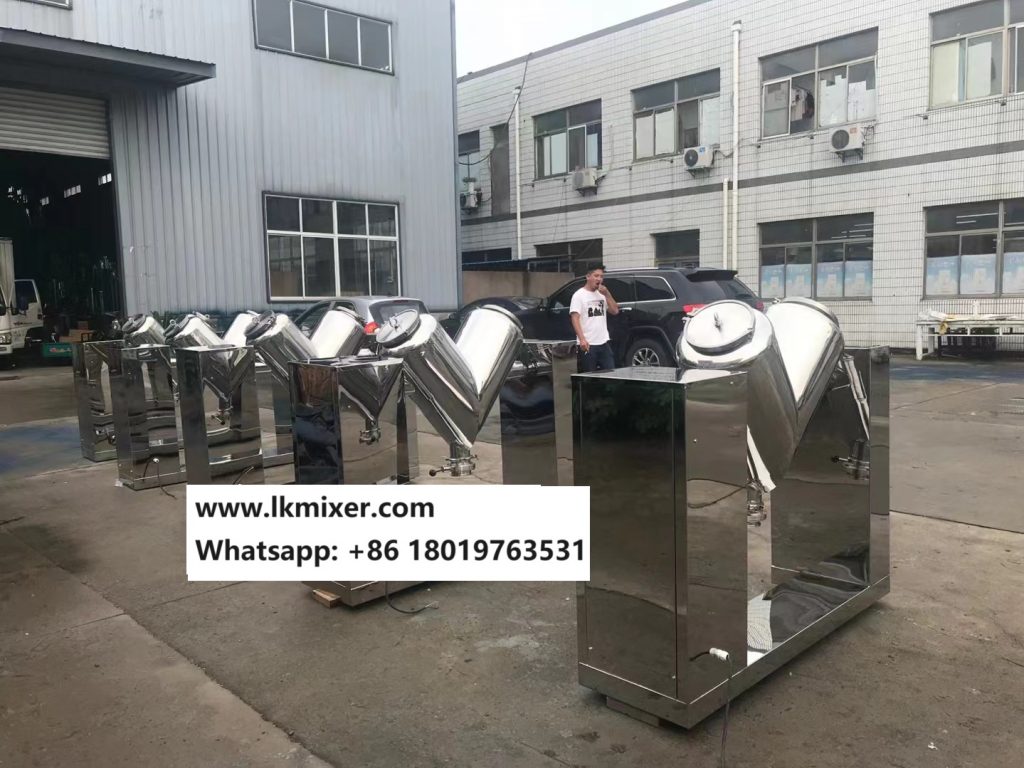
Large V Blender Pictures
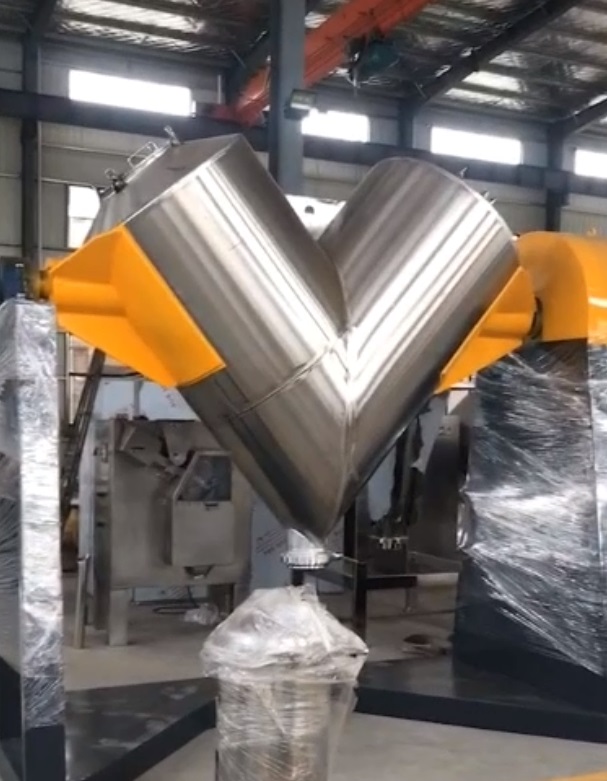
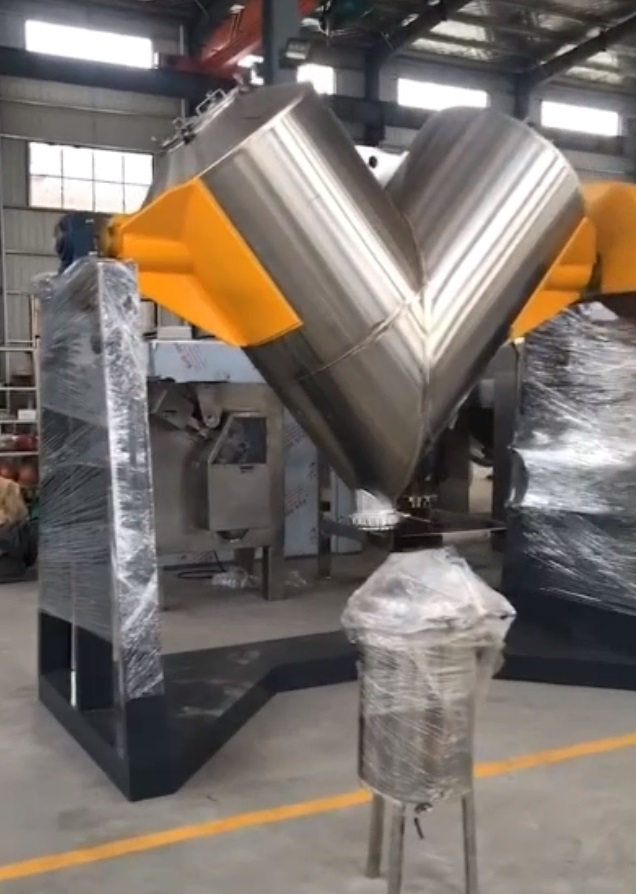
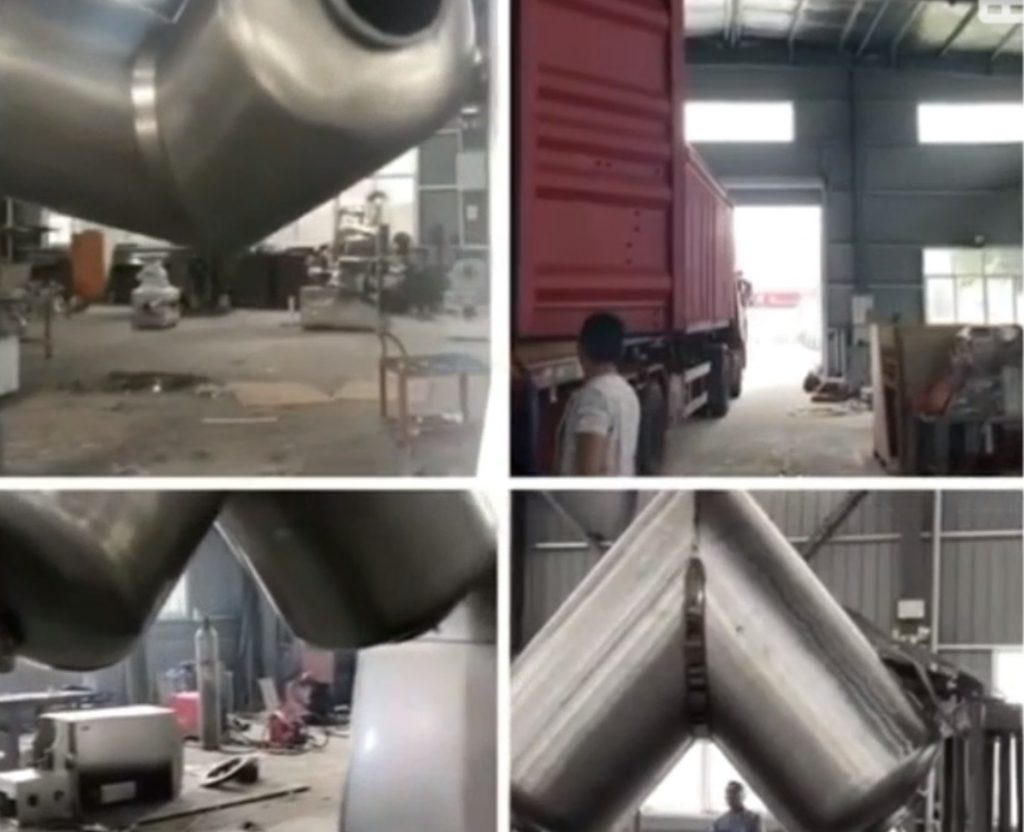
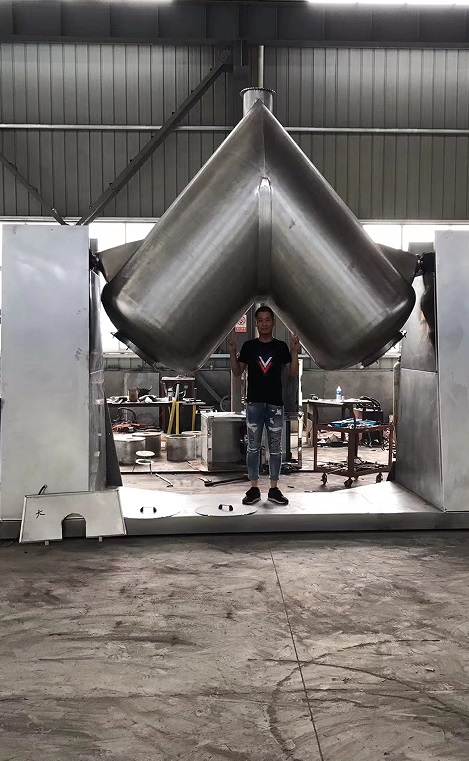
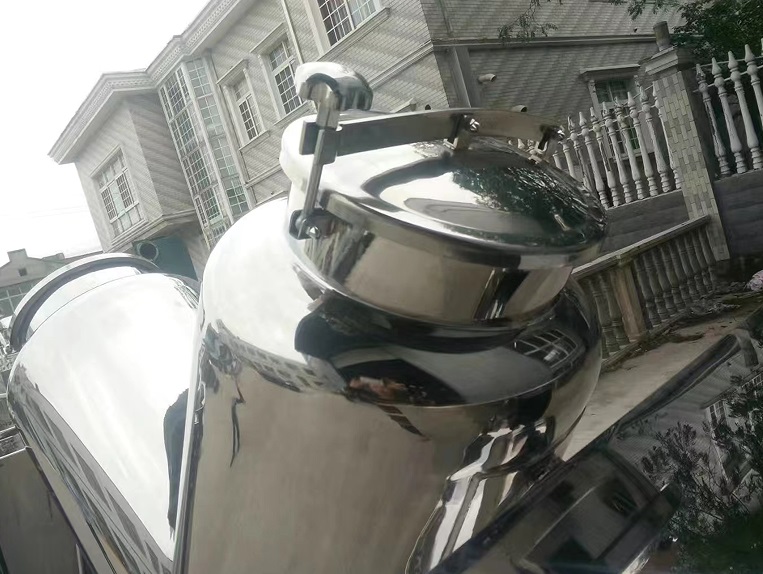
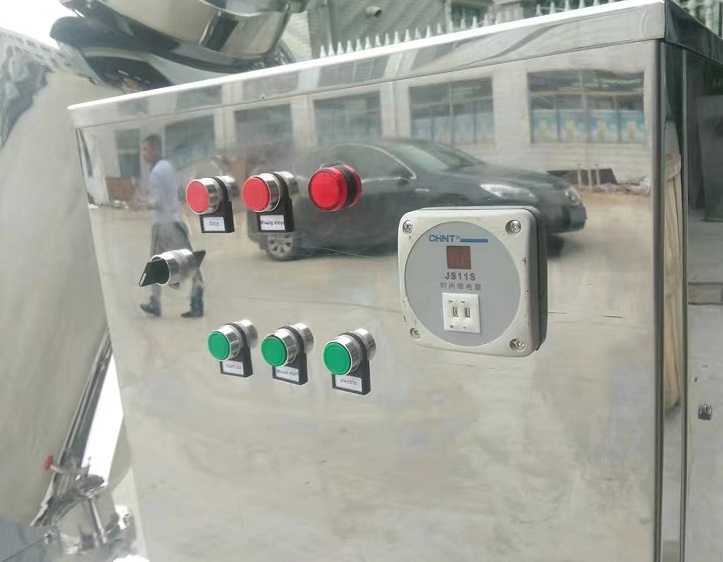
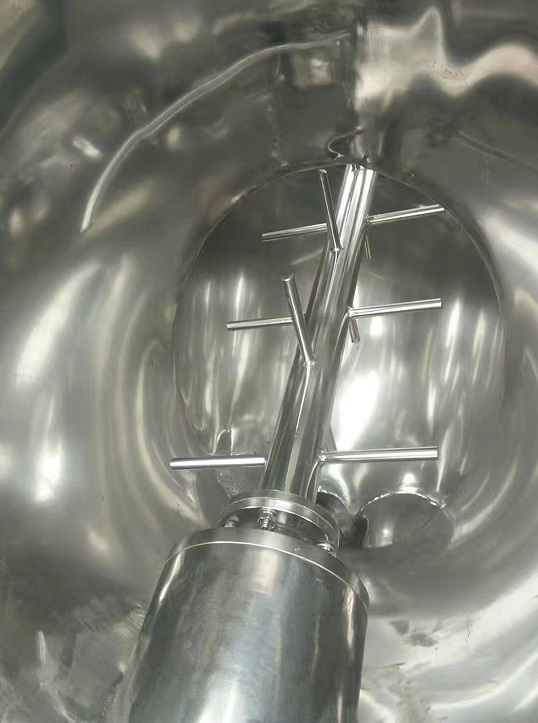
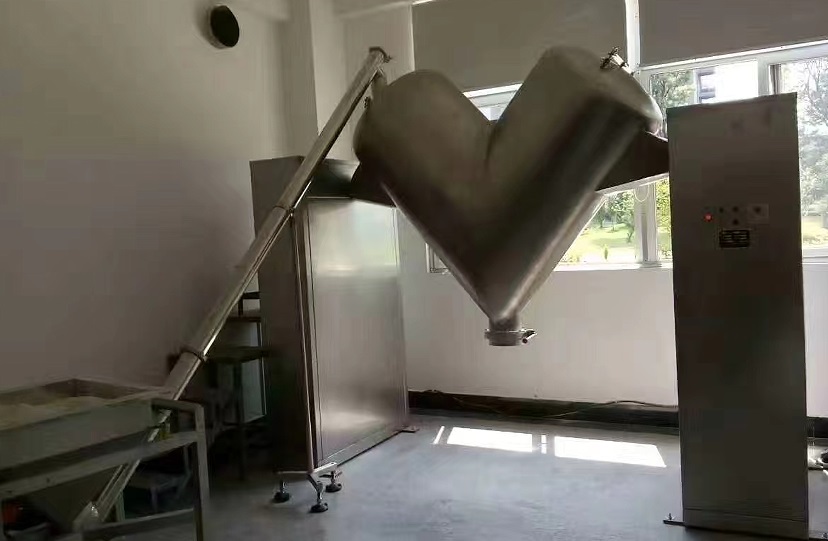
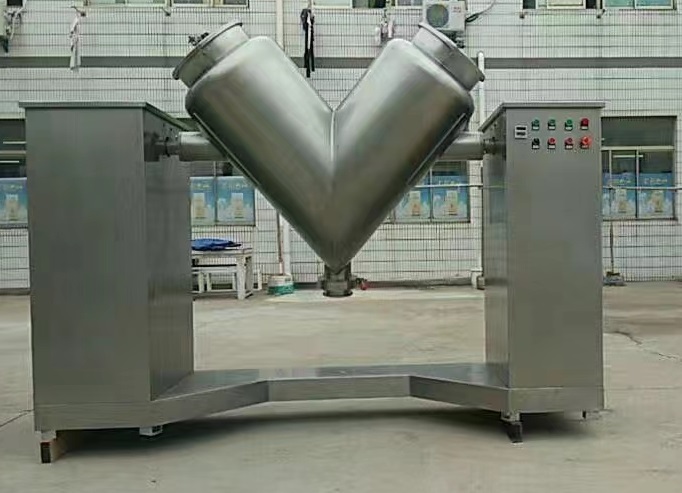
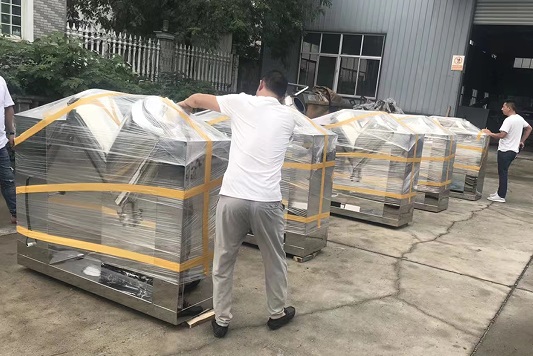
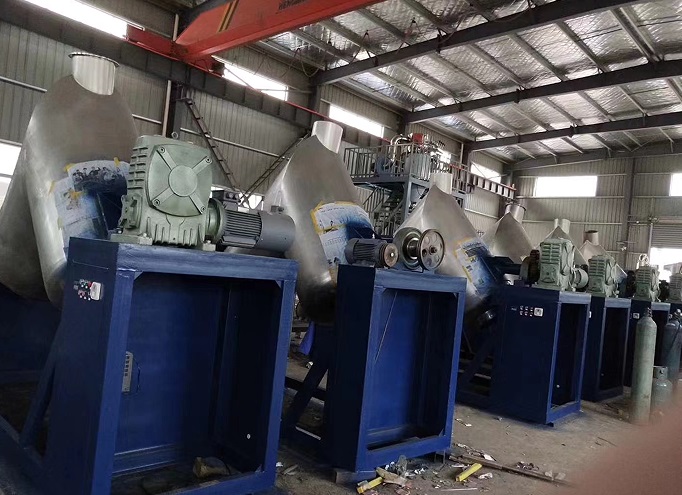
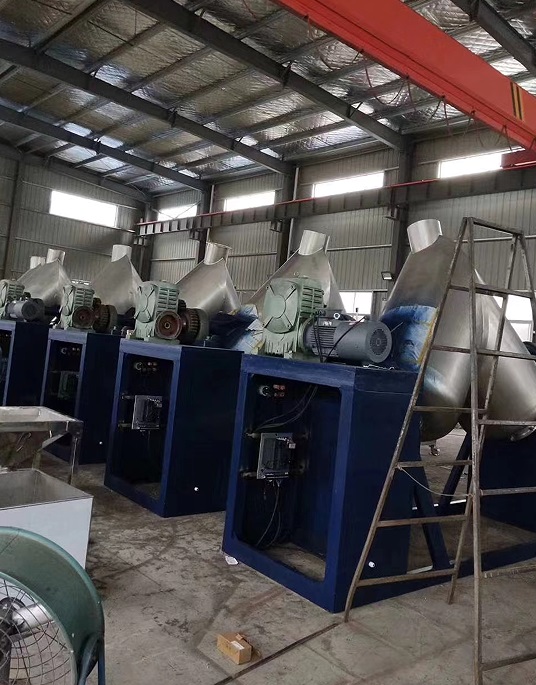
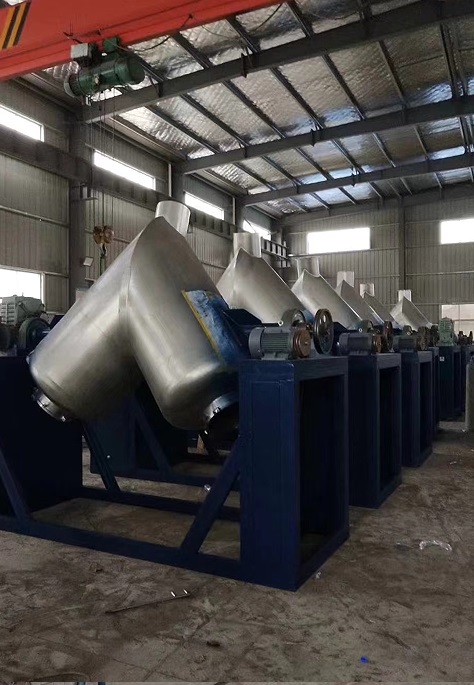
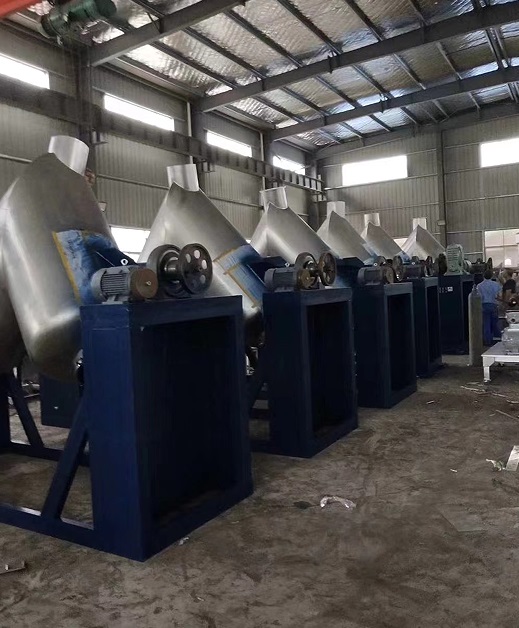
