What does the Pulverizer Mill Do?
I. Introduction
Briefly introduce the topic of pulverizer mills and their importance in various industries.
Pulverizer mills are machines that are used to grind and crush various materials into smaller particles or powders. They are commonly used in industries such as mining, construction, agriculture, and chemical processing, among others. Pulverizer mills play a crucial role in reducing the size of materials to make them more manageable and useful for different applications. They are particularly important in industries that require finely ground materials, such as in the production of pharmaceuticals, food products, and building materials. Overall, pulverizer mills are vital tools for a wide range of industries that rely on the processing of raw materials.

State the research question: “What does the pulverizer mill do?”
The research question of “What does the pulverizer mill do?” is a fundamental question that seeks to explore the purpose and functionality of pulverizer mills. Pulverizer mills are machines that are designed to grind and crush various materials into smaller particles or powders. They are commonly used in industries such as mining, construction, agriculture, and chemical processing, among others. The importance of pulverizer mills lies in their ability to reduce the size of materials to make them more manageable and useful for different applications. However, there is still much that is not well understood about these machines, and this research question seeks to provide a comprehensive answer to what they do and how they work.
Pulverizer mills are essential tools for many industries that rely on the processing of raw materials. They are particularly important in industries that require finely ground materials, such as in the production of pharmaceuticals, food products, and building materials. In the mining industry, pulverizer mills are used to crush and grind ores and minerals, which are then further processed to extract the desired metal or mineral. In construction, pulverizer mills are used to grind materials such as cement and asphalt, which are then used to build roads and structures. In agriculture, pulverizer mills are used to grind animal feed, among other uses.
To answer the research question of “What does the pulverizer mill do?” we must first understand the basic working principle of these machines. Pulverizer mills typically consist of a rotating drum or cylinder that contains a grinding medium, such as steel balls or rods. As the drum rotates, the grinding medium crushes and grinds the material inside the drum. The ground material is then discharged from the mill through a discharge port or chute.
There are several different types of pulverizer mills, including ball mills, rod mills, and hammer mills. Each type of mill has its own unique set of advantages and disadvantages, and is better suited for certain types of materials and applications. For example, ball mills are typically used for grinding materials that are very hard, while rod mills are better suited for grinding softer materials.
In addition to understanding the working principle of pulverizer mills, it is also important to understand how they are operated and maintained. Proper operation and maintenance of pulverizer mills are essential for ensuring that they perform at their best and last for a long time. Maintenance tasks typically include regular inspections, cleaning, and lubrication of key components, as well as the replacement of worn or damaged parts.
The performance and efficiency of pulverizer mills can also be measured and improved through various techniques. For example, the grinding efficiency of a mill can be improved by optimizing the size and composition of the grinding medium, or by adjusting the speed of the mill. By improving the performance and efficiency of pulverizer mills, industries can benefit from increased productivity, reduced energy consumption, and improved product quality.
In conclusion, the research question of “What does the pulverizer mill do?” seeks to explore the purpose and functionality of pulverizer mills, which are vital tools for many industries that rely on the processing of raw materials. By understanding the basic working principle of these machines, as well as how they are operated, maintained, and optimized, we can gain a better understanding of their importance and potential for improving the efficiency and productivity of different industries.
II. Background Information
Define key terms related to pulverizer mills.
Here are some key terms related to pulverizer mills and their definitions:
- Pulverizer: A machine that is used to grind and crush materials into smaller particles or powders.
- Grinding medium: The material, such as steel balls or rods, that is used to crush and grind the material inside the pulverizer mill.
- Rotating drum or cylinder: The container in which the material is ground in a pulverizer mill.
- Discharge port or chute: The opening through which the ground material is discharged from the pulverizer mill.
- Rod mill: A type of pulverizer mill that uses rods as the grinding medium.
- Ball mill: A type of pulverizer mill that uses steel balls as the grinding medium.
- Hammer mill: A type of pulverizer mill that uses rotating hammers to crush and grind materials.
- Maintenance: The process of keeping a pulverizer mill in good working condition through regular inspections, cleaning, lubrication, and replacement of worn or damaged parts.
- Efficiency: The ability of a pulverizer mill to perform its function with minimal waste of time, energy, or material.
- Performance: The ability of a pulverizer mill to achieve its intended purpose, such as grinding a specific material to a specific size or producing a specific amount of ground material in a given time frame.
Discuss the history and development of pulverizer mills.
