WFM Vibrating Pulverizer
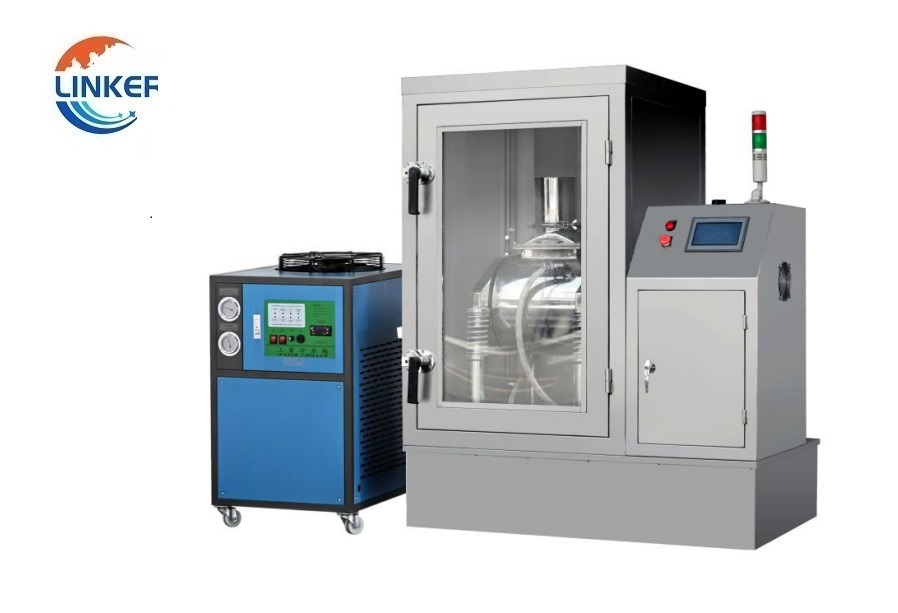
WFM Ultrafine Vibrating Pulverizer
I. Introduction
A. Background on pulverization
Pulverization is the process of reducing the size of solid materials into smaller particles, often to a fine powder. This process is essential in many industries such as pharmaceuticals, food processing, chemical engineering, and mining. Pulverization is used to enhance the surface area of materials, make them easier to mix and handle, increase their reactivity, or separate valuable minerals from unwanted impurities.
The history of pulverization can be traced back to ancient times, where primitive tools like mortar and pestle were used to crush and grind materials. Over time, more advanced techniques were developed such as the use of watermills and windmills to power crushing machines. The Industrial Revolution in the 18th and 19th centuries saw the widespread adoption of steam-powered mills for pulverizing various materials.
Today, different types of pulverizers are used for different materials and applications. These include ball mills, hammer mills, jet mills, and vibrating pulverizers. Vibrating pulverizers, also known as vibratory mills or vibratory grinding mills, are relatively new and have gained popularity due to their unique ability to generate intense vibrations that aid in pulverization. They are often used for the pulverization of hard, brittle, or fibrous materials, such as minerals, ores, ceramics, and plastics.
B. Importance of pulverization in various industries
Pulverization is an important process in various industries because it allows for the reduction of solid materials into smaller particles, which can be advantageous for a number of reasons. Here are some examples of how pulverization is important in different industries:
- Pharmaceutical Industry: In the pharmaceutical industry, pulverization is used to create fine powders of active ingredients that can be more easily absorbed by the body. This is particularly important for drugs that need to be rapidly dissolved or absorbed. Pulverization also helps to ensure that each dose of a drug contains the correct amount of active ingredient.
- Food Processing Industry: Pulverization is used in the food processing industry to reduce the particle size of ingredients like spices, sugar, and flour. This can improve the texture and flavor of food products and make them easier to mix and package.
- Chemical Engineering Industry: Pulverization is used in the chemical engineering industry to increase the surface area of materials, which can enhance their reactivity. For example, pulverized coal is used in the production of electricity in power plants, and pulverized limestone is used in the production of cement.
- Mining Industry: Pulverization is an important step in the mining industry because it is used to separate valuable minerals from unwanted impurities. For example, ore that has been pulverized can be separated using gravity separation techniques or flotation to extract the desired mineral.
- Plastics Industry: Pulverization is used in the plastics industry to create fine powders of plastic materials that can be used as additives or fillers in other plastic products. This can help to improve the mechanical properties of plastic materials and reduce costs by using recycled plastic materials.
C. Overview of vibrating pulverizers
Vibrating pulverizers, also known as vibratory mills or vibratory grinding mills, are a type of pulverizer used to grind and pulverize various materials into fine powders. They are typically used for the pulverization of hard, brittle, or fibrous materials, such as minerals, ores, ceramics, and plastics.
Vibrating pulverizers use a unique mechanism to generate intense vibrations that aid in the pulverization process. The grinding media, which can be steel balls, ceramic beads, or other materials, are placed in a grinding chamber that is vibrated at high frequencies using an eccentric motor. The vibration of the chamber causes the media to impact and grind against the material, reducing it to a fine powder.
One of the advantages of vibrating pulverizers is that they can be used for wet or dry grinding, which makes them versatile for a variety of applications. Additionally, the intense vibrations generated during the pulverization process can help to break apart agglomerated particles and improve the homogeneity of the final product.
