Ribbon Blender Advantages and Disadvantages
Today we discuss about Ribbon Blender Advantages and Disadvantages. Ribbon mixers are widely used to blend thousands of products in various industries around the world. These are mainly used in everything from fertilizers to food processing and from plastics to cosmetics. Ribbon mixers are one of the most popular and effective mixing equipment available today. Versatility and cost effectiveness have made this blender popular. It is made with a simple design that ensures easy maintenance at a low cost. For the enterprises that choose to use it, it reduces the production cost, improves the overall economic benefits, and is very beneficial to the long-term production and production of enterprises. Its function is to mix materials with different components to achieve a uniform mixing effect.

Working principle of Ribbon Blender:
The ribbon mixer is mainly composed of a rotating helix and a fixed cylinder. When the material in the cylinder enters the machine, the spiral begins to rotate, pushing the material to the outlet of the cylinder and mixing it evenly along the way. The rotation speed of the screw and the feed speed of the material can be adjusted to control the degree and time of mixing.
Advantages of Ribbon Blender:
Compared with other equipment Ribbon mixers have the following advantages compared with other common mixing equipment:
- Protect motor and equipment to prevent overload. When the load is too large and blocked, the working liquid is ejected from the fusible plug to make the working machine and the load free, so that the motor and equipment are not damaged when starting and overloading. The speed difference caused by impact during operation is mitigated by couplings.
The smooth start of the load equipment, in the equipment starting and running process, effectively isolated the impact and torsional vibration of the equipment. - Better mixing effect: Compared with traditional mixers, the screw design of the ribbon mixer allows the material to be mixed more evenly. Due to the push effect of the screw, the material can fully contact and collide during the mixing process, so as to achieve a better mixing effect.
- Energy savings: Ribbon mixers have lower energy consumption compared to high speed mixing equipment.
- Small footprint: ribbon mixers require less space than other mixing equipment and are more flexible for companies with limited space.
- Simple operation: The use of screw belt mixer is very convenient, just put the material into the machine, set the mixing time and speed.
- Strong adaptability: The ribbon mixer is suitable for mixing all kinds of powder, granular and certain viscous materials.
- Easy to clean: The structure of the ribbon mixer is relatively simple, and it is easy to clean.
- Widely use: Ribbon mixer is widely used in food, chemical, metallurgy, building materials and other industries, its main applications include: – Food processing: ribbon mixer can be used to mix flour, condiments, food additives and other food raw materials. – Chemical field: Ribbon mixer can be used to mix powdered or granular chemical raw materials for pharmaceutical, pesticide and other industries. – Building materials field: Screw belt mixer can be used to mix cement, lime, stone powder and other building materials.
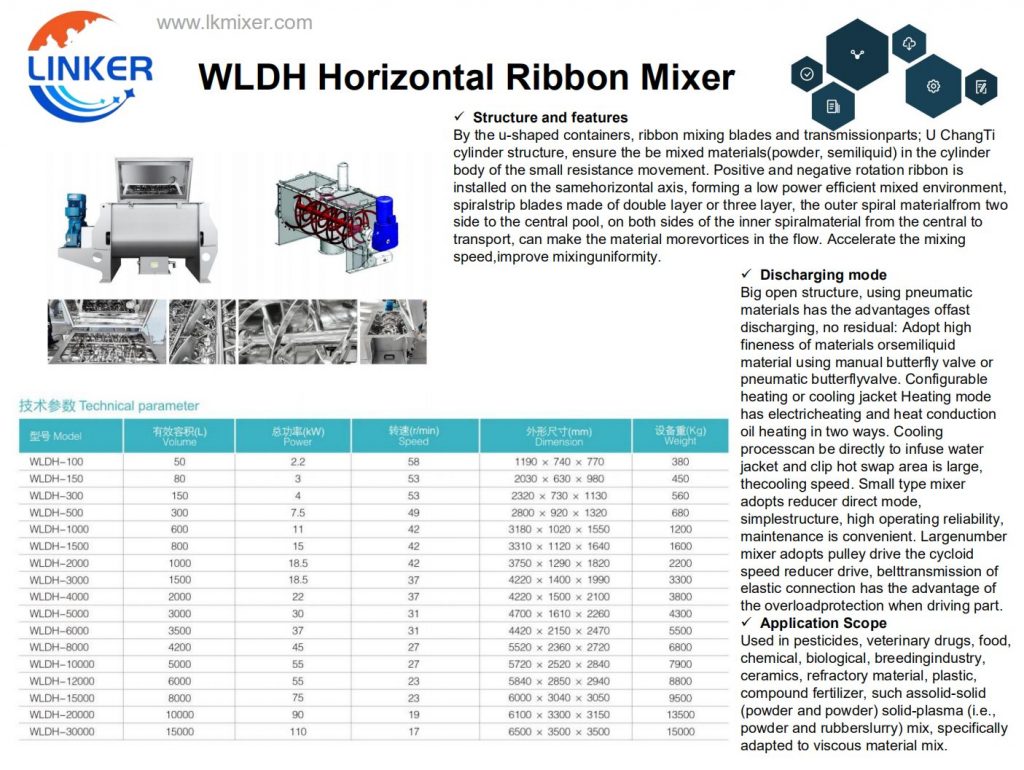
Disadvantages of Ribbon Blender:
- The hydraulic coupling is usually not loaded with the inverter, can not effectively adjust the speed of the equipment.
