What Is Blender?
Definition of Blender:
Blender is a automatic mechanical equipment that uses mechanical force and gravity to evenly mix two or more kinds of materials. In the mixing process, it can not only mix a variety of materials into a uniform mixture, such as gravel, sand, cement and water mixed into wet concrete, but also increase the contact surface area between materials, thereby promoting the chemical reaction, but also accelerate the occurrence of physical changes. LINKER electric Mixer has various stainless steel mixers for sale.
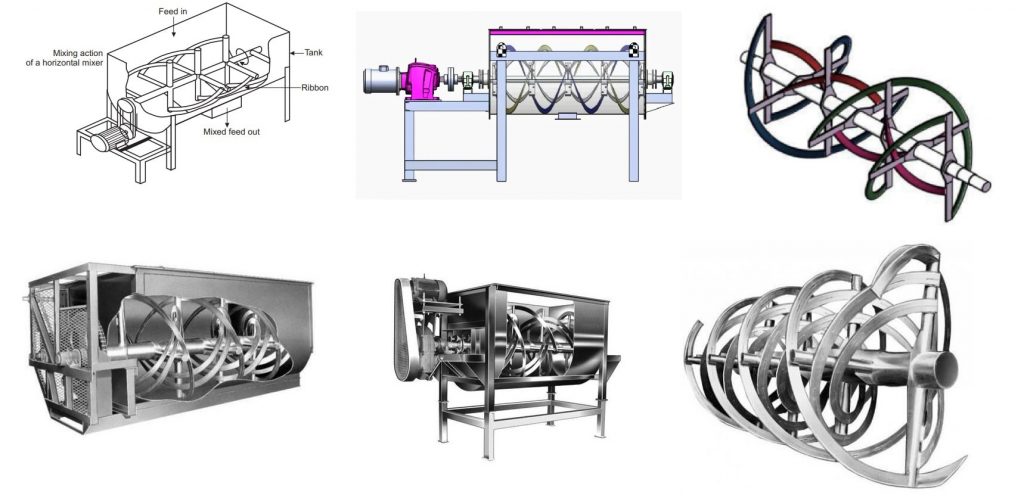
Classification of Blenders:
Common Blenders can be divided into the following three categories: gas and low viscosity liquid mixers, medium and high viscosity liquid and paste mixers, and powder and granular solid material mixers. These Blenders play an important role in industrial production, meeting the needs of different material mixing, improving production efficiency and product quality. Gas and low-viscosity liquid mixers are characterized by simple structure, no rotating parts, small maintenance and repair, and low energy consumption. This type of mixer mainly includes four