WFJ Best Cutting Type Pulverizer