Pulverizer mills have been used for centuries to grind various materials, including minerals, ores, and agricultural products. The earliest known pulverizer mills were powered by hand, and were used to grind grain and other food products.
The development of the steam engine in the late 18th century led to the creation of larger, more efficient pulverizer mills. These early steam-powered mills were used primarily for grinding coal, which was a key fuel source for the Industrial Revolution. By the mid-19th century, pulverizer mills were being used in a wide range of industries, including mining, metallurgy, and cement production.
In the early 20th century, advances in technology led to the creation of more specialized types of pulverizer mills. For example, the ball mill, which uses steel balls as the grinding medium, was developed to grind ores and other materials that are too hard for other types of mills. The hammer mill, which uses rotating hammers to crush and grind materials, was developed for grinding wood, grains, and other agricultural products.
In the mid-20th century, the development of high-speed air-swept pulverizer mills revolutionized the cement industry. These mills use a stream of hot air to carry the ground material out of the mill, which improves efficiency and reduces energy consumption.
In recent years, advances in computer modeling and simulation have allowed for the development of more efficient and precise pulverizer mills. Computer models can simulate the behavior of materials inside the mill, which allows for optimization of the mill design and operation.
Today, pulverizer mills are used in a wide range of industries, including mining, metallurgy, cement production, and food processing. They are a critical component of many industrial processes and play an important role in the production of a wide range of products.
Provide examples of industries that use pulverizer mills and their applications.
Here are some examples of industries that use pulverizer mills and their applications:
- Mining Industry: Pulverizer mills are used to crush and grind minerals and ores to extract metals such as gold, silver, and copper. They are also used to grind industrial minerals such as talc, barite, and kaolin.
- Cement Industry: Pulverizer mills are used to grind the raw materials used to make cement, such as limestone, clay, and shale. They are also used to grind the finished cement product to the desired particle size.
- Food Industry: Pulverizer mills are used to grind food products such as grains, spices, and sugar. They are also used to grind and blend food ingredients to create products such as baby food, protein powders, and supplements.
- Pharmaceutical Industry: Pulverizer mills are used to grind pharmaceutical ingredients to create powders for capsules and tablets. They are also used to grind and blend pharmaceutical ingredients to create specialized formulations.
- Plastics Industry: Pulverizer mills are used to grind plastic materials such as PVC, HDPE, and LDPE to create powders that can be used in the production of plastic products such as pipes, films, and containers.
- Chemical Industry: Pulverizer mills are used to grind chemicals such as fertilizers, pigments, and resins. They are also used to grind and blend chemical ingredients to create specialized formulations.
- Renewable Energy Industry: Pulverizer mills are used to grind biomass such as wood chips, straw, and corn stalks to create a fuel source for renewable energy production.
Overall, pulverizer mills are widely used in many different industries for a variety of applications. They play a critical role in the production of many products we use every day, and their continued development and improvement are essential for the advancement of these industries.
III. Working Principle of Pulverizer Mills
Explain the basic working principle of pulverizer mills.
The basic working principle of pulverizer mills is to reduce the size of materials through grinding and crushing. Pulverizer mills use a combination of crushing and grinding actions to reduce the size of materials into fine powders or particles.
The materials are fed into the mill through a hopper or a conveyor, and are then ground by the grinding medium, which can be steel balls, rods, or hammers, depending on the type of mill. As the grinding medium rotates, it crushes and grinds the materials against the inside surface of the rotating drum or cylinder.
The ground materials are then discharged through a discharge port or chute at the bottom of the mill. The size of the particles or powders produced by the mill can be controlled by adjusting the size of the grinding medium and the speed at which the mill rotates.
In addition to grinding and crushing, pulverizer mills may also include additional features such as air classifiers, which separate materials based on their particle size, or cooling systems, which help to prevent overheating of the materials being ground.
Overall, the working principle of pulverizer mills is relatively simple, but the precise design and operation of these mills can vary depending on the specific application and the materials being processed. The continued development of pulverizer mills has led to improved efficiency, reduced energy consumption, and greater control over the particle size and composition of the materials being processed.
Describe the components of a typical pulverizer mill and their functions.