types of air flow mixing, pipeline mixing, jet mixing and forced circulation mixing. Medium and high viscosity liquid and paste mixing machinery usually has a strong shearing action. The thermoplastic material mixer is mainly used for the mixing of thermoplastic materials and additives. Powder and granular solid material mixing machinery is mostly intermittent operation, including machinery with mixing and grinding, such as wheel rolling machines.
Blenders can also classified to: V-type mixers, ribbon mixers, no-gravity mixers, horizontal pear knife mixers and double spiral conical mixers. According to the different working principles, mixers can be further divided into gravity controlled mixers (such as cylindrical mixers, disk granulates, etc.), stirring mixers (such as plow knife mixers, paddle mixers, screw mixers, etc.) and high-shear mixers.
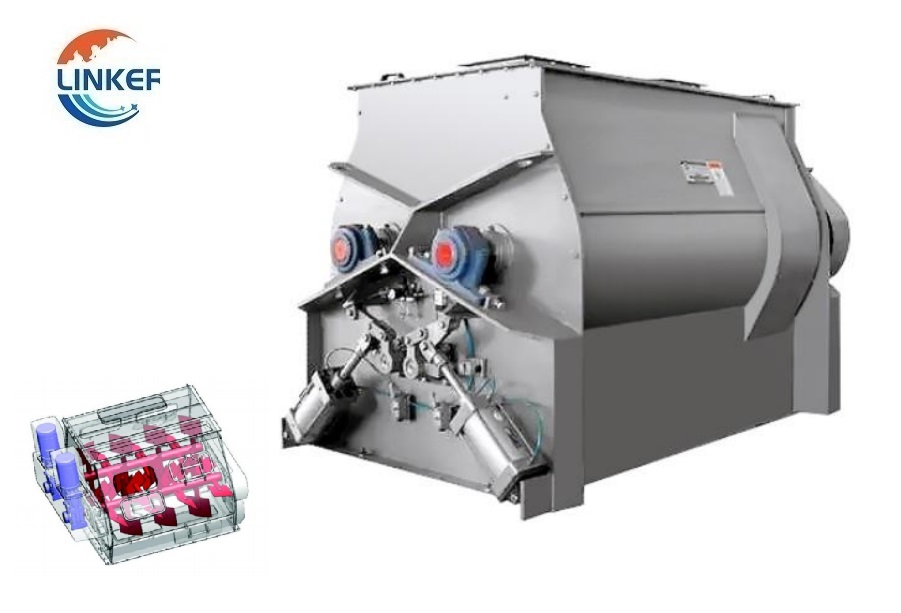
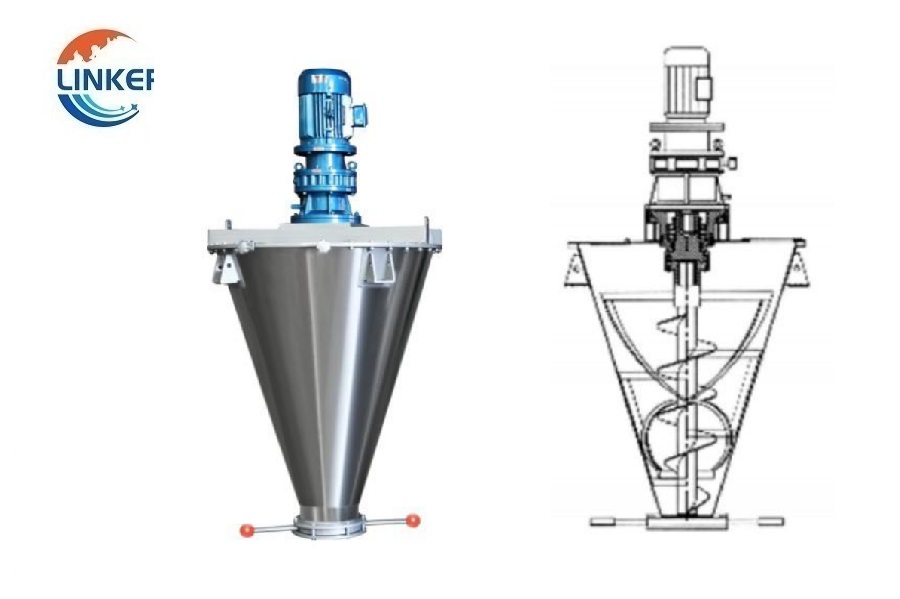
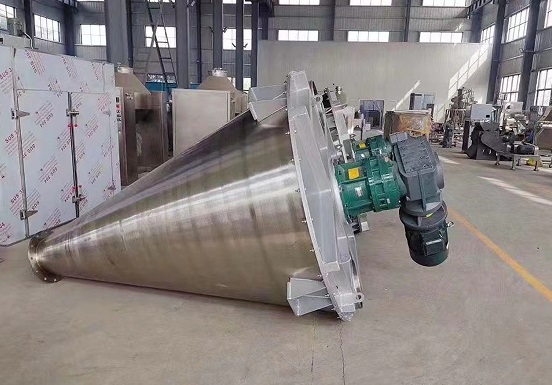
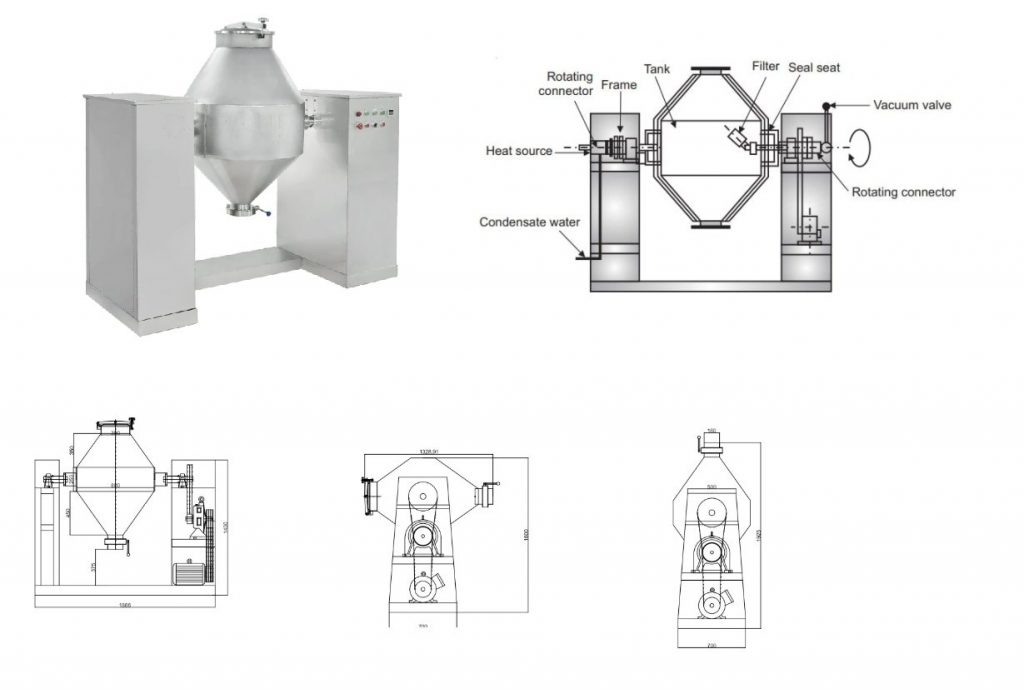
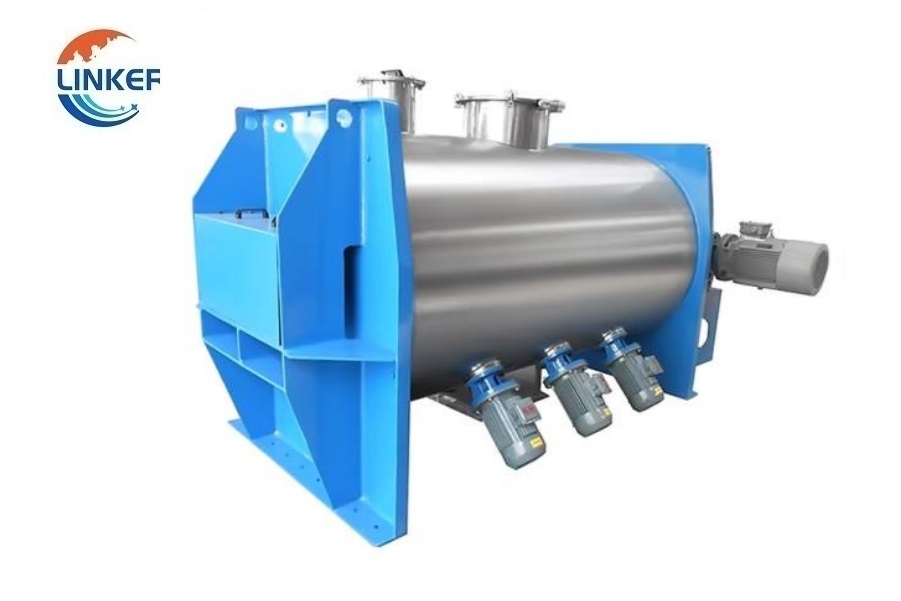
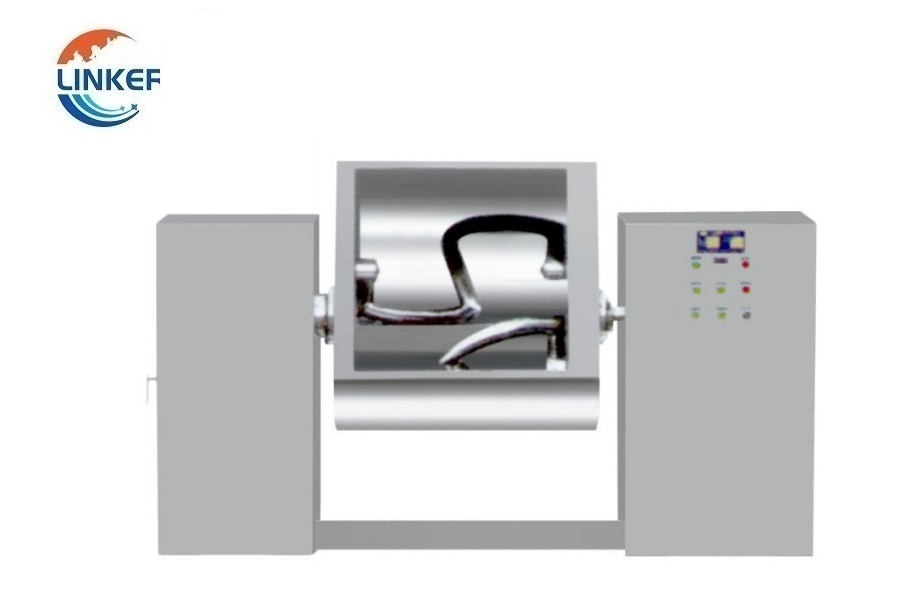
The gravity controlled Blenders mainly relies on different fuselage geometries or mechanical motion modes to make the particle system produce complex material mixing motion under its own gravity. The stirring Blenders mixes the material into the warehouse through the external mechanical force to improve the mixing degree of the material. The high-shear mixer uses a high-speed rotating impeller to vigorously stir the granular material laid on it to achieve the mixing effect, which is actually a special form of mixing mixer.
Working Principles of Various Blenders:
Horizontal Plow Knife Mixer:
The horizontal plow knife mixer comprises four main components: the driving structure, horizontal barrel, plow knife, and flying knife. Material movement occurs radially along the cylinder wall under the cutter’s action, with centrifugal vortex movement generated by the cutter’s sides. This results in three-dimensional diffusion and mixing of stressed materials. Shear stirring by the high-speed rotating cutter disperses the material strongly, achieving uniform mixing rapidly. This mixer accommodates solid-liquid mixing, wet granulation, drying, and other composite processes, making it particularly suitable for viscous or gelatinous additive mixing.