Vibrating pulverizers can be operated in batch or continuous modes and can be equipped with various accessories, such as sieves or classifiers, to control the particle size distribution of the final product. They are widely used in industries such as mining, chemical engineering, and materials science, and are particularly useful for pulverizing materials that are difficult to grind using other types of pulverizers.
II. Literature Review
A. Historical development of pulverizers
The history of pulverizers can be traced back to ancient times when crude grinding tools like mortars and pestles were used to crush and grind materials. Over time, more sophisticated techniques were developed, such as the use of water-powered mills and windmills to grind grains into flour.
During the Industrial Revolution in the 18th and 19th centuries, steam-powered mills became popular for pulverizing various materials. These mills used large rollers or balls to crush and grind materials, and they were used extensively in the mining industry to extract valuable minerals from ore.
In the 20th century, new technologies were developed that allowed for more precise and efficient pulverization. Ball mills, which use steel balls to grind materials, were first introduced in the 1920s and became popular for grinding minerals and ores. Hammer mills, which use rotating hammers to pulverize materials, were also developed in the early 20th century and are still widely used today.
In the 1950s, the jet mill was invented, which uses high-speed jets of compressed air or steam to pulverize materials. This technology allowed for finer particle sizes and more precise control over the grinding process.
Vibrating pulverizers, which use intense vibrations to pulverize materials, were first introduced in the 1970s and have gained popularity in recent years due to their unique ability to generate high-frequency vibrations. They are particularly useful for grinding hard, brittle, or fibrous materials that are difficult to pulverize using other methods.
Today, a variety of pulverizers are available for different applications, including ball mills, hammer mills, jet mills, and vibrating pulverizers. These technologies continue to evolve and improve, with a focus on increasing efficiency, reducing energy consumption, and minimizing environmental impact.
B. Types of pulverizers
There are several types of pulverizers used in various industries to grind and pulverize materials. Here are some of the most common types:
- Ball mills: These are cylindrical or conical mills that contain a charge of steel balls that grind the material into a fine powder. Ball mills are commonly used in the mining and chemical industries to grind materials.
- Hammer mills: These mills use rotating hammers to pulverize the material into small particles. They are commonly used in the agricultural industry to grind grains and other crops, as well as in the pharmaceutical industry to grind drugs.
- Jet mills: Jet mills use high-speed jets of air or steam to grind materials into a fine powder. They are commonly used in the pharmaceutical and chemical industries.
- Pin mills: Pin mills use a rotor with pins or blades that rotate at high speeds to pulverize the material. They are commonly used in the food and pharmaceutical industries.
- Vibrating pulverizers: These use intense vibrations to pulverize materials. They are commonly used in the mining, chemical engineering, and materials science industries to grind hard, brittle, or fibrous materials.
- Cage mills: Cage mills are cylindrical mills that contain a series of cages, each containing a row of rotating blades. They are commonly used in the fertilizer and chemical industries to grind materials.
The choice of pulverizer depends on factors such as the type of material being ground, the desired particle size, and the required throughput. Each type of pulverizer has its own advantages and disadvantages, and the appropriate type must be selected based on the specific needs of the application.
C. Vibrating pulverizer design and operation
The design of a vibrating pulverizer is typically based on a circular or rectangular grinding chamber with a central vibrating motor that causes the chamber to vibrate at high frequencies. The grinding media, such as steel balls, ceramic beads, or other materials, are placed in the chamber along with the material to be pulverized. The vibration of the chamber causes the media to impact and grind against the material, reducing it to a fine powder.
Vibrating pulverizers can be operated in batch or continuous modes. In batch mode, a fixed amount of material is added to the grinding chamber, and the pulverization process is carried out until the desired particle size is achieved. In continuous mode, material is continuously fed into the grinding chamber, and the pulverization process is carried out until the desired particle size is achieved or until the material is completely ground.
The vibrating motor is typically an eccentric motor that is mounted on the bottom of the grinding chamber. The motor generates high-frequency vibrations that are transmitted to the chamber through a series of springs or other mechanisms. The frequency and amplitude of the vibrations can be adjusted to optimize the pulverization process for a specific material.
To ensure efficient pulverization and prevent damage to the equipment, it is important to control the flow rate of the material and the size and composition of the grinding media. Vibrating pulverizers can be equipped with various accessories, such as sieves or classifiers, to control the particle size distribution of the final product.
Overall, the design and operation of a vibrating pulverizer must be carefully controlled to ensure optimal pulverization and maximum efficiency. The choice of design and operating parameters will depend on the specific material being pulverized, the desired particle size, and other factors related to the application.
D. Research on the performance of vibrating pulverizers
There have been several research studies on the performance of vibrating pulverizers, with a focus on understanding the factors that affect their efficiency and effectiveness for different applications.
One study published in the Journal of Materials Science and Engineering compared the performance of a vibrating pulverizer with that of a ball mill for grinding a range of materials, including glass, alumina, and zirconia. The study found that the vibrating pulverizer was more effective for grinding hard and brittle materials than the ball mill, with higher grinding efficiency and lower energy consumption.
Another study published in Powder Technology evaluated the performance of a vibrating pulverizer for grinding limestone and found that the optimal grinding conditions were achieved at a specific amplitude and frequency of vibration. The study also found that the pulverizer was more effective than a conventional ball mill for grinding limestone, with lower energy consumption and higher grinding efficiency.
In a study published in the Journal of Chemical Engineering and Processing, researchers compared the performance of a vibrating pulverizer with that of a jet mill for grinding talc. The study found that the vibrating pulverizer was more effective for producing fine particles with a narrow particle size distribution than the jet mill, with lower energy consumption and higher grinding efficiency.