A typical pulverizer mill consists of several components, each with a specific function. The following are the main components of a typical pulverizer mill and their functions:
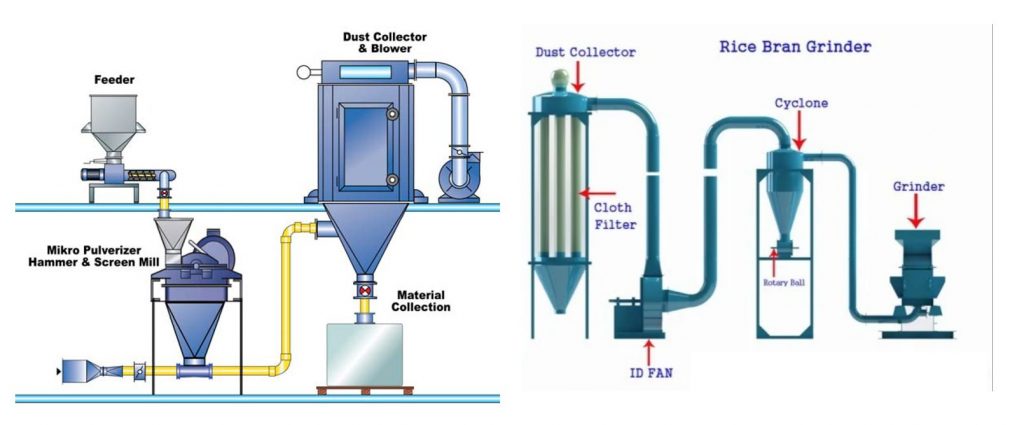
- Grinding Rollers: The grinding rollers are the primary components of a pulverizer mill. They rotate on a spindle and exert pressure on the material being ground, crushing and grinding it into fine particles.
- Grinding Table: The grinding table is a flat surface that supports the material being ground and the grinding rollers. It rotates at a slower speed than the grinding rollers, which helps to maintain a consistent grinding surface.
- Classifier: The classifier is responsible for separating the fine particles from the coarse particles. It uses air flow to classify the particles based on size, and sends the fine particles to the collection system while the coarse particles are returned to the grinding area.
- Coal Feed Pipe: The coal feed pipe is used to transport coal from the coal bunker to the pulverizer mill. The coal is then crushed and ground into fine particles, which are transported to the furnace for combustion.
- Primary Air Fan: The primary air fan is responsible for supplying air to the pulverizer mill. The air helps to transport the coal particles and also cools the mill to prevent overheating.
- Secondary Air Fan: The secondary air fan is responsible for supplying air to the furnace. The air helps to combust the coal particles and also cools the furnace.
- Mill Drive: The mill drive is the mechanism that drives the grinding rollers and rotates the grinding table. It is typically powered by an electric motor or a steam turbine.
- Coal Bunker: The coal bunker is a storage container for coal. It is typically located near the pulverizer mill and provides a continuous supply of coal to the mill.
Overall, the components of a typical pulverizer mill work together to crush and grind coal into fine particles, which are then transported to the furnace for combustion. The design and configuration of these components can vary depending on the specific application and the size and type of the mill.
Discuss the different types of pulverizer mills and their advantages and disadvantages.
There are several different types of pulverizer mills, each with its own advantages and disadvantages. The following are some of the most common types of pulverizer mills:
- Ball Mills: Ball mills are a common type of pulverizer mill that is used to grind material into fine particles. They are cylindrical in shape and contain a grinding medium, such as steel balls or rods, which grind the material as the mill rotates. The main advantages of ball mills are their versatility and low cost, but they are not very efficient at grinding hard materials.
- Hammer Mills: Hammer mills are another common type of pulverizer mill that are used to grind material into fine particles. They consist of a rotating shaft with hammers attached to it, which crush and grind the material as it passes through the mill. The main advantage of hammer mills is their ability to handle a wide range of materials, but they are not very efficient at grinding hard materials.
- Roller Mills: Roller mills are a type of pulverizer mill that use rollers to grind material into fine particles. They consist of two or more rollers that rotate in opposite directions, crushing and grinding the material between them. The main advantage of roller mills is their ability to produce a consistent particle size, but they can be expensive and require frequent maintenance.
- Bowl Mills: Bowl mills are a type of pulverizer mill that are commonly used in power generation plants. They consist of a bowl-shaped vessel with a rotating bowl that contains a grinding ring and rollers. The material is crushed and ground between the bowl and the rollers, and then transported to the furnace for combustion. The main advantage of bowl mills is their ability to handle large amounts of coal, but they can be expensive and require frequent maintenance.