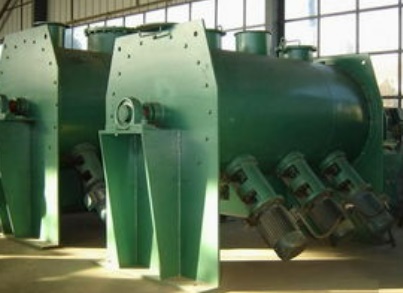
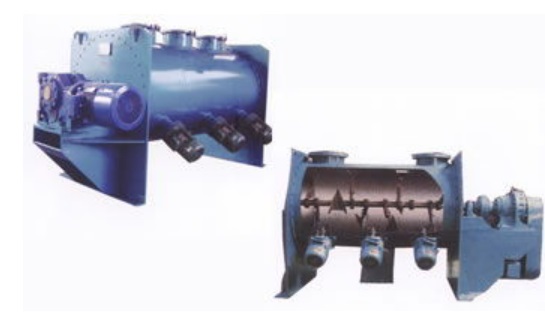
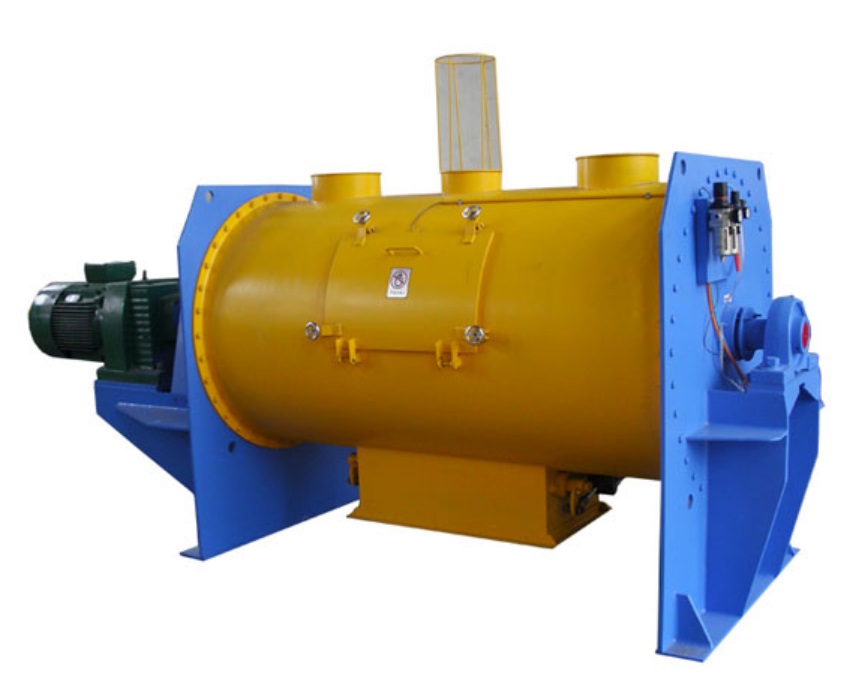
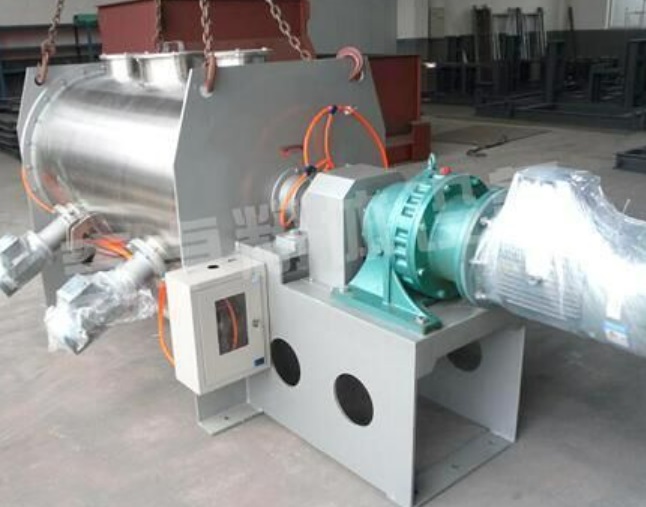
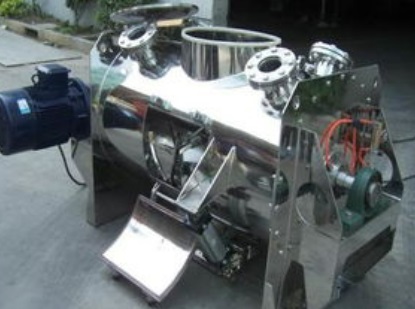
Double Helix Conical Mixer:
Main Uses: This mixer is a high-efficiency particle mixing equipment widely applied across various industries for powder particles’ precise mixing.
Main Characteristics:
Advanced structure, easy operation, and reliable safety features.
High-speed, uniformly mixed products facilitated by the asymmetrical arrangement of the double helix, ideal for materials of varying proportions.
Remarkable energy-saving performance, consuming only one-tenth of the energy used by drum mixers.
Minimal wear and pressure on granular materials, suitable for heat-sensitive material mixing without overheating reactions.
Stable mixed preparation without stratification or segregation.
Dust-free, sealed design ensures simple operation, easy maintenance, and extended service life. Can be customized into a pressure vessel for specific operational requirements.
Equipped with a motor and cycloidal pin transmission reducer for auto and smooth revolution.