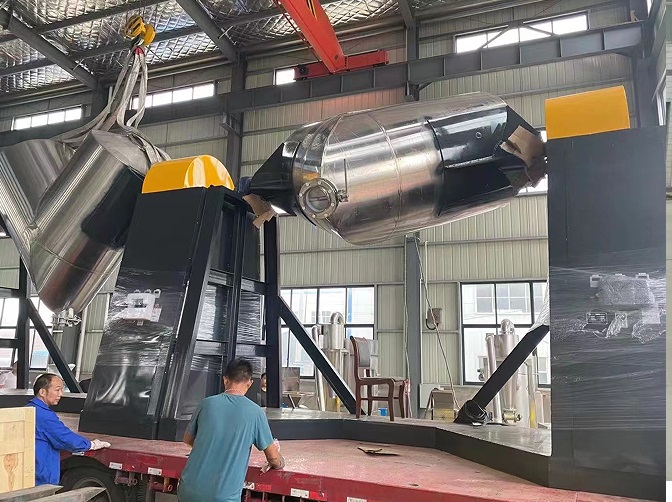
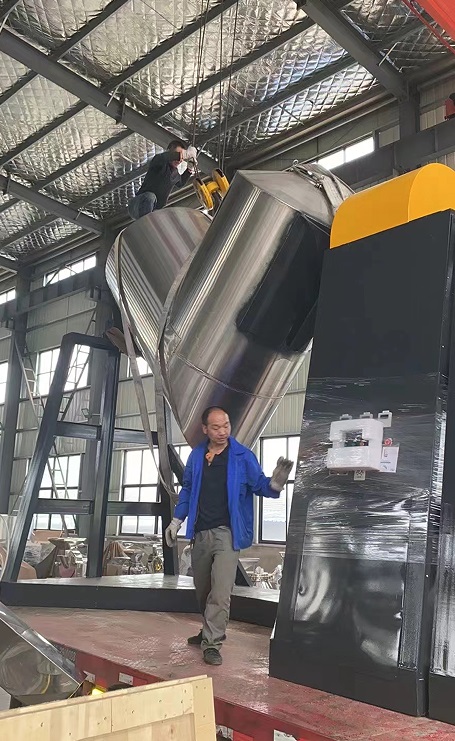
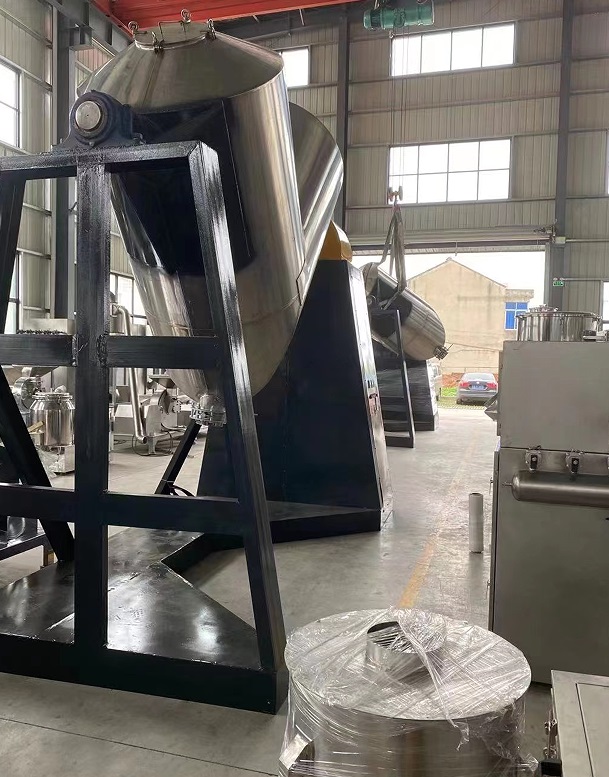
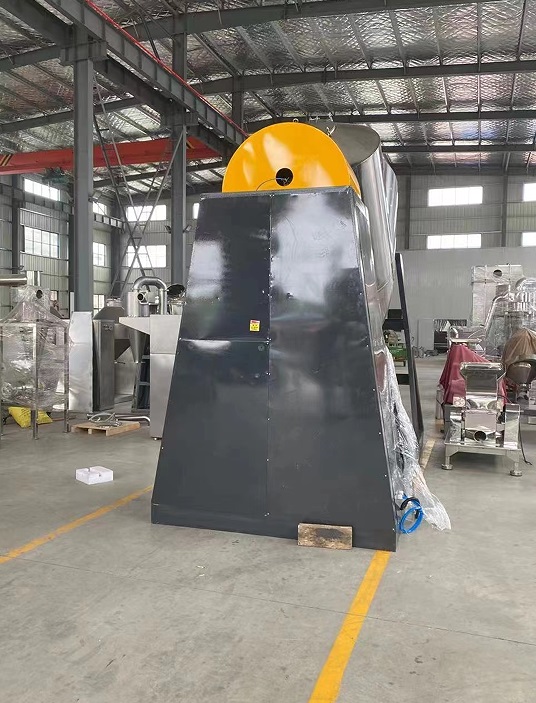
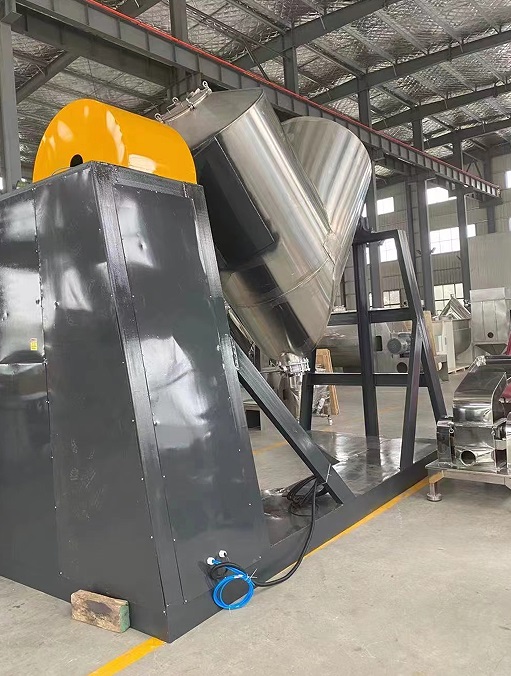
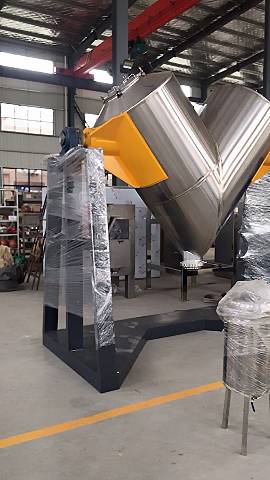
Spare Parts:
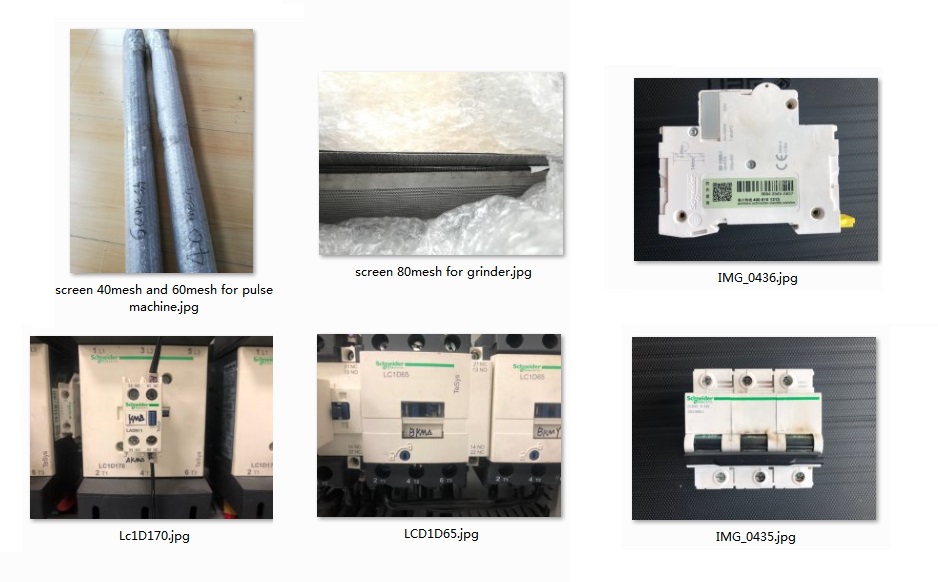
Blender Mixer for Sale:
Parameters of Pharmaceutical Mixer:
Model | Volume(㎥) | Capacity(KG/time) | Mixing Rotating Speed(rpm/min) | Feeding tine(min) | Mixing time(min) | Machine Weight(KG) | Total Power(KG) |
GHJ-0.18 | 0.18 | 72 | 12 | 3-5 | 4-8 | 280 | 1.1 |
GHJ-0.3 | 0.3 | 120 | 12 | 3-5 | 6-10 | 320 | 1.1 |
GHJ-0.5 | 0.5 | 200 | 12 | 4-6 | 6-10 | 550 | 2.2 |