- Because the loading of the hydraulic coupling is also easy to form multiple transmission of kinetic energy, resulting in power consumption, solid can not improve the starting performance of the equipment.
- The device cannot be clicked during use. In the overload, the splash of the working liquid also causes danger to the personal safety of the operator.
Advantages of double Ribbon Blender:
- High mixing efficiency: The double screw belt mixer uses the opposite rotating double screw belt for mixing, which has the characteristics of high mixing intensity and high mixing efficiency, and can effectively ensure the uniformity of mixing. The screw belt mixer uses spiral blades to stir the material, so that the material can get better mixing effect in the mixing process. It can roll and mix the material in a full range, so that the mixing effect of the material is more uniform and adequate. This good mixing effect can not only improve the quality of materials, but also meet different process requirements.
- Wide range of application: The double screw belt mixer is suitable for mixing all kinds of powder, particles and flake materials, and it also has good adaptability for materials with large viscosity, poor density and significant ratio. The application range of the ribbon mixer is very wide. It can be used for the mixing of powder, particles, liquid and other materials, and can also be used for the mixing of materials with different gravity and different particle size. In addition, the ribbon mixer can also be customized according to different process requirements to meet the needs of different fields.
- Simple operation: double screw belt mixer is simple in structure, easy to clean, easy to operate, and easy to maintain and maintain.
- With premixing function: due to the high mixing strength of the double screw belt mixer, the premixing operation can also be performed before mixing, so that various materials can be more fully mixed together and improve the mixing effect.
- Another advantage of the ribbon mixer is that the mixing speed is fast. Because the screw belt mixer uses spiral blades for mixing, it can complete the mixing of materials in a relatively short time. This can not only improve work efficiency, but also reduce the retention time of the material, thereby reducing the risk of material deterioration.
- The screw belt mixer has simple structure and fewer parts, so its cleaning and maintenance is very convenient. In the process of use, the equipment can be easily disassembled and cleaned, so as to ensure the cleanliness of the equipment. In addition, the maintenance cost of the ribbon mixer is also very low, its parts replacement cycle is long, and the service life is long.
- Safe and reliable: The screw belt mixer is designed with safety factors fully considered. Its equipment operates stably and does not produce violent vibration and noise. In addition, the screw belt mixer is also equipped with safety facilities such as emergency shutdown, thus ensuring the safety of the operator.
In short, the ribbon mixer is an efficient, reliable and practical mixing equipment. It has the advantages of good mixing effect, fast mixing speed and wide application range. In addition, the ribbon mixer also has the characteristics of easy cleaning and maintenance, safety and reliability. These features make ribbon mixers ideal for many industries.
The shortcomings of double Ribbon Blender:
- High energy consumption: the mixing efficiency of the double screw belt mixer is high, but a certain amount of energy is consumed during use, so its energy consumption is high.
- Large equipment investment: the structure of the double screw belt mixer is relatively complex, which needs to be designed and manufactured, and the machine volume is relatively large, so the equipment investment is relatively high.
- Some materials are prone to bias: because the mixing strength of the double screw belt mixer is larger, when the density and specific gravity of some materials are larger, it is easy to produce bias, which affects the mixing efficiency.
- Large noise: in the mixing process, the double screw belt mixing will produce a large noise, if the mixer and the surrounding environment are not appropriate, it may cause adverse effects on personnel.
In summary, the double screw belt mixer has many advantages in mixing efficiency, application scope, simple operation, etc., but it also has disadvantages such as high energy consumption, large equipment investment, and easy deviation of some materials. In the selection of double screw belt mixer need to be considered according to the specific production demand and economic cost, in order to achieve the best mixing effect.
Horizontal ribbon mixer for pesticide powder
Pesticide powder horizontal ribbon mixer, pesticide powder mixer, herbicide powder mixer, pesticide powder mixing mixer, ribbon mixer, horizontal ribbon mixer, double screw horizontal mixer, horizontal powder mixer, pesticide powder dispensing mixing equipment, ribbon mixer, ribbon mixing equipment, horizontal ribbon powder mixer.