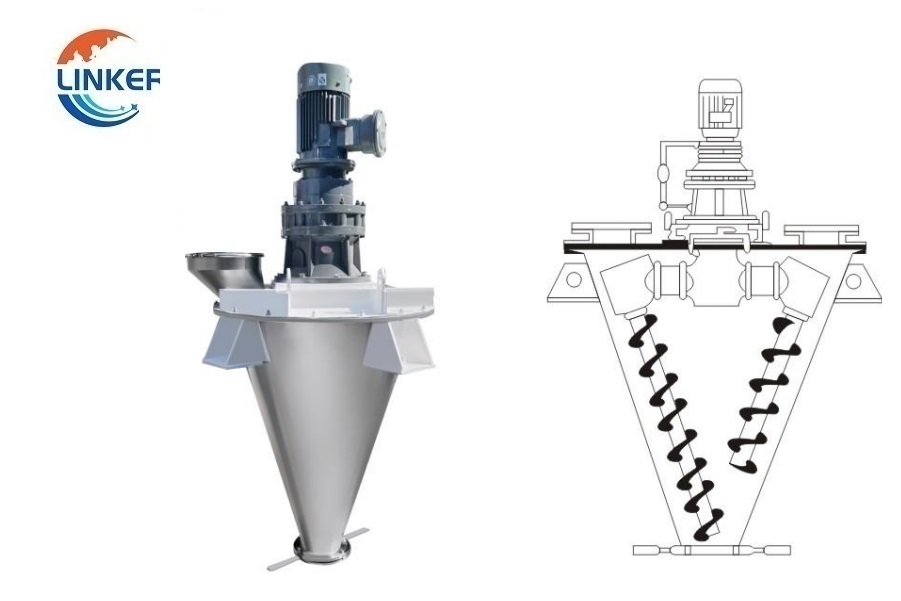
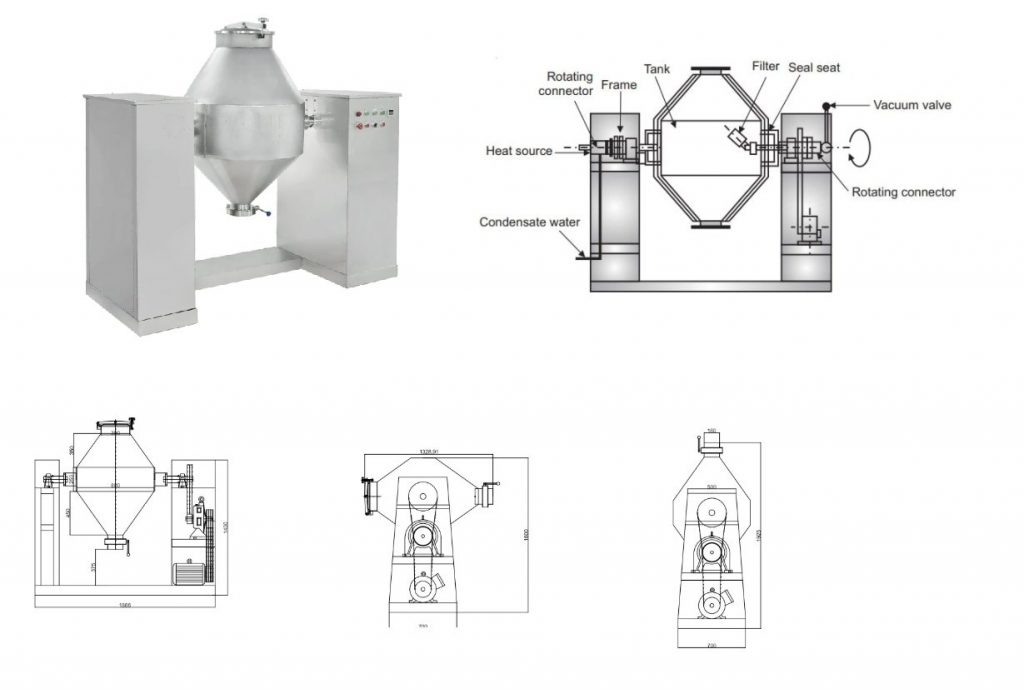
Working Principle:
Powder particles rotate around the cone wall due to the double helix’s rotation.
The powder is discharged to the cone’s center for radial movement by the spiral blade’s auto.
Powder flows upward from the cone’s bottom, mixed via upward and downward movements caused by spiral rotation, forming a composite movement of convection, shear, diffusion, and infiltration for rapid and uniform mixing.
Horizontal Ribbon Mixer:
The horizontal double-axis screw belt mixer ensures even mixing of dry powdery materials. Materials inside undergo compound movement propelled by two rotors moving oppositely. Axial and rotational movements cause convective circulation and shear infiltration, achieving rapid and uniform mixing in a short time. The horizontal screw belt mixer consists of a mixing bin, agitator, and driving device. A U-shaped tubular bin houses the double-layer, oppositely wound screw belt agitator shaft. The outer spiral belt, powered, transports materials from both ends of the U-shaped bin to the central zone, while the inner spiral belt moves material from the middle to the ends, promoting convection-mixing. The discharge port is positioned at the bottom center of the mixer’s horizontal cylinder. The outer spiral belt’s rotation direction coordinates with the main shaft to ensure material discharge from the cylinder’s central port.