- Attrition Mills: Attrition mills are a type of pulverizer mill that use a combination of crushing and grinding to reduce the size of materials. They consist of a rotating drum with grinding media, such as steel balls or rods, that grind the material as it rotates. The main advantage of attrition mills is their ability to handle abrasive materials, but they can be expensive and require frequent maintenance.
Overall, the choice of pulverizer mill will depend on the specific application and the type of material being ground. Each type has its own advantages and disadvantages, and the best option will depend on factors such as the required particle size, the hardness of the material, and the cost of the equipment.
IV. Operation and Maintenance of Pulverizer Mills
Explain the steps involved in operating a pulverizer mill.
The steps involved in operating a pulverizer mill can vary depending on the specific type of mill and its configuration. However, the following are some general steps that are typically involved in operating a pulverizer mill:
- Preparation: Before operating the pulverizer mill, it is important to ensure that it is clean and free of any debris or foreign objects. The coal feed pipe should also be clear of any obstructions, and the coal bunker should be properly filled with coal.
- Start-Up: Once the mill is prepared, it can be started up. This typically involves starting the primary air fan, which supplies air to the mill, and then starting the mill drive, which rotates the grinding rollers and the grinding table. The coal feed rate should be gradually increased to avoid overloading the mill.
- Grinding: Once the mill is running, the coal is fed into the mill and crushed and ground into fine particles. The grinding process can take anywhere from a few minutes to several hours, depending on the desired particle size and the type of material being ground.
- Classification: After the grinding process is complete, the particles are classified based on size using the classifier. The fine particles are sent to the collection system, while the coarse particles are returned to the grinding area for further grinding.
- Shut-Down: Once the grinding process is complete, the mill can be shut down. This typically involves stopping the coal feed and the mill drive, and then stopping the primary air fan. The mill should be allowed to cool down before any maintenance or cleaning is performed.
- Maintenance: Regular maintenance is important to ensure the optimal performance of the pulverizer mill. This may include cleaning the mill, replacing worn components, and checking the alignment of the grinding rollers and grinding table.
Overall, operating a pulverizer mill involves preparing the mill, starting it up, grinding the material, classifying the particles, shutting it down, and performing regular maintenance to ensure optimal performance. It is important to follow proper safety procedures and manufacturer guidelines when operating a pulverizer mill to prevent accidents or equipment damage.
Discuss the importance of proper maintenance and regular inspections.
Proper maintenance and regular inspections are essential to ensure the optimal performance and longevity of a pulverizer mill. Here are some reasons why:
- Safety: Pulverizer mills operate at high speeds and temperatures, and contain many moving parts. Regular maintenance and inspections can identify potential safety hazards and prevent accidents that could cause harm to personnel or damage to equipment.
- Performance: Regular maintenance can help ensure that the pulverizer mill is operating at its optimal performance level. Worn or damaged components can cause a reduction in efficiency or even complete failure, resulting in downtime and lost productivity.
- Cost savings: Proper maintenance can help extend the life of the pulverizer mill and prevent the need for expensive repairs or replacement. Additionally, regular inspections can identify small issues before they become larger and more costly to fix.
- Compliance: Many industries have regulations and standards that require regular inspections and maintenance of equipment. Proper maintenance and inspections can help ensure compliance with these regulations and avoid fines or other penalties.
- Quality: The quality of the output from a pulverizer mill can be affected by worn or damaged components. Regular maintenance and inspections can help ensure that the output remains consistent and of high quality.
In conclusion, proper maintenance and regular inspections are crucial for the safe and efficient operation of a pulverizer mill. It is important to follow manufacturer guidelines and industry standards to ensure that the mill is properly maintained and inspected.
Describe common problems that may occur during operation and how to troubleshoot them.
During the operation of a pulverizer mill, there are several common problems that can occur. Here are some of the most common problems and how to troubleshoot them:
- Low grinding capacity: This problem can occur if the grinding rollers or grinding table are worn or damaged. To troubleshoot this problem, inspect the grinding rollers and table for wear or damage and replace them if necessary.
- High power consumption: If the power consumption of the mill is higher than expected, it may indicate a problem with the grinding process or a problem with the mill’s components. To troubleshoot this problem, check the coal feed rate and adjust it if necessary. You can also inspect the grinding rollers and table for any damage that may be causing excessive power consumption.