Overall, these studies suggest that vibrating pulverizers can be an effective and efficient tool for grinding a range of materials, particularly hard and brittle materials that are difficult to grind using conventional methods. The performance of the pulverizer can be optimized through careful control of the vibration amplitude and frequency, as well as the choice of grinding media and other operating parameters.
Parameter of Vibrating Pulverizer:
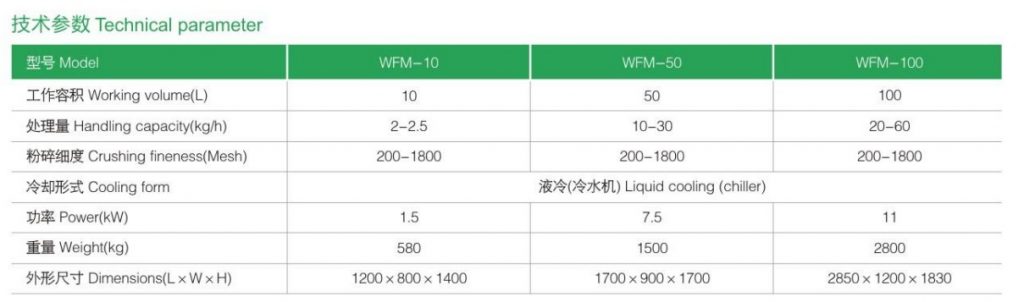
Model | WFM-10 |
Working Volume | 10 |
Capacity(kg/h) | 2-2.5 |
Fineness(Mesh) | 200-1800 |
Cooling Form | Liquid Cooling(Chiller) |
Power(KW) | 1.5 |
Weight(KG) | 580 |
Dimension(L*W*H) | 1200*800*1400 |
Business Type: | Manufacturer/Factory | Main Products: | Mill, grinder, granulator, mixer, Crushing Equipment |
Number of Employees: | 100 | Year of Establishment: | 2014.05 |
Production Capacity | 5000Set/Year | After-sales Service: | Technical Support; on-line teach lessons |
R&D Capacity: | ODM, OEM | Annual Output Value: | US$5 Million – US$10 Million |
No. of R&D Staff: | 5 | No. of Production Lines: | 6 |
LK Mixer is a professional manufacturer for grinder, mixer and pulverizer. These machines are widely used in pharmaceutical, cosmetic, health care products and chemical industries. Our main product including granulating machine, grinder, mixer, dryer, etc. All mechanical products in accordance with the China GMP design requirements. And also we have other certifications such as CE, UL for motors.
Business Philosophy