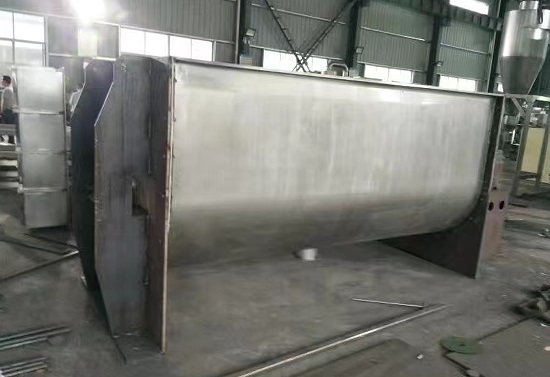
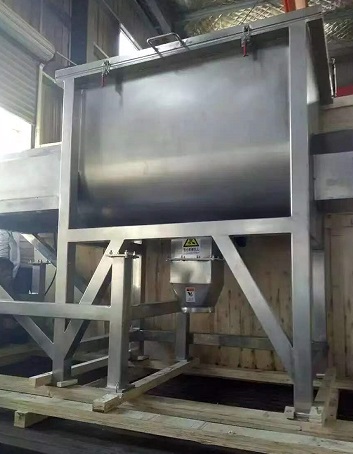
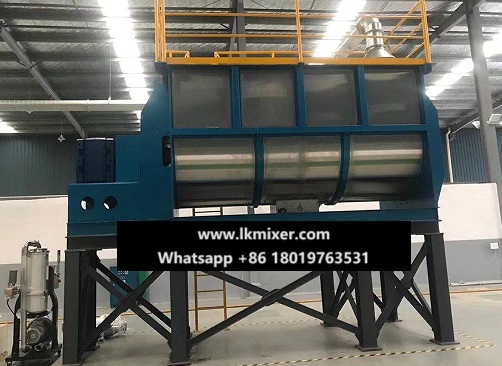
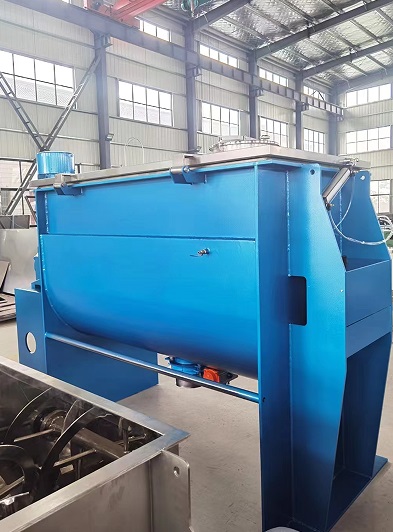
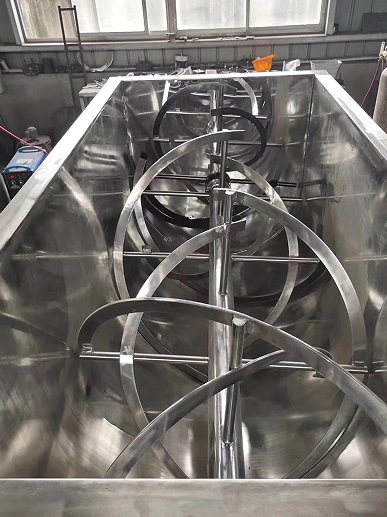
Product Features:
U-shaped barrel structure ensures smooth operation, uniform mixing, and clean discharge without dead angles.
Internal and external double-layer screw belts enable fast mixing and high uniformity.
Bearings at both ends reduce material entry, lowering maintenance requirements.
Easy feeding via screw conveyor, with the feed port conveniently flush with the ground.
ISO9001 certified materials ensure durability and quality.
Horizontal Two-Axis Screw Belt Mixer:
Components: Consists of feeding and mixing sections.
Feeding: Materials enter through the hopper and are lifted into the mixing cylinder by spiral blades.
Mixing: Inside the cylinder, materials undergo round-trip staggered movements, resulting in thorough mixing.
These mixers offer efficient, multi-directional mixing, surpassing standard mixer uniformity. Safety features include protection bars to prevent accidents during operation. Installation and operation guidelines ensure user safety and machine longevity.
Vacuum Drying Mixer:
How it Works: The double-cone vacuum drying mixer employs a double-cone rotary tank. In a vacuum, steam or hot water heats the tank’s jacket, transferring heat to the wet material through the tank’s inner wall. Vapor evaporates and is pumped away through a vacuum pump, accelerating material drying and achieving uniformity through constant rotation and movement.
Purpose: Ideal for vacuum drying and mixing powder and granular materials in industries like pharmaceuticals, food, and chemicals, especially for heat-sensitive, oxidizable, or solvent-recovering materials.
About LKMixer
LKMixer is a professional manufacturer for fertilizer production line, grinder, mixer and granulator, shredder. These machines are widely used in food, pharmaceutical, cosmetic, health care products and chemical industries. The Food materials like Peanut, mushroom, seeds, potato, bean, tobacco, salt, cannabis, tea, Sugar, corn, Coffee, rice, pepper, grain as so on. Grinders have many types such as Pulse Dust Grinder which suitable for zero pollution environment, Turbine Mill which is suitable for coffee bean, 12-120mesh all can meet, Ultrafine Grinding Mill covers 80-200mesh, and also Winnowing Dust Grinder or other grinding machines like SF Hammer. Welcome to contact us for details. Contact us for more information. Proposal, catalog, quotation. Mobile/WhatsApp: +86 18019763531 Tel: +86 21 66037855 Email: sales@lkmixer.com
Contact Us
How to choose right model for blenders:
In the realm of powder and granular material mixing equipment, the choice between vertical cone mixers and horizontal mixers often arises. While many users opt for domestic vertical cone mixers, experts advise against it due to high maintenance rates and inherent shortcomings. Instead, they recommend horizontal mixers for their high efficiency, quality mixing, short unloading times, and minimal residual amounts. However, selecting and using horizontal mixers requires attention to specific details:
Matching Capacity to Production: Choose a bed mixing machine according to daily production needs. With each batch requiring approximately 10 minutes for processing, plus additional time for discharging and feeding, the mixer can process about 4 batches per hour. Select a mixer with a capacity matching production demands, such as 100 kg per batch for a processing rate of 400 kg per hour.
Consistent Mixing Ability: Ensure the pitch of the double spiral belts used in horizontal spiral belt mixers is consistent. The pitch of the inner spiral belt should be smaller than the outer spiral belt’s, preventing material concentration in one direction. Consistency in pitch ensures uniform mixing.