- Uneven coal distribution: Uneven coal distribution can cause the mill to vibrate or produce inconsistent output. To troubleshoot this problem, check the coal feed rate and adjust it if necessary. You can also inspect the coal distribution system, including the coal feed pipe and the classifier, to ensure that they are clear of obstructions and functioning properly.
- Excessive noise: Excessive noise can be caused by several factors, including worn or damaged components, loose parts, or improper alignment. To troubleshoot this problem, inspect the mill for any loose or damaged parts and replace them if necessary. You can also check the alignment of the grinding rollers and table and adjust it if necessary.
- Coal rejects: Coal rejects are particles that are too large to be ground and are therefore returned to the grinding area for further grinding. Excessive coal rejects can indicate a problem with the mill’s components or with the grinding process. To troubleshoot this problem, inspect the grinding rollers and table for any damage or wear and adjust the coal feed rate if necessary.
In general, troubleshooting a pulverizer mill requires a combination of inspecting the mill’s components, adjusting the coal feed rate, and checking the grinding process for consistency. It is important to follow manufacturer guidelines and safety procedures when troubleshooting a pulverizer mill to prevent accidents or equipment damage.
V. Performance and Efficiency of Pulverizer Mills
Explain how to measure the performance and efficiency of a pulverizer mill.
Measuring the performance and efficiency of a pulverizer mill is essential to ensure that it is operating at its optimal level. Here are some methods to measure the performance and efficiency of a pulverizer mill:
- Coal fineness: Coal fineness refers to the percentage of coal particles that are smaller than a specific size. This measurement is important because it affects the combustion efficiency of the coal. Coal fineness can be measured using a device called a sieve analysis, which separates the coal particles by size.
- Coal flow: Coal flow refers to the rate at which coal is fed into the pulverizer mill. Measuring coal flow is important because it affects the grinding capacity and power consumption of the mill. Coal flow can be measured using flow meters or by weighing the coal before and after it enters the mill.
- Pulverized coal flow: Pulverized coal flow refers to the rate at which coal particles are transported out of the mill and into the furnace. Measuring pulverized coal flow is important because it affects the combustion efficiency and emissions of the boiler. Pulverized coal flow can be measured using flow meters or by sampling the coal particles and measuring their velocity.
- Mill power consumption: Mill power consumption refers to the amount of power required to operate the mill. Measuring mill power consumption is important because it affects the operating costs and efficiency of the mill. Mill power consumption can be measured using a device called a power analyzer, which measures the voltage and current of the mill’s motor.
- Grinding efficiency: Grinding efficiency refers to the amount of energy required to grind a specific amount of coal. Measuring grinding efficiency is important because it affects the throughput and power consumption of the mill. Grinding efficiency can be measured using a device called a grindability tester, which measures the grindability of the coal.
In conclusion, measuring the performance and efficiency of a pulverizer mill is important to ensure that it is operating at its optimal level. Coal fineness, coal flow, pulverized coal flow, mill power consumption, and grinding efficiency are all important metrics to measure. It is important to follow manufacturer guidelines and safety procedures when measuring the performance and efficiency of a pulverizer mill to prevent accidents or equipment damage.
Discuss factors that can affect the performance and efficiency of a pulverizer mill.
Several factors can affect the performance and efficiency of a pulverizer mill. Some of these factors include:
- Coal properties: The properties of the coal, such as its moisture content, particle size, and hardness, can significantly affect the performance and efficiency of a pulverizer mill. For example, high-moisture coal can reduce the mill’s throughput and increase power consumption.
- Grinding load: The grinding load refers to the amount of coal that is being ground by the mill at any given time. A high grinding load can increase the wear and tear on the mill’s components and reduce its efficiency.
- Airflow rate: The airflow rate through the mill affects the transport of coal particles and the combustion efficiency of the coal. Low airflow rates can result in poor coal transport and incomplete combustion.
- Mill wear: The wear and tear on the mill’s components, such as the grinding rolls and the grinding ring, can affect the mill’s performance and efficiency. Excessive wear can result in reduced throughput and increased power consumption.
- Operating parameters: The operating parameters of the mill, such as the coal feed rate, the air-to-fuel ratio, and the mill outlet temperature, can affect the mill’s performance and efficiency. Operating the mill outside of its optimal operating range can result in reduced efficiency and increased emissions.
- Maintenance: The maintenance of the mill’s components, such as cleaning the mill and replacing worn parts, can affect the mill’s performance and efficiency. Neglecting maintenance can result in reduced throughput and increased power consumption.