“Quality is the main policy of sales” and “integrity is the principle of success” are the business philosophy of our people. We carry out one-year warranty, lifelong maintenance service, with technical consultation, with material test machine and other services, and long-term supply of equipment. Welcome new and old customers to negotiate cooperation!
Certifications:
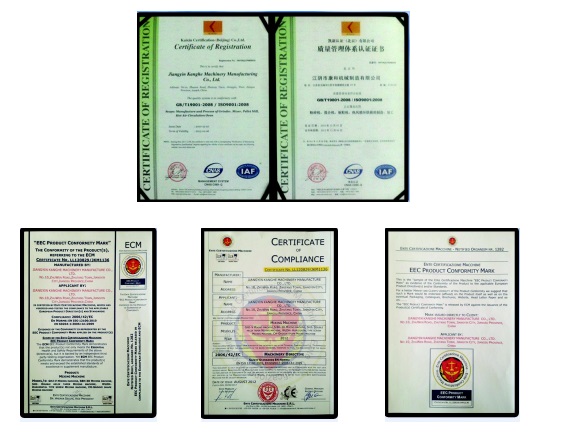
Various Cutting Knife Type Pictures:
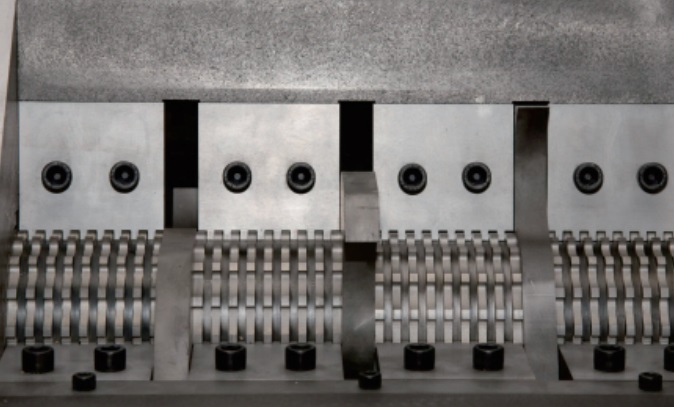
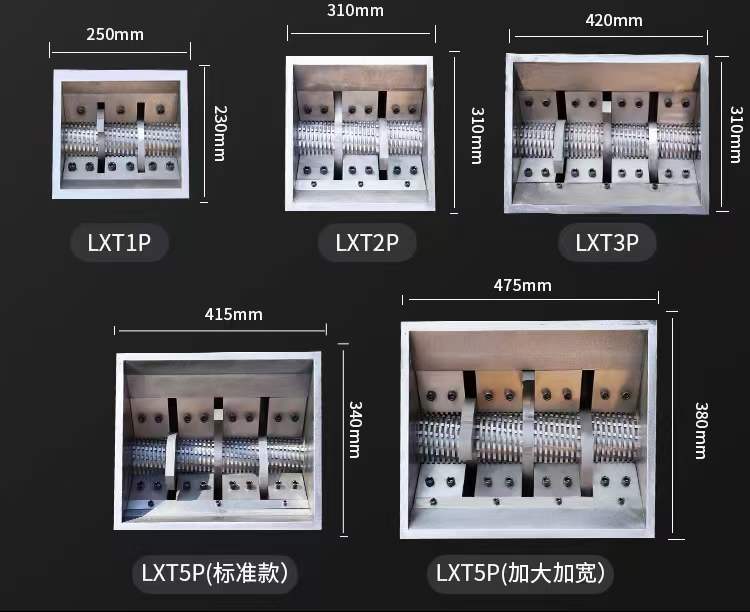
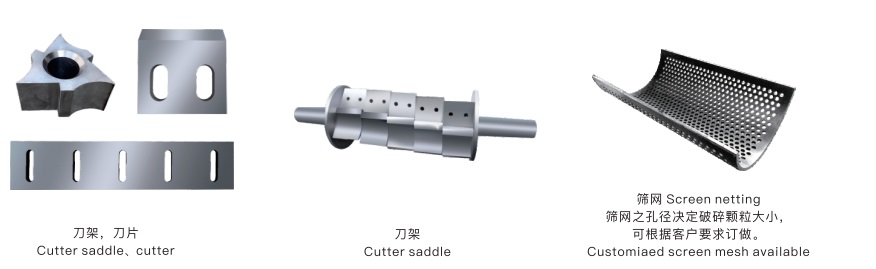
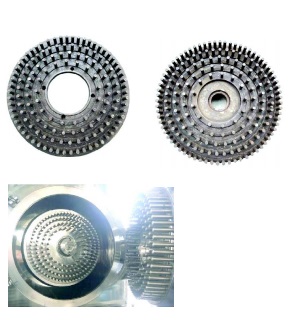
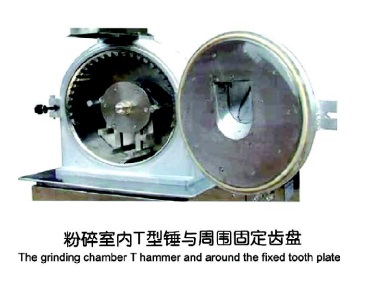
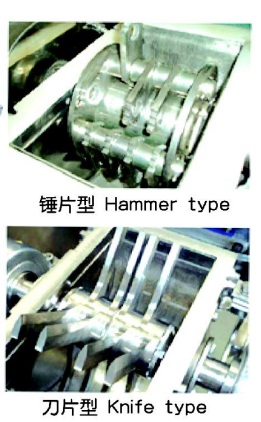
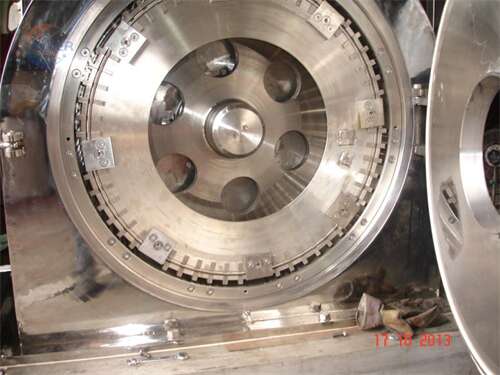
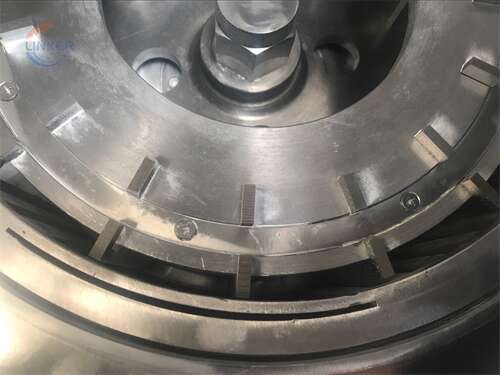
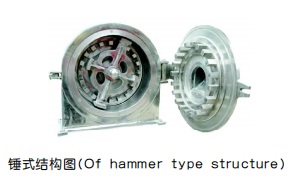
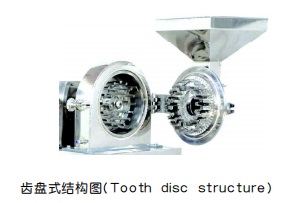
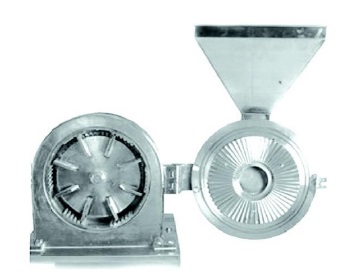
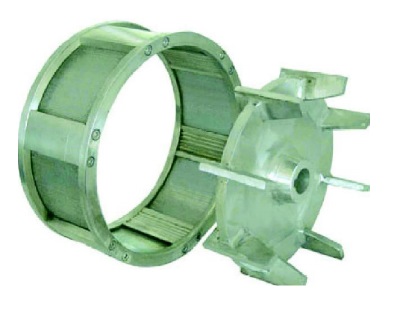
Electric Cabinet with UL Certification
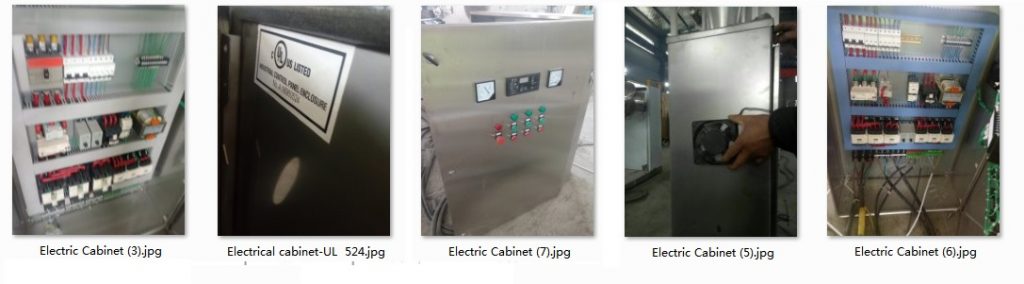
Cyclone Processor and Motors:
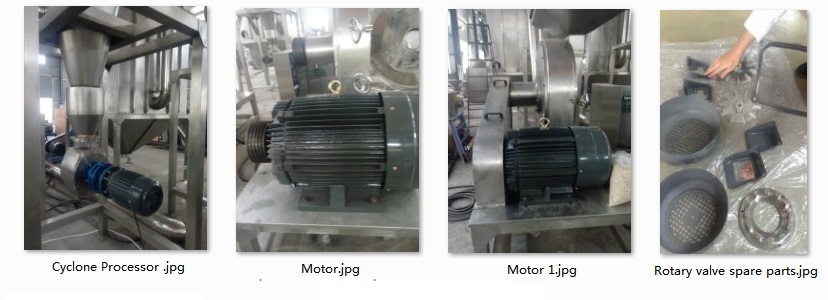
Spare Parts:
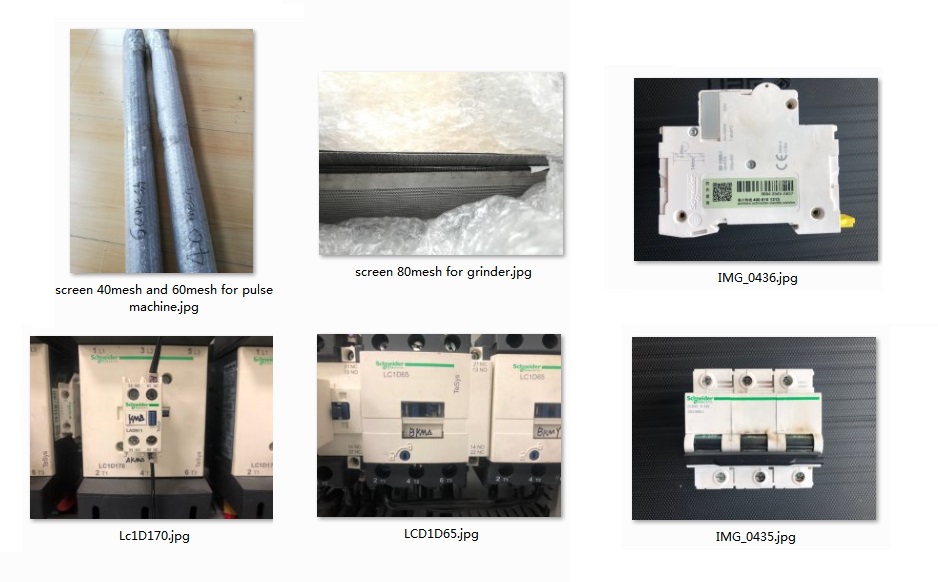
Small Machine Packing:
Small machine packed with export fumigation-free wooden cases, goes with bulk shipment or in container.
When packing small machines for sea shipment, it is important to take measures to ensure that the machines are protected from damage during transit. Here are some general steps that a manufacturer may follow when packing small machines for sea shipment:
- Clean and dry the machine: Before packing, the machine should be thoroughly cleaned and dried to prevent any moisture or debris from causing damage during transit.
- Disassemble the machine: If possible, the machine should be disassembled into its component parts to reduce its overall size and make it easier to pack.
- Wrap the machine in protective material: The machine should be wrapped in a layer of protective material, such as bubble wrap or foam, to protect it from scratches and impact during transit.
- Place the machine in a sturdy box: The wrapped machine should then be placed in a sturdy box that is appropriate for the size and weight of the machine. The box should be made of durable material, such as corrugated cardboard or plywood, and should be able to withstand the rigors of sea transit.
- Add packing material: The box should be filled with packing material, such as packing peanuts or air pillows, to provide cushioning and prevent the machine from shifting during transit.
- Seal the box: The box should be securely sealed with high-quality packing tape to prevent it from opening during transit.
- Label the box: The box should be clearly labeled with the machine’s name, weight, and any other relevant information, as well as the destination address and contact information.
Overall, the goal is to pack the small machine in a way that will protect it from damage during transit and ensure that it arrives at its destination in good condition. It is important to follow proper packing procedures and use high-quality packing materials to minimize the risk of damage during sea shipment.