GHJ-1.0 | 1 | 400 | 12 | 6-9 | 6-10 | 950 | 4 |
GHJ-1.5 | 1.5 | 600 | 12 | 6-10 | 6-10 | 1020 | 4 |
GHJ-2.0 | 2 | 800 | 12 | 8-13 | 6-10 | 1600 | 5 |
GHJ-2.5 | 2.5 | 1000 | 12 | 8-15 | 6-10 | 2040 | 7.5 |
GHJ-3.0 | 3 | 1200 | 10 | 8-12 | 8-12 | 2300 | 7.5 |
GHJ-4.0 | 4 | 1600 | 10 | 10-15 | 8-12 | 2800 | 11 |
GHJ-5.0 | 5 | 2000 | 10 | 15-20 | 8-12 | 3250 | 15 |
GHJ-6.0 | 6 | 2400 | 10 | 18-25 | 8-12 | 3850 | 18.5 |
LKMixer V Cone Blender is reliable in design and construction, use 304 stainless steel or 316 stainless steel, can meet GMP standard. We provide wholesale suitable for market, we have small v blender and large v blender. Welcome to contact us for more details.
V Blender Working Principle:
The working principle of the V-type mixer is very simple, that is, the length and size of its two cylinders are not the same, so as to achieve the effect of dumping. Let the raw material be fully stirred in its internal space, where various substances can be mixed.
Of course, the Angle and size of its two cylinders produce a variety of forces inside the mixer, including balance forces, interaction forces, etc., so that various substances such as cement and sand and stone can be fully mixed in it to produce new substances, which is also one of the reasons why it can be fully mixed.