Optimizing Design Principles: Consider the gap between the spiral belt and the shell, ideally ranging from 4 mm to 10 mm. This gap facilitates friction-driven material mixing. Some manufacturers enhance products by improving machining accuracy, reducing the bottom gap to about 3 mm, or offering adjustable positions between the spindle and housing to maintain optimal gap distances.
Discharge Method: Pay attention to the discharge method when choosing a horizontal spiral belt mixer. Communicate with suppliers to select a valve form suitable for the process. Avoid side mouth discharge, which can delay mixing time or lead to excessive mixing, compromising uniformity.
Feeding Order: Adhere to a specific feeding order when using horizontal mixers. Begin with smaller ingredients like aniseed or corn meal, followed by group feeds like premix. Avoid feeding premix with a screw elevator to prevent segregation and loss of active ingredients.
Batch Feeding: Feed batches continuously after starting the mixer, without pausing between batches. Interrupting the process may cause power distance issues and motor burnout upon restarting.
Choosing an appropriate horizontal mixer and adhering to proper usage guidelines will significantly enhance mixture quality and positively impact production processes. Mastering self-mixing technology further reduces material costs, thereby increasing profits.
Role of Feed Mixers in Feed Production:
Feed mixers are crucial in feed production, ensuring effective mixing of feed raw materials and premixes. Proper mixing is essential for distributing ingredients and nutrients evenly, vital for extrusion, granulation, or direct feeding to livestock. Inadequate mixing diminishes feed quality and nutritional value, negatively impacting animal health.
The feed industry employs various mixer types, with vertical screw and horizontal mixers being the most common. Vertical screw mixers process materials from top to bottom gradually, while horizontal mixers utilize blades connected to a horizontal rotor for quicker processing, suitable for diverse farm sizes.
Blender Videos
You may also interest in:
FAQ(Click and See More)
Why Choose Us?
We have 20 years manufacturing experiences; 15600 cubic meters factory area; 5000sets annual capacity; 55 professional engineers;
What’s your main maket?
South America: Brazil, Colombia, Peru, Bolivia, Uruguay, Paraguay ;Romania;
USA with UL Certification
Middle East: Saudi, Arabia, Oman, Turkey
Europe: Russia, Australia, Belarus, Ukraine, Poland
Can you support OEM?
– Yes, OEM or ODM. Machine can be customized according to customer detail requirement, including capacity and voltages, motor certifications.
– Drawing and raw materials also can be customized.
What after-sale services?
– 7*24 customer service online;
– 7*24 engineers online services;
– 12 months warranty services.
WHAT kind of MACHINE YOUR COMPANY HAVE?
CAN YOU GIVE ME GUIDE ON OTHER MACHINE ? TO FULL MY PRODUCTION LINE
YES ! Our f have factory build more than 20 years now, we can design and customize whole line, besides of the grinding machine, mixing machine, we can also fully support to provide the washing machine, cutting machine, drying machine, packing machine, filling machine. Though we are not producing these machine, but our brother companies co-work together for over 20 years, we have rich experience in providing you a full effective production line, fully automatically or semi-automatically.
HOW TO VISIT YOUR COMPANY?
Our Factory located in Jiangsu Province, very near to Shanghai, you can fly to Shanghai Pudong Airport, we pick you up and take you by car 2 hours ride, can reach our factory, welcome your visit.
WHAT’S YOUR BEFORE & AFTER SERVICE ?
1) Before your purchasing, we need to know your detail request, such as what kind of material you want to grind and mixing, what final product powder or granule you want to reach. Because different material and powder sizes request of different machine to do. We can provide professional advice and rich experience help to choose machine. Most of the products we have already did before for other customer, trail test or run mass production, so we knows which machine is best in performance of grinding and mixing. This is of very importance in helping you choose the right model. We also wish this can help our customer a lot. Even the material we didn’t do before, we will prepare the same material and to do the trail test and send video to you for your reference.
2) One Year guarantee of machine quality. If the machine have problem within one year, we will send you the spare parts to you for replacement, but this not including the damage caused by human causes. We also have 24 hours on line guide for customer, if you have operation difficulty, we will guide by video and on line communication with our engineer for your emergency debug.
3) For small machine, we sell with whole machine, it’s no need to install, and easy to operation, no problems for operation. While for large machine, its’s also not difficult to install with video guideline, but if you need, we can assign our technicians to go abroad, the round ticket, food and residents will be paid by customer.
HOW ABOUT YOUR PAYMENT TERM?
Our payment term is T/T. 50% payment in advance, rest of 50% payment finish before the goods shipped. When we finish the machine production we will do trail test and run the machine take videos for your green light. You pay the rest of 50% payment then.
What difference between Artesian and Mechanical blender?
As industries advance, so does the diversity and importance of mixers in industrial processes. Mixers have become indispensable in various sectors such as chemical, food, construction, pharmaceuticals, and fertilizers, contributing to the production of numerous everyday products through mixing methods categorized as artesian and mechanical.
Artesian Mixing involves the movement between materials, achieving uniform mixing through inherent friction. Conversely, Mechanical Mixing employs mechanical forces to uniformly mix materials. Gas mixing generally falls under artesian mixing, while modern mixing equipment often integrates both artesian and mechanical mixing. Mechanical mixing, where the mixing container remains stationary, is particularly common.
High-Speed Mixer
High-speed mixers, primarily used in the plastics industry, offer a swift and efficient solution for mixing and stirring various materials. The structural design and principles of high-speed mixers, like the SHR high-speed mixers, find applications across different industries.