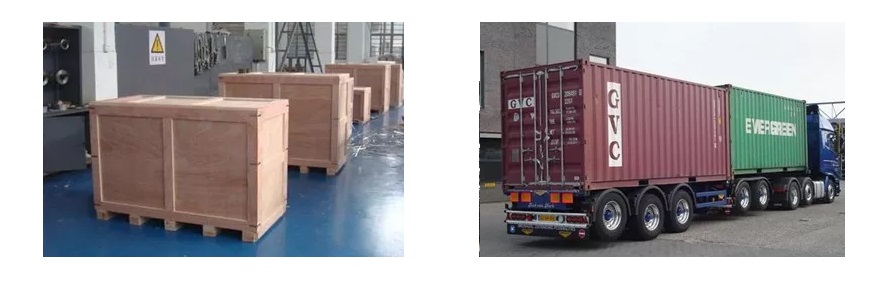
Large Machine Packing:
Packing a large machine for sea shipment can be a complex and challenging task. However, with careful planning and attention to detail, it is possible to pack a large machine for sea shipment in a way that will ensure that it arrives at its destination in good condition. Here are some general steps that a manufacturer may follow when packing up a large machine for sea shipment:
- Clean and prepare the machine: Before packing, the machine should be thoroughly cleaned and prepared. All fluids, such as oil or coolant, should be drained, and any loose or detachable parts should be removed.
- Disassemble the machine: If possible, the machine should be disassembled into its component parts to reduce its overall size and make it easier to pack. Each part should be carefully labeled and numbered to ensure that it can be easily reassembled at the destination.
- Protect delicate parts: Delicate or fragile parts should be wrapped in protective material, such as bubble wrap or foam, to protect them from damage during transit.
- Build a custom crate: A custom crate should be built around the machine to provide a secure and sturdy enclosure. The crate should be made of durable material, such as plywood, and should be designed to fit the machine snugly. The crate should also include braces or supports to prevent the machine from shifting during transit.
- Add cushioning material: The crate should be filled with cushioning material, such as packing peanuts or air pillows, to provide extra protection and prevent the machine from moving or shifting during transit.
- Securely fasten the machine: The machine should be securely fastened to the crate to prevent it from moving or shifting during transit. This may involve using straps, bolts, or other fasteners to hold the machine in place.
- Seal and label the crate: The crate should be securely sealed with high-quality packing tape, and should be clearly labeled with the machine’s name, weight, and any other relevant information. The destination address and contact information should also be clearly marked on the crate.
Overall, packing a large machine for sea shipment requires careful planning and attention to detail. It is important to use high-quality materials and follow proper packing procedures to ensure that the machine arrives at its destination in good condition. A professional packing and shipping company may be consulted to ensure that the machine is properly packed and prepared for sea shipment.