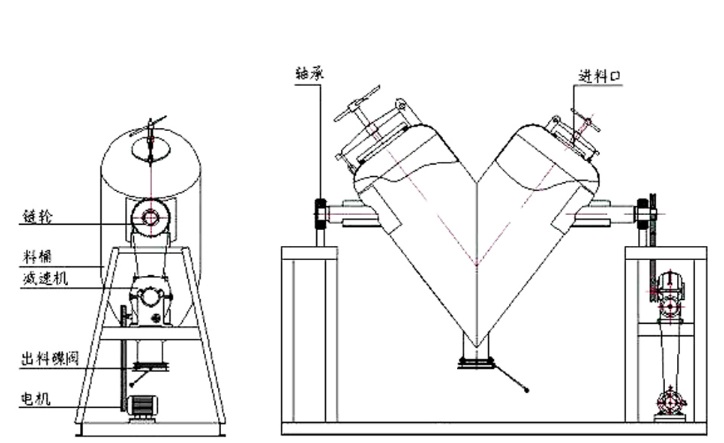
Application of V Blender:
It is suitable for food, pharmaceutical, chemical industry, such as capsule, coffee powder, Brown Sugar, Flour and so on.
What is V Blender?
V-type mixer series products are highly efficient asymmetrical mixer, which is suitable for mixing powder or pellet like materials in chemical, food, medicine, feed, ceramics, metallurgy and other industries. The machine structure is reasonable, simple, closed operation, easy access to materials, (artificial or vacuum feeding) cylinder made of stainless steel material, easy to clean, is one of the basic equipment of enterprises.
V Blender Construction:
This machine can mix dry powder and granular materials of food.
The mixing cylinder has unique structure, uniform mixing, high efficiency and no accumulation. The whole machine has simple structure and easy operation. The outer surface and material contact parts are made of high-quality stainless steel, beautiful appearance, easy maintenance and cleaning.
How to maintain V Blender machinery in use?
The use method of V-type mixer, in the case of running with material, first open the feed port of the mixer, and confirm whether the discharge port is closed, and put the specified amount of material into the V-type hopper according to the process control requirements. After feeding, in order to prevent the material from flowing out during mixing, the feeding port should be closed and locked. Next is the working time of the machine, turn on the power button, rotate the stop button to the left, start the reverse button of the mixer, adjust the motor speed within the speed specified in the process to 600r/min for mixing. After the mixing feed reaches the specified time of the process, stop by adjusting the motor speed button. When stopping, the discharge port of the mixer should be facing the ground, and the regulating motor speed button should be adjusted to 0 position. The V-type mixer will rotate the stop button to the right and cut off the power supply. Finally, the material is discharged: open the feed port of the V-type mixer, and load the material with the specified container in the feed port until the material in the hopper is discharged.
There are still many things that need our attention during the installation and use of the V-type mixer, which is conducive to the maintenance of the V-type mixer and the increase of its service life.
- installation: place the machine smoothly, install the machine foot, pad flat, so that the mechanical can run freely.
- before use, the oil must be added to the oil, and then the no-load operation, check whether the fasteners are loose, whether the electrical is normal, whether the machinery is operating normally, if there is an anomaly, repair and debugging.
- Turn the feeding port to the top, open the feeding cover for feeding, the feeding amount shall not exceed the specified volume, then close the feeding cover, start the machine to operate, if abnormal is found on the way, it must be stopped for inspection.
- the replacement of the variety must be the hopper inside and outside to wash clean. It is suitable for mixing of powder or pellet like materials in chemical, food, medicine, feed, ceramics, metallurgy, etc. The machine structure is reasonable, simple, closed operation, easy access to materials, (artificial or vacuum feeding) cylinder made of stainless steel material, easy to clean, is one of the common basic equipment.
The correct operation process of V Blender is:
- Open the feed port of the mixer, reconfirm that the feed port is closed, and put the specified amount of material into the V-shaped hopper according to the process control requirements.
- After feeding, close the feeding port and lock it to prevent the material from flowing out when mixing.
- start the V-type mixer forward button, adjust the motor speed, slow forward running.
- During the operation of the V-type mixer, the fuselage should be operated at a constant speed without abnormal noise.
- mixing to reach the specified time, by adjusting the motor speed button to stop, stop should make the mixer discharge port is facing the ground, and adjust the motor speed button to 0, V-type mixer will stop button to the right rotation, cut off the power supply.
- The fault problem of V Blender is:
- 1, V-type mixer host vibration and noise abnormal sound, installation is not adjusted and speed change machine damage.
- 2, V-type mixer in the use of the process, sudden shutdown and discharge mechanism if not normal operation.
- 3, V-type mixer can not start, mainly because the power supply is not connected, lack of phase, check the line.
- Insufficient motor power, improper preparation of belt pulley, belt slip, serious wear of hammer, uneven feeding or excessive water content of raw materials are the main reasons for low production efficiency
- 5, bearing overheating when the bearing lubrication is poor, damaged or spindle bending, rotor serious imbalance, belt is too tight will make the bearing overheating. By adding and replacing lubricating oil, replacing bearing and spindle, balancing rotor, adjusting belt tightness and other methods, the bearing can be restored to normal state. The dry and wet materials of the three-dimensional mixer can be mixed by the trough mixer. CH series trough mixer is used for mixing powder or wet material, so that the main auxiliary materials are evenly mixed in different proportions. Widely used in pharmaceutical, food, chemical, electronic and other industries of dry powder mixing. The trough mixer is made of stainless steel in contact with the material. The clearance between pulp blade and barrel body is small. Both ends of the mixing shaft are provided with a sealing device to prevent material leakage. Hopper adopts button control, easy discharge. Especially suitable for three-dimensional mixer is a widely used in pharmaceutical, chemical, food, light industry and other industries and scientific research units of novel material mixer, the machine can be very uniform mixing flow performance of good powder or granular materials, so that the mixed material to achieve the effect, the existence of centrifugal force in the mixing movement, it can make different density of mixed materials produce segregation. The heat source of the three-dimensional mixer is mainly self-friction, so in most cases no additional heating is required. The V-type mixer is composed of a container welded by two cylinders and a reinforced mixing element, which has a single V type and a multi-V type series. When the container rotates, the material to be mixed is divided into two flows when the top Angle of the cylinder turns upward, and then the top Angle turns downward, and the material flows into the top Angle again, so it is repeatedly divided and combined to achieve mixing.
Business Type: | Manufacturer/Factory | Main Products: | Mill, grinder, granulator, mixer, Crushing Equipment |
Number of Employees: | 100 | Year of Establishment: | 2014.05 |
Production Capacity | 5000Set/Year | After-sales Service: | Technical Support; on-line teach lessons |
R&D Capacity: | ODM, OEM | Annual Output Value: | US$5 Million – US$10 Million |
No. of R&D Staff: | 5 | No. of Production Lines: | 6 |
LK Mixer is a professional manufacturer for grinder, mixer and pulverizer. These machines are widely used in pharmaceutical, cosmetic, health care products and chemical industries. Our main product including granulating machine, grinder, mixer, dryer, etc. All mechanical products in accordance with the China GMP design requirements. And also we have other certifications such as CE, UL for motors.
Business Philosophy
“Quality is the main policy of sales” and “integrity is the principle of success” are the business philosophy of our people. We carry out one-year warranty, lifelong maintenance service, with technical consultation, with material test machine and other services, and long-term supply of equipment. Welcome new and old customers to negotiate cooperation!
Certifications:
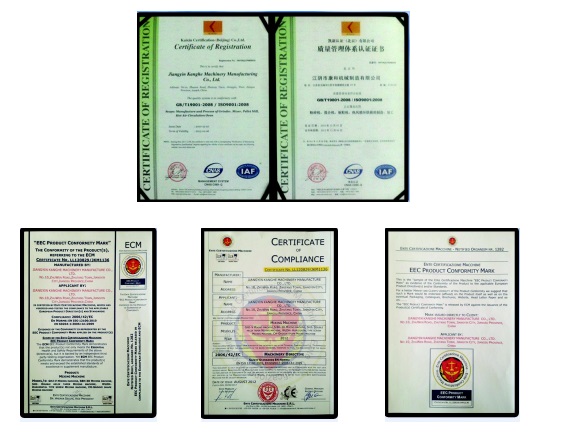
Small Machine Packing:
Small machine packed with export fumigation-free wooden cases, goes with bulk shipment or in container.
When packing small machines for sea shipment, it is important to take measures to ensure that the machines are protected from damage during transit. Here are some general steps that a manufacturer may follow when packing small machines for sea shipment:
- Clean and dry the machine: Before packing, the machine should be thoroughly cleaned and dried to prevent any moisture or debris from causing damage during transit.
- Disassemble the machine: If possible, the machine should be disassembled into its component parts to reduce its overall size and make it easier to pack.