Working process of horizontal Ribbon Blender:
The materials of various components enter the mixer after calculation according to the formula proportion, and the materials are mixed under the push of the ribbon spiral blade. The outer screw belt pushes the material from one end to the other section, the inner screw belt makes the material move in the opposite direction, the inner material is pushed to one side after the inside to roll out, the outer material is pushed to the other side after the outside to roll in. In the convection process, the two streams of material penetrate each other, become mixed, and then mix in the rolling process on both sides, so repeated for many times, and finally the boredom after mixing is discharged from the discharge door through the discharge control mechanism.
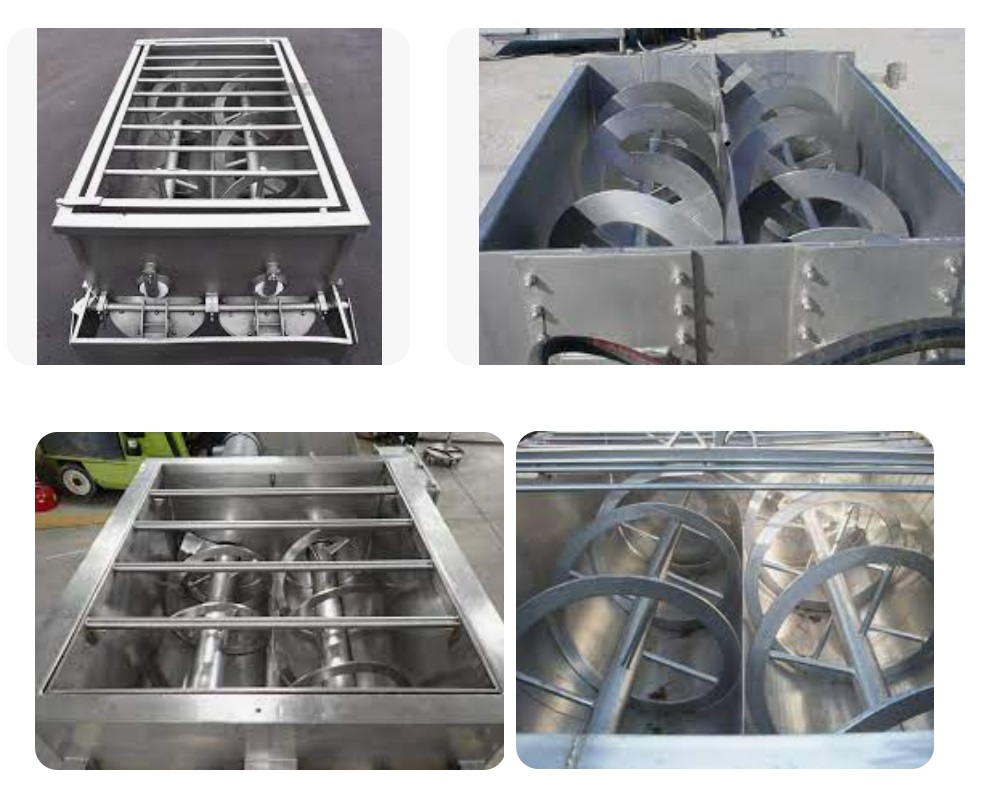
Equipment structure:
The bottom discharge mode of the mixer: the powder material adopts the pneumatic big door structure, which has the advantages of fast discharge and no residue. High fineness material or semi-fluid material using manual butterfly valve or pneumatic butterfly valve, manual butterfly valve is economical, pneumatic butterfly valve for semi-fluid sealing is good, but the cost is higher than manual butterfly valve. In the case of heating or cooling, the jacket can be configured. There are two heating methods: electric heating and thermal oil heating are optional: electric heating is convenient, but the heating speed is slow and the energy consumption is high; Heat conduction oil heating requires configuration of oil pan and oil guiding power, pipeline, large investment, but the heating speed is fast, low energy consumption. Cooling process can directly inject cooling water into the jacket, the jacket heat exchange area is large, cooling speed is fast. The motor and the mixing spindle are directly connected by cycloidal pin-wheel reducer, which has simple structure, high reliability and easy maintenance.
The Application of horizontal ribbon blender:
The horizontal ribbon mixer is generally used for the mixing of viscous or cohesive powder particles and the mixing of liquid and paste materials added to the powder particles. At the same time, due to the characteristics of difficult cleaning of viscous materials, it is suitable for mixing occasions with large output and infrequent replacement of varieties.
Horizontal ribbon mixer is widely used in putty paste, real stone paint, dry powder, putty, medicine, food, chemicals, feed, ceramics, refractory materials such as solid-solid (powder and powder), solid-slurry (powder and glue) mixing, especially suitable for thick material mixing. The mixer is not suitable for mixing materials with large fiber content and large density difference. Putty paste, real stone paint, biology, medicine, food and other industries, it is recommended to use stainless steel. Under normal circumstances, mixing dry powder mortar containing vitrified microbeads is recommended to use a horizontal ribbon mixer.