Customer Side Machine Groups Showcase Videos:
Dust Collector Shipment
Shipment – Packing Method
Two Large Industrial Grinder Ready to Ship
Domestic Shipment Show Case:
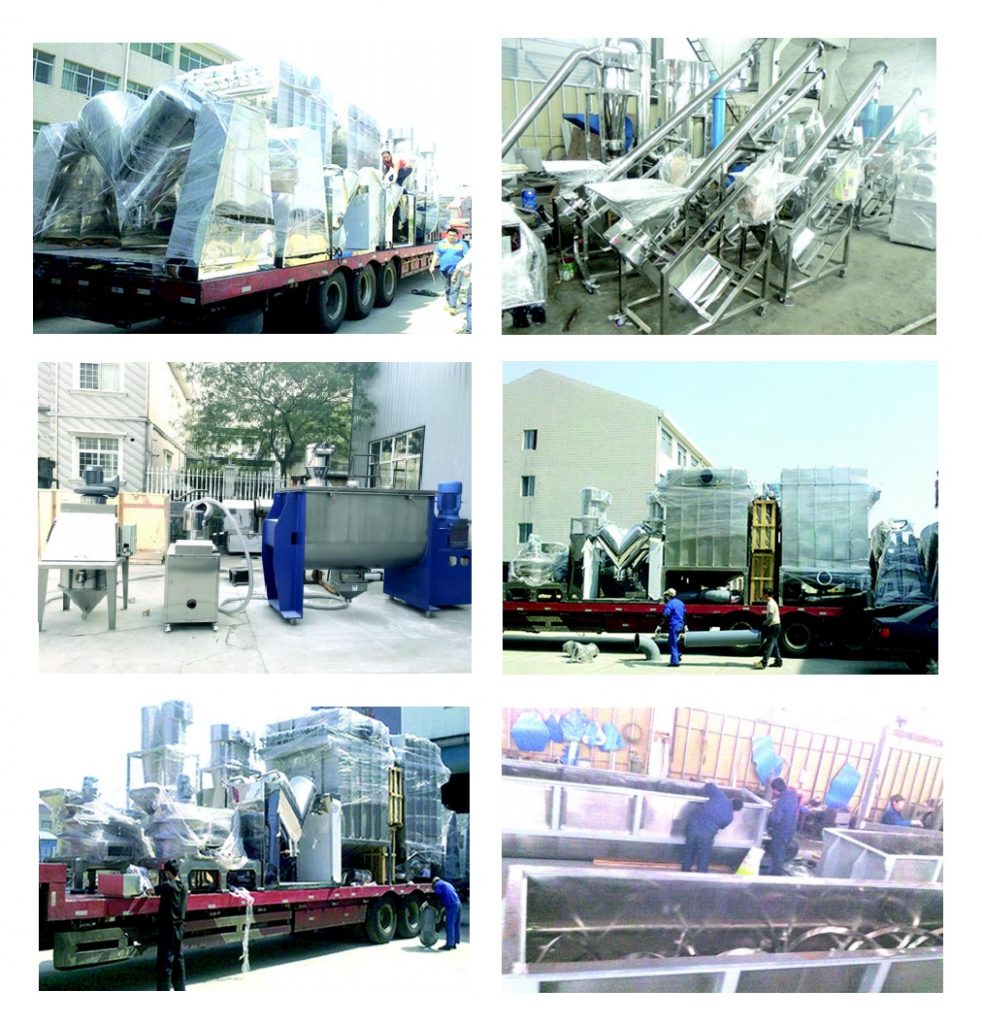
Installation Layout:
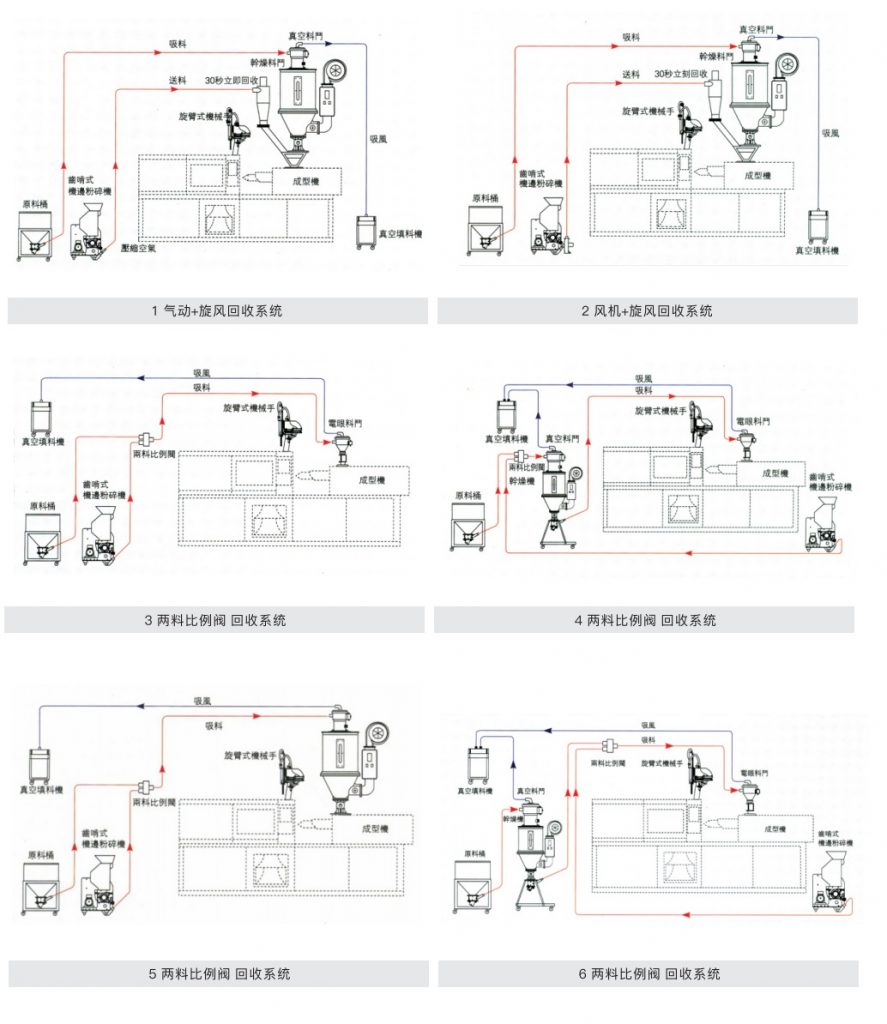
Maintenance and Safety Measures
Proper maintenance practices for the machine
Proper maintenance practices are essential for ensuring the efficient and safe operation of a universal grinder. Here are some maintenance practices that should be followed:
- Regular cleaning – The machine should be cleaned regularly to remove any debris, dust, or coolant that may accumulate on the machine’s surfaces. This can be done using a soft brush, air hose, or a cleaning solution.
- Lubrication – The machine’s moving parts should be lubricated regularly to reduce friction and wear. The manufacturer’s recommendations for lubrication intervals and types should be followed.
- Inspection – The machine should be inspected regularly for any signs of wear, damage, or misalignment. Any issues should be addressed immediately to prevent further damage or safety hazards.
- Replacement of worn or damaged parts – Worn or damaged parts should be replaced immediately with genuine parts from the manufacturer.
- Calibration – The machine should be calibrated regularly to ensure that it is operating within the specified tolerances and accuracy.
- Operator training – Proper operator training is essential for ensuring the safe and efficient operation of the machine. Operators should be trained on the proper operation, maintenance, and safety procedures for the machine.
- Record keeping – A maintenance log should be kept to track the machine’s maintenance history, including cleaning, lubrication, inspection, and repairs. This can help identify any trends or issues that need to be addressed.
Following these maintenance practices can help ensure the safe and efficient operation of a universal grinder, prolong its lifespan, and reduce the risk of downtime and costly repairs.
Safety measures for operators and workers
Safety measures for operators and workers are crucial when using a universal grinder. Here are some safety measures that should be followed:
- Personal protective equipment (PPE) – Operators and workers should wear appropriate PPE, including safety glasses, hearing protection, gloves, and safety shoes.