- Wrap the machine in protective material: The machine should be wrapped in a layer of protective material, such as bubble wrap or foam, to protect it from scratches and impact during transit.
- Place the machine in a sturdy box: The wrapped machine should then be placed in a sturdy box that is appropriate for the size and weight of the machine. The box should be made of durable material, such as corrugated cardboard or plywood, and should be able to withstand the rigors of sea transit.
- Add packing material: The box should be filled with packing material, such as packing peanuts or air pillows, to provide cushioning and prevent the machine from shifting during transit.
- Seal the box: The box should be securely sealed with high-quality packing tape to prevent it from opening during transit.
- Label the box: The box should be clearly labeled with the machine’s name, weight, and any other relevant information, as well as the destination address and contact information.
Overall, the goal is to pack the small machine in a way that will protect it from damage during transit and ensure that it arrives at its destination in good condition. It is important to follow proper packing procedures and use high-quality packing materials to minimize the risk of damage during sea shipment.
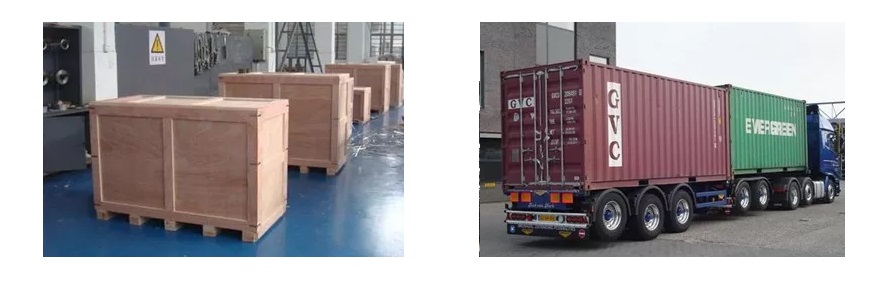
Large Machine Packing:
Packing a large machine for sea shipment can be a complex and challenging task. However, with careful planning and attention to detail, it is possible to pack a large machine for sea shipment in a way that will ensure that it arrives at its destination in good condition. Here are some general steps that a manufacturer may follow when packing up a large machine for sea shipment:
- Clean and prepare the machine: Before packing, the machine should be thoroughly cleaned and prepared. All fluids, such as oil or coolant, should be drained, and any loose or detachable parts should be removed.
- Disassemble the machine: If possible, the machine should be disassembled into its component parts to reduce its overall size and make it easier to pack. Each part should be carefully labeled and numbered to ensure that it can be easily reassembled at the destination.
- Protect delicate parts: Delicate or fragile parts should be wrapped in protective material, such as bubble wrap or foam, to protect them from damage during transit.
- Build a custom crate: A custom crate should be built around the machine to provide a secure and sturdy enclosure. The crate should be made of durable material, such as plywood, and should be designed to fit the machine snugly. The crate should also include braces or supports to prevent the machine from shifting during transit.
- Add cushioning material: The crate should be filled with cushioning material, such as packing peanuts or air pillows, to provide extra protection and prevent the machine from moving or shifting during transit.