Components:
Mixing Tank: Featuring a conical vessel with cooling and heating capabilities, it houses the material and binder inlet and facilitates temperature regulation.
Rotating Blade: Special-shaped stirring paddles mounted on the main shaft, offering two speed settings (60r/min and 120r/min) for thorough mixing.
Transmission Device: Comprising a motor, tape wheel, and reducer, allowing variable speed regulation.
Discharge Door: Mechanism for material discharge, equipped with a connecting rod system driven by a cylinder.
Cooling and Heating Devices: Ensure optimal mixing temperature through cooling water and hot water circulation.
Working Principle:
The main shaft, driven by the motor via belt wheel and reducer box, rotates the special-shaped blades. Centrifugal force propels materials along the conical tank wall in a swirling motion, facilitating efficient mixing of materials with different densities. Various raw materials and binders are input through the inlet, while mixed materials exit through the side discharge port.
Application Range:
High-speed mixers excel in efficiently mixing solid-liquid, solid-powder, and powder-powder combinations. They find extensive use in industries such as fine chemicals, electronics, ceramics, pharmaceuticals, and food processing.
Operating Procedures:
Before operation, ensure all connections are tight, components are flexible, and the equipment is clean. Check the motor’s rotation direction and monitor its smooth operation during use. Regular maintenance, including cleaning between material changes and monitoring load factors during feeding, ensures optimal performance and equipment longevity.
Conclusion:
Understanding the artesian and mechanical mixing principles of mixers, such as high-speed mixers, along with adhering to proper operating procedures, ensures efficient and consistent mixing essential for diverse industrial processes.
What size is a large weed grinder?
We have small and large weed grinder, according to your capacity , each model can customize the size to your request. For example, BJB machine largest size if 1250*1040*1650mm(Length * Width*Height), capacity is from 10~1500kg per hour.
The Major difference of Paddle Blender and Ribbon Blender:
The Different Efficiency of Blending:
Ribbon Blender advantages and disadvantages:
Ribbon Blender always have “U shape” tank, and at the same time have two or more ribbon vertical or horizontal lay out in tank. These ribbons rotate in opposite direction, and this opposite strength can bring the raw materials to be blended sufficiently. Ribbon Blender always suitable for large batch of material blending. Because of the top of tank open and easy to load the material into the tank, so it can mixing large batch of materials.
The great feature and advantages of the ribbon blender is that it is capable to mix different shape, dimension, and density material in large batch. To make final power, granule, or liquid to be fully mixed. Another point is that ribbon mixer can mix in low speed, so to protect the product not to be destroyed elements in material, to keep the raw material in good condition.
Though the ribbon blenders have many advantages, but at the same time, it also have disadvantages, such as:
Firstly, it is not efficient enough when mixing small batch material. This is because the mixing machine tank always exists corner which is hard to mixed, this may result as when mixing small batch of material, some portion can not be mixed fully.
Secondly, If need to heat in mixing procedure, the heat transferring is also another problem. The open top side and the gap between the top make it is not so high efficient in heat transferring.
Paddle Mixer Advantages and Disadvantages:
As to the mixing time, the paddle mixer is most efficient. They can finish the mixing process within several minutes. The V shape and Cone Mixer usually need to finish in longer time. LINKER Paddle Mixer reduced the space in mixing tank, this upgraded the efficiency at most.
Paddle Mixer is also more easy in maintain when compared with other mixer. You can easily change and adjust the position of paddle, the material also protected as they are softly treated by paddle instead of in high rotating speed.
The structure of paddle mixer usually have two or more rows of paddle. If need, the paddle can also add the cutting function, softly and gently. So paddle mixer can be used in both small and large batch mixing.
One of the main advantages of using a paddle mixer is its ability to slowly, finely and efficiently mix materials with different sizes, shapes and densities. In addition, blade mixers are capable of mixing at high speeds, making them ideal for products that need to be mixed quickly.
Blade mixers also have better heat transfer because the closed top and cylindrical design has a larger surface area and is enclosed and improves efficiency.
However, one of the main disadvantages of using paddle mixers is that they are not as efficient at loading bulk material directly into the mixer as the cylinder type configuration usually requires conveying during loading.
When choosing a mixer, it is important to consider the size and type of material to be mixed. Ribbon mixers are ideal for mixing large volumes of bulk material when loaded without a conveyor, while paddle mixers are better for mixing small or large batches, but usually require a conveyor for loading. In addition, both types of mixers can mix materials of different sizes, shapes and densities. Ultimately, deciding which type of mixer is best for your needs will depend on the specific application. Finally, when you compare mixing time and batch time efficiency, paddle mixers are superior to ribbon mixers.
About LKMixer
LK Mixer is a professional manufacturer for fertilizer production line, grinder, mixer and granulator, shredder. These machines are widely used in food, pharmaceutical, cosmetic, health care products and chemical industries. The Food materials like Peanut, mushroom, seeds, potato, bean, tobacco, salt, cannabis, tea, Sugar, corn, Coffee, rice, pepper, grain as so on. Grinders have many types such as Pulse Dust Grinder which suitable for zero pollution environment, Turbine Mill which is suitable for coffee bean, 12-120mesh all can meet, Ultrafine Grinding Mill covers 80-200mesh, and also Winnowing Dust Grinder or other grinding machines like SF Hammer. Welcome to contact us for details.