Horizontal Ribbon Blender features:
Material requirements:
According to the material situation, the user can choose ordinary carbon steel and stainless steel and other materials, if the material corrosion is too large, then you can choose the high-grade stainless steel material or choose the liner corrosion resistant layer, according to the material use level requirements of the surface treatment can be rough polishing, fine polishing, mirror polishing.
Horizontal Ribbon Blender selection principle:
At present, many users in the powder/powder mixing equipment to choose the original domestic vertical cone mixing equipment, but experts suggest that because the vertical cone mixer has many shortcomings, high maintenance rate, so in the powder/powder or granular material mixing, should choose the horizontal mixer, the equipment mixing efficiency is high, mixing quality is good, unloading time is short, residual amount is also small. However, the selection and use of horizontal mixer should pay attention to the following points:
- Bed mixer selected according to daily production. Because each batch of material processing time of the mixer is about 10 minutes, plus the time of discharging and feeding, each batch of material processing time can be measured by 15 minutes, then 4 batches of material can be processed continuously in 1 hour. If you choose a mixer with a processing capacity of 100 kg per batch, you can process 400 kg per hour. Users can choose horizontal mixers according to their needs.
- According to the working principle of the horizontal spiral belt mixer, the ability of the double spiral belt used for mixing to push the material in the opposite direction should be basically consistent. Because the pitch of the inner spiral belt should be smaller than the outer spiral belt, in order to achieve the ability to push the material is consistent, the pitch of the inner spiral belt should be smaller than the outer spiral belt, and the width should be greater than the outer spiral belt, otherwise the material will be concentrated in one direction. Therefore, pay attention to this when choosing a horizontal mixer.
- According to the design principle, the gap between the spiral belt and the shell in the spiral belt mixer can be 4 mm to 10 mm, and the material can be driven by friction to participate in the mixing. However, because the grinding particle size and the friction coefficient of the material are not the same, the time of mixing of various components of the material is not the same, resulting in the non-uniformity of the product. At present, some manufacturers have realized this point and made improvements to their products. One is to pay attention to the machining accuracy, so that the bottom gap is reduced to about 3 mm; The other is to make the position between the spindle and the housing in the form of adjustable, according to the amount of wear can often adjust the gap between the spiral belt and the housing. When choosing a mixer, these two forms of products should be a good choice.
- Choose horizontal spiral belt mixer to pay attention to the discharge method. Should communicate with the supplier in time to choose the valve form suitable for their own process, and do not choose the discharge form of the side mouth. The reason is that when the mixer completes mixing at the specified time, the uniformity of the material can be ensured by clearing it once in a short time; If the side screw belt is gradually released, one is to delay the time, not to reach the expected productivity, the second is that the material has reached a good uniformity, excessive mixing will make the material segregation, destroy the uniformity, thus losing the significance of choosing a horizontal mixer.
- When using horizontal mixer, pay attention to the order of feeding. Generally, aniseed is first cast, such as corn meal, soybean meal, etc., and then cast group feed, such as premix. Pay attention to the premix must not be fed by the screw elevator, the application of one-time tipping bucket feeding, or manual feeding, so as to avoid the segregation and loss of the active ingredients in the premix.
- The horizontal mixer should be fed batch by batch after the mixer is started. Do not stop when the mixing is finished, and mix a batch after the net material. If you start again after full load, it will cause the power distance to be too large and burn the motor.
In short, the Ribbon Blender is an important industrial equipment, with good mixing effect, simple operation, strong adaptability and easy to clean and so on. It is widely used in the food, chemical and building materials fields, and has advantages over other mixing equipment. Choosing a suitable horizontal mixer and using it properly will significantly improve the quality of the mixture and quickly reflect the positive effect in the production process. If you can further master the technology of self-mixing, you can also greatly reduce the cost of materials, thereby increasing profits.
You may also interest in:
About LKMixer
LK Mixer is a professional manufacturer for fertilizer production line, grinder, mixer and granulator, shredder. These machines are widely used in food, pharmaceutical, cosmetic, health care products and chemical industries. The Food materials like Peanut, mushroom, seeds, potato, bean, tobacco, salt, cannabis, tea, Sugar, corn, Coffee, rice, pepper, grain as so on. Grinders have many types such as Pulse Dust Grinder which suitable for zero pollution environment, Turbine Mill which is suitable for coffee bean, 12-120mesh all can meet, Ultrafine Grinding Mill covers 80-200mesh, and also Winnowing Dust Grinder or other grinding machines like SF Hammer. Welcome to contact us for details.