- Machine guards – The machine should be equipped with proper machine guards to prevent access to the grinding wheel during operation. The guards should be in good condition and properly installed.
- Lockout/tagout procedures – Lockout/tagout procedures should be followed to ensure that the machine is not accidentally started or energized during maintenance or repair.
- Training – Operators and workers should receive proper training on the safe operation of the machine, including the use of PPE, machine guards, and lockout/tagout procedures.
- Inspection – The machine should be inspected regularly for any signs of wear, damage, or misalignment that may pose a safety hazard.
- Proper use of grinding wheels – Operators should ensure that the grinding wheel is properly installed, dressed, and aligned. The grinding wheel should not be overloaded or forced into the material being ground.
- Proper handling of coolant – If coolant is used, operators should ensure that it is properly mixed, applied, and contained. Coolant should not be allowed to accumulate on the floor, as it can create a slipping hazard.
- Emergency procedures – Emergency procedures should be established and communicated to all operators and workers in case of an accident or injury.
Following these safety measures can help prevent accidents and injuries when using a universal grinder. It is important to prioritize safety and ensure that all operators and workers are trained and informed about the potential hazards of the machine.
Model | WFM-50 |
Working Volume | 50 |
Capacity(kg/h) | 10-30 |
Fineness(Mesh) | 200-1800 |
Cooling Form | Liquid Cooling(Chiller) |
Power(KW) | 7.5 |
Weight(KG) | 1500 |
Dimension(L*W*H) | 1700*900*1700 |
Model | WFM-100 |
Working Volume | 100 |
Capacity(kg/h) | 20-60 |
Fineness(Mesh) | 200-1800 |
Cooling Form | Liquid Cooling(Chiller) |
Power(KW) | 11 |
Weight(KG) | 2800 |
Dimension(L*W*H) | 2850*1200*1830 |
Vibrating Herb Grinder
A vibrating herb grinder is a type of grinder that is designed to grind herbs, spices, and other plant materials using vibrations to break down the material into small, uniform pieces. This type of grinder is becoming increasingly popular due to its ease of use and efficiency.
Vibrating herb grinders typically consist of a container, a motor, and a set of grinding blades or teeth. The container is filled with the herb or plant material that needs to be ground, and the motor is turned on to create vibrations that help to break down the material.
As the motor vibrates, the grinding blades or teeth rotate and grind the material into smaller pieces. This process continues until the desired consistency is reached.
One of the advantages of using a vibrating herb grinder is that it can grind herbs and other plant materials quickly and efficiently. The vibrations created by the motor help to break down the material more effectively than a traditional manual grinder, which can be time-consuming and require more effort.
Additionally, vibrating herb grinders are often designed to be portable and easy to use. Many models are small enough to fit in a pocket or bag, making them convenient for on-the-go use.
It is important to note that vibrating herb grinders can vary in terms of quality and performance. Some models may produce inconsistent results or may not grind certain types of herbs or plant materials effectively. It is important to do research and read reviews before purchasing a vibrating herb grinder to ensure that it will meet your needs and expectations.
Overall, a vibrating herb grinder can be a useful tool for anyone who enjoys cooking with fresh herbs or using plant materials for medicinal or recreational purposes. Its ease of use, efficiency, and portability make it a popular choice for many people.
Universal Grinder Youtube Video (See More)
About LKMixer
LKMixer is a professional manufacturer for fertilizer production line, grinder, mixer and granulator, shredder. These machines are widely used in food, pharmaceutical, cosmetic, health care products and chemical industries. The Food materials like Peanut, mushroom, seeds, potato, bean, tobacco, salt, cannabis, tea, Sugar, corn, Coffee, rice, pepper, grain as so on. Grinders have many types such as Pulse Dust Grinder which suitable for zero pollution environment, Turbine Mill which is suitable for coffee bean, 12-120mesh all can meet, Ultrafine Grinding Mill covers 80-200mesh, and also Winnowing Dust Grinder or other grinding machines like SF Hammer. Welcome to contact us for details. Contact us for more information. Proposal, catalog, quotation. Mobile/WhatsApp: +86 18019763531 Tel: +86 21 66037855 Email: sales@lkmixer.com
Contact Us
FAQ(Click and See More)
What is a puck mill?
A puck mill is a type of grinding mill used to grind and homogenize materials such as rocks, minerals, and other hard materials. It is a specialized machine that uses a combination of impact and friction to break down the material into smaller particles.
The puck mill consists of a circular grinding chamber with a puck and ring set inside. The puck is a small, flat disc made of a hard material, such as tungsten carbide, that is placed in the center of the grinding chamber. The ring is a larger circular disc that is positioned around the puck.
To use the puck mill, the material to be ground is placed into the grinding chamber, on top of the puck. The ring is then lowered onto the puck, and the machine is turned on. The puck begins to spin rapidly, creating a centrifugal force that causes it to impact and grind against the ring.
The high-speed rotation of the puck and the friction between the puck and the ring help to break down the material into smaller particles. The resulting ground material can then be used for further analysis or processing.
Puck mills are often used in geological and mineralogical research, where it is important to obtain consistent and homogeneous samples for analysis. They are also used in the pharmaceutical and chemical industries, as well as in materials science and engineering.
Overall, a puck mill is a specialized type of grinding mill that is used for the rapid and efficient grinding of hard materials. Its unique design and operation make it a valuable tool in various industries where particle size and consistency are critical factors.