- Securely fasten the machine: The machine should be securely fastened to the crate to prevent it from moving or shifting during transit. This may involve using straps, bolts, or other fasteners to hold the machine in place.
- Seal and label the crate: The crate should be securely sealed with high-quality packing tape, and should be clearly labeled with the machine’s name, weight, and any other relevant information. The destination address and contact information should also be clearly marked on the crate.
Overall, packing a large machine for sea shipment requires careful planning and attention to detail. It is important to use high-quality materials and follow proper packing procedures to ensure that the machine arrives at its destination in good condition. A professional packing and shipping company may be consulted to ensure that the machine is properly packed and prepared for sea shipment.
Shipment:
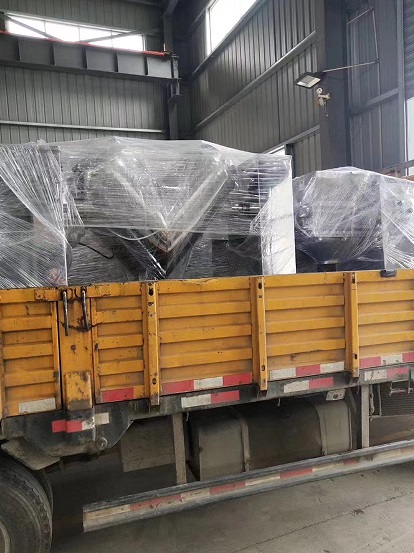
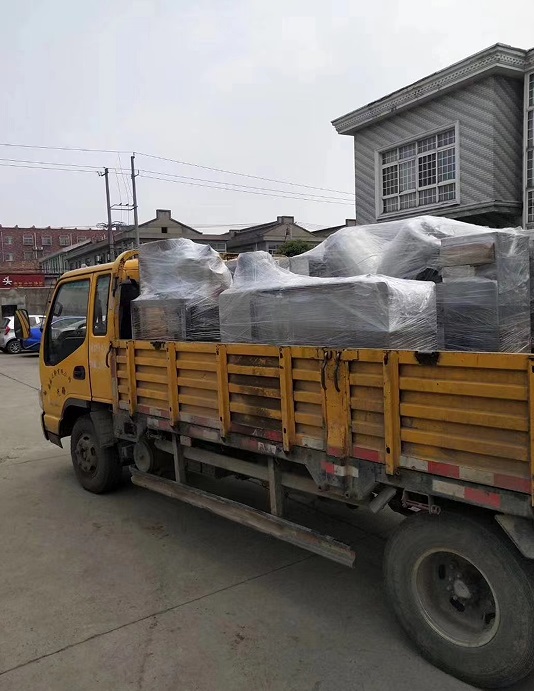
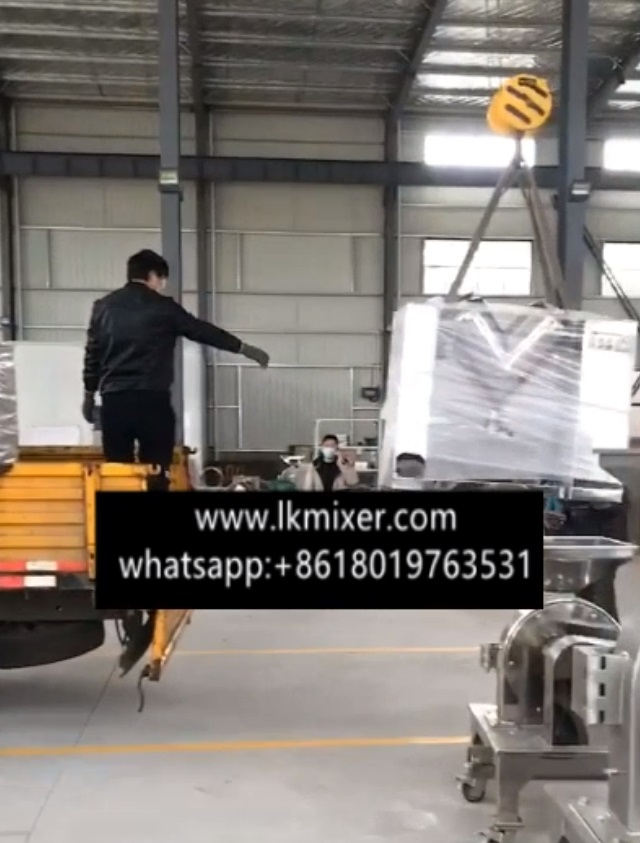
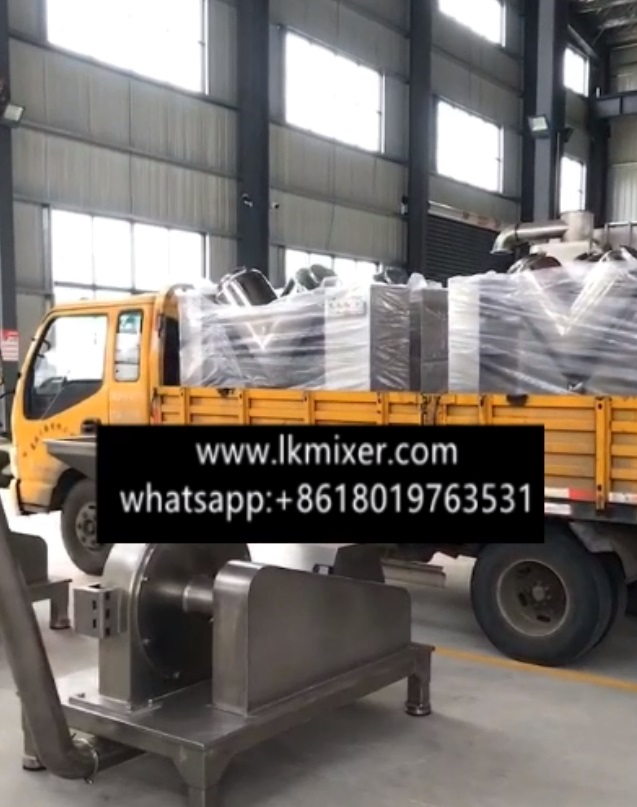
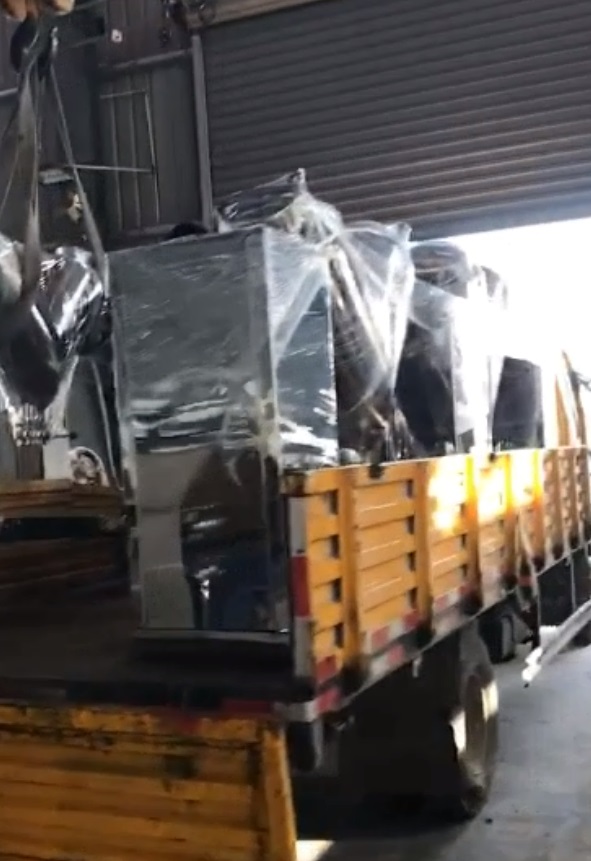
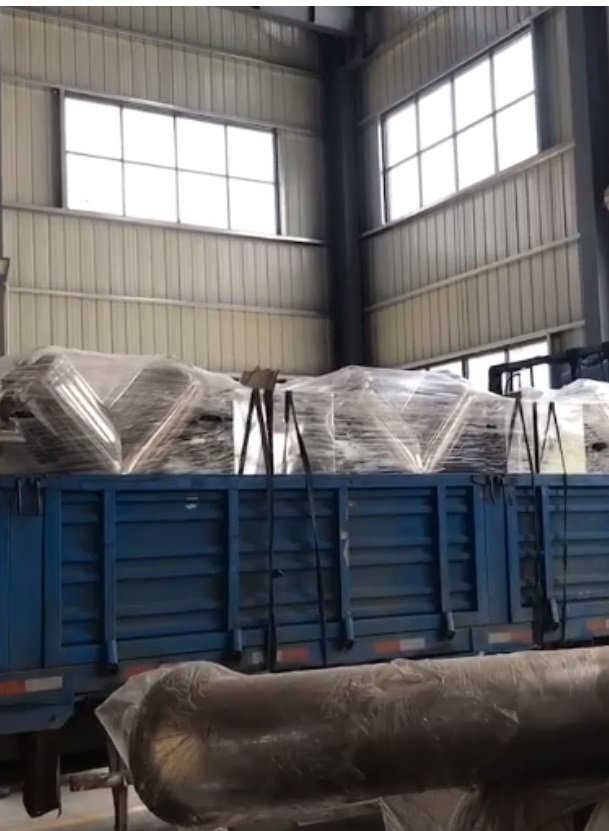
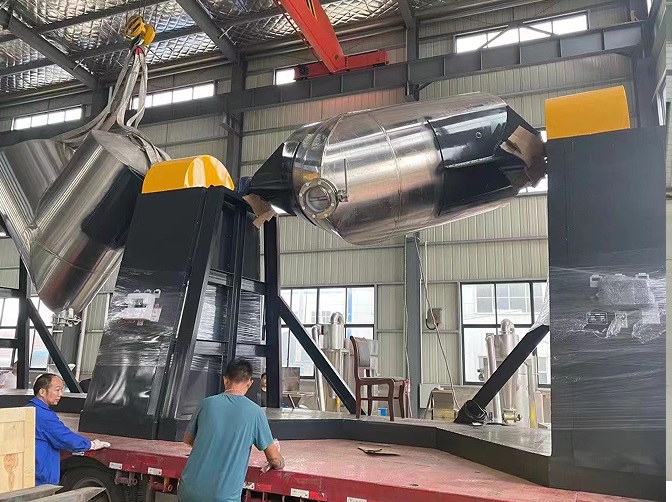
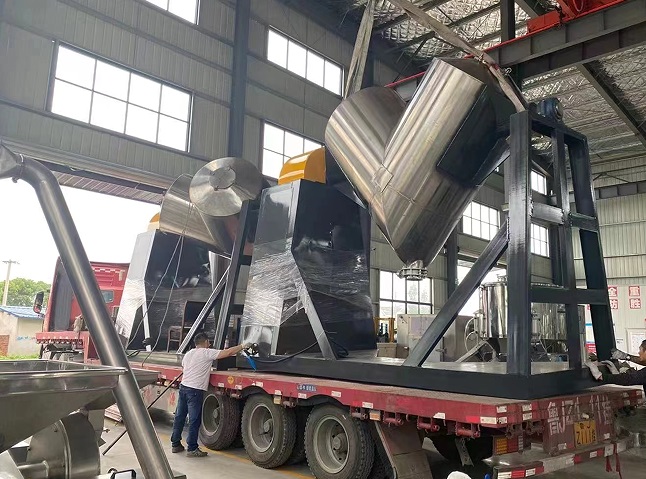
Customer Side Machine Groups Showcase Videos:
Dust Collector Shipment
Shipment – Packing Method
Two Large Industrial Grinder Ready to Ship
Domestic Shipment Show Case:
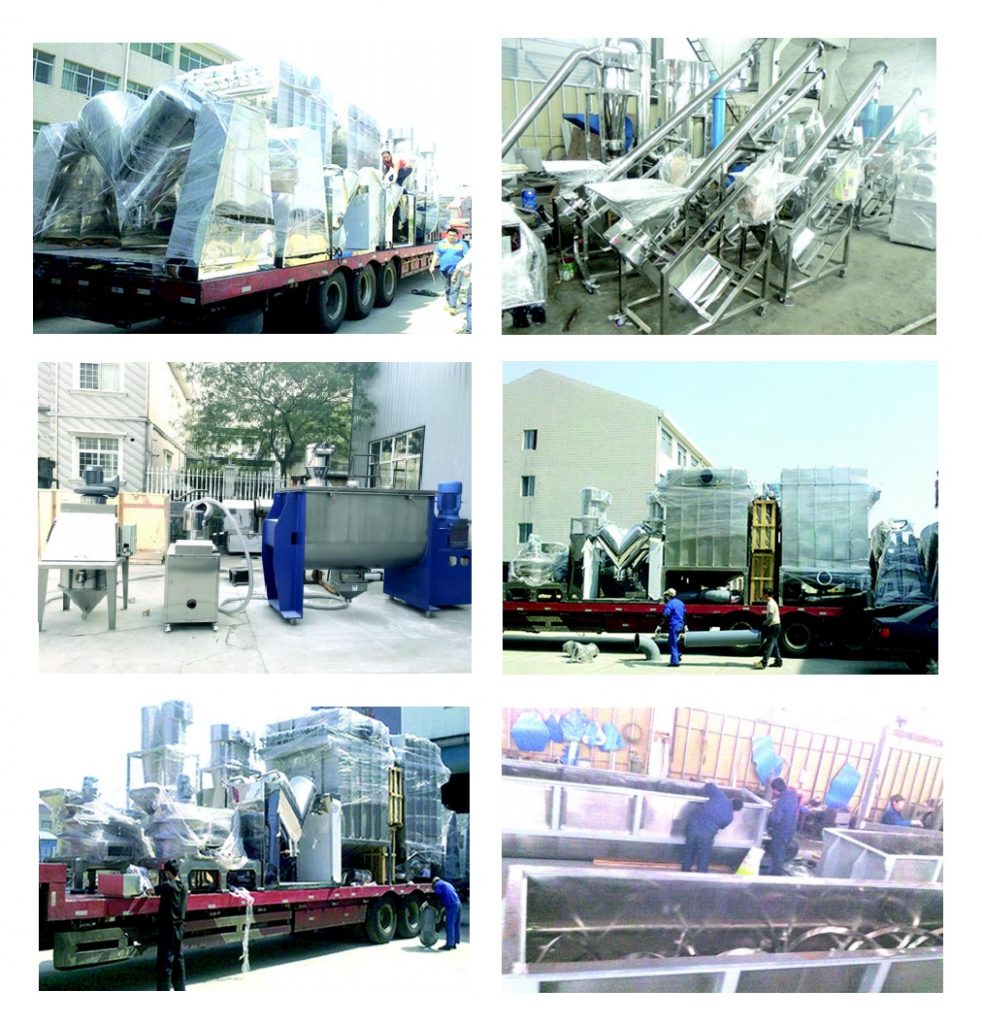
Installation Layout:
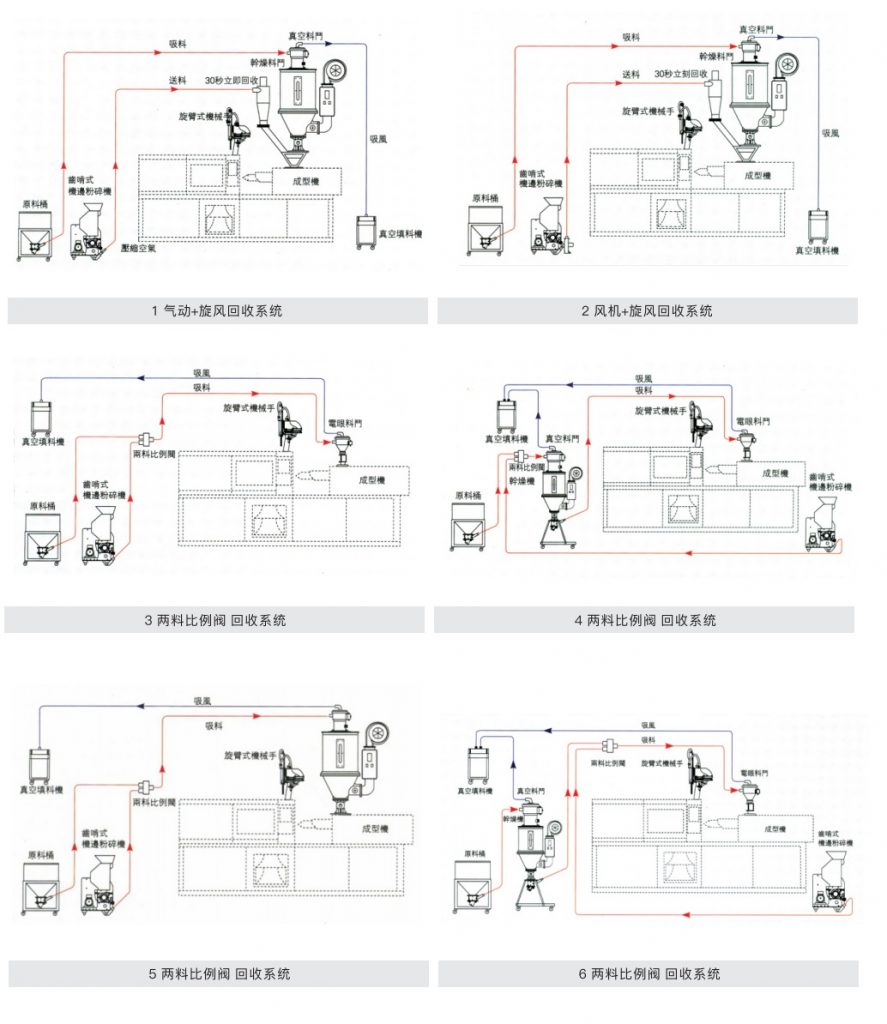
Maintenance and Safety Measures
Proper maintenance practices for the machine
Proper maintenance practices are essential for ensuring the efficient and safe operation of a universal grinder. Here are some maintenance practices that should be followed:
- Regular cleaning – The machine should be cleaned regularly to remove any debris, dust, or coolant that may accumulate on the machine’s surfaces. This can be done using a soft brush, air hose, or a cleaning solution.
- Lubrication – The machine’s moving parts should be lubricated regularly to reduce friction and wear. The manufacturer’s recommendations for lubrication intervals and types should be followed.
- Inspection – The machine should be inspected regularly for any signs of wear, damage, or misalignment. Any issues should be addressed immediately to prevent further damage or safety hazards.
- Replacement of worn or damaged parts – Worn or damaged parts should be replaced immediately with genuine parts from the manufacturer.
- Calibration – The machine should be calibrated regularly to ensure that it is operating within the specified tolerances and accuracy.
- Operator training – Proper operator training is essential for ensuring the safe and efficient operation of the machine. Operators should be trained on the proper operation, maintenance, and safety procedures for the machine.
- Record keeping – A maintenance log should be kept to track the machine’s maintenance history, including cleaning, lubrication, inspection, and repairs. This can help identify any trends or issues that need to be addressed.
Following these maintenance practices can help ensure the safe and efficient operation of a universal grinder, prolong its lifespan, and reduce the risk of downtime and costly repairs.
Safety measures for operators and workers
Safety measures for operators and workers are crucial when using a universal grinder. Here are some safety measures that should be followed:
- Personal protective equipment (PPE) – Operators and workers should wear appropriate PPE, including safety glasses, hearing protection, gloves, and safety shoes.
- Machine guards – The machine should be equipped with proper machine guards to prevent access to the grinding wheel during operation. The guards should be in good condition and properly installed.
- Lockout/tagout procedures – Lockout/tagout procedures should be followed to ensure that the machine is not accidentally started or energized during maintenance or repair.
- Training – Operators and workers should receive proper training on the safe operation of the machine, including the use of PPE, machine guards, and lockout/tagout procedures.
- Inspection – The machine should be inspected regularly for any signs of wear, damage, or misalignment that may pose a safety hazard.
- Proper use of grinding wheels – Operators should ensure that the grinding wheel is properly installed, dressed, and aligned. The grinding wheel should not be overloaded or forced into the material being ground.
- Proper handling of coolant – If coolant is used, operators should ensure that it is properly mixed, applied, and contained. Coolant should not be allowed to accumulate on the floor, as it can create a slipping hazard.
- Emergency procedures – Emergency procedures should be established and communicated to all operators and workers in case of an accident or injury.
Following these safety measures can help prevent accidents and injuries when using a universal grinder. It is important to prioritize safety and ensure that all operators and workers are trained and informed about the potential hazards of the machine.
You may also interest in:
About LKMixer
LKMixer is a professional manufacturer for fertilizer production line, grinder, mixer and granulator, shredder. These machines are widely used in food, pharmaceutical, cosmetic, health care products and chemical industries. The Food materials like Peanut, mushroom, seeds, potato, bean, tobacco, salt, cannabis, tea, Sugar, corn, Coffee, rice, pepper, grain as so on. Grinders have many types such as Pulse Dust Grinder which suitable for zero pollution environment, Turbine Mill which is suitable for coffee bean, 12-120mesh all can meet, Ultrafine Grinding Mill covers 80-200mesh, and also Winnowing Dust Grinder or other grinding machines like SF Hammer. Welcome to contact us for details. Contact us for more information. Proposal, catalog, quotation. Mobile/WhatsApp: +86 18019763531 Tel: +86 21 66037855 Email: sales@lkmixer.com