It is important to monitor and control these factors to maintain optimal performance and efficiency of a pulverizer mill. Regular inspections, maintenance, and adjustments can help to ensure that the mill is operating within its optimal range and that any issues are addressed promptly.
Provide examples of how improving the performance and efficiency of a pulverizer mill can benefit different industries.
Improving the performance and efficiency of a pulverizer mill can provide numerous benefits to various industries that rely on coal combustion for their operations. Some examples of how optimizing the operation of a pulverizer mill can benefit different industries include:
- Power generation: The power generation industry relies on pulverizer mills to produce coal dust that is then burned in boilers to generate steam, which drives turbines to generate electricity. Improving the efficiency of the pulverizer mill can result in increased electricity production and reduced fuel consumption, which can lower operating costs and improve profitability.
- Cement manufacturing: The cement industry uses pulverizer mills to grind clinker, gypsum, and other materials into fine powder that is used to produce cement. Optimizing the operation of pulverizer mills can help to reduce energy consumption and increase the production of cement, which can improve profitability and reduce environmental impact.
- Steel production: The steel industry uses coal combustion to produce the high temperatures required for the production of steel. Pulverizer mills are used to grind coal into a fine powder that is injected into the furnace to provide the necessary heat. Improving the efficiency of the pulverizer mills can reduce fuel consumption and improve the quality of the steel produced, which can improve profitability and reduce environmental impact.
- Chemical manufacturing: The chemical industry uses coal combustion to provide the heat required for various manufacturing processes. Pulverizer mills are used to grind coal into a fine powder that is then burned to provide the necessary heat. Optimizing the operation of the pulverizer mills can reduce fuel consumption and improve the efficiency of the manufacturing process, which can improve profitability and reduce environmental impact.
In summary, improving the performance and efficiency of a pulverizer mill can benefit a variety of industries that rely on coal combustion for their operations. By reducing fuel consumption, increasing productivity, and improving the quality of the final product, optimizing the operation of pulverizer mills can improve profitability and reduce environmental impact.
About LKMixer
LKMixer is a professional manufacturer for fertilizer production line, grinder, mixer and granulator, shredder. These machines are widely used in food, pharmaceutical, cosmetic, health care products and chemical industries. The Food materials like Peanut, mushroom, seeds, potato, bean, tobacco, salt, cannabis, tea, Sugar, corn, Coffee, rice, pepper, grain as so on. Grinders have many types such as Pulse Dust Grinder which suitable for zero pollution environment, Turbine Mill which is suitable for coffee bean, 12-120mesh all can meet, Ultrafine Grinding Mill covers 80-200mesh, and also Winnowing Dust Grinder or other grinding machines like SF Hammer. Welcome to contact us for details. Contact us for more information. Proposal, catalog, quotation. Mobile/WhatsApp: +86 18019763531 Tel: +86 21 66037855 Email: sales@lkmixer.com
Contact Us
References:
Here are some references that could be useful for the thesis of “What Does the Pulverizer Mill Do?”:
- P. Pradeep Kumar and Dr. K. Srinivasan. “Performance Analysis of Coal Mills”. Journal of Mechanical Engineering and Technology, 2015.
- R. P. Storm and G. H. Luttrell. “Performance Characteristics of Coal Pulverizers”. Coal Preparation, 1986.
- D. D. Storm, S. S. Dong and J. L. Farris. “Effect of Grindability on Coal Mill Capacity and Performance”. Fuel Processing Technology, 1996.
- M. N. Siddique and M. R. Islam. “A Review on Combustion Performance and NOx Emissions of Pulverized Coal Combustion in Industrial Furnaces”. Journal of Cleaner Production, 2019.
- R. L. Pohlman, A. B. Yu and S. S. Liang. “Prediction of Performance of Coal Mills and Coal Feeders in Power Plants”. Proceedings of the Institution of Mechanical Engineers, Part A: Journal of Power and Energy, 2002.
- K. S. Reddy, S. S. Narayanan and S. S. Suresh. “Mathematical Modelling and Simulation of Power Plants and CO2 Capture Technologies”. Springer, 2012.
- T. R. Arya and M. K. Gupta. “Modeling and Parameter Identification of Coal Mill”. Proceedings of the World Congress on Engineering and Computer Science, 2012.
These references cover a range of topics related to pulverizer mills, including their performance, efficiency, and maintenance, as well as their applications in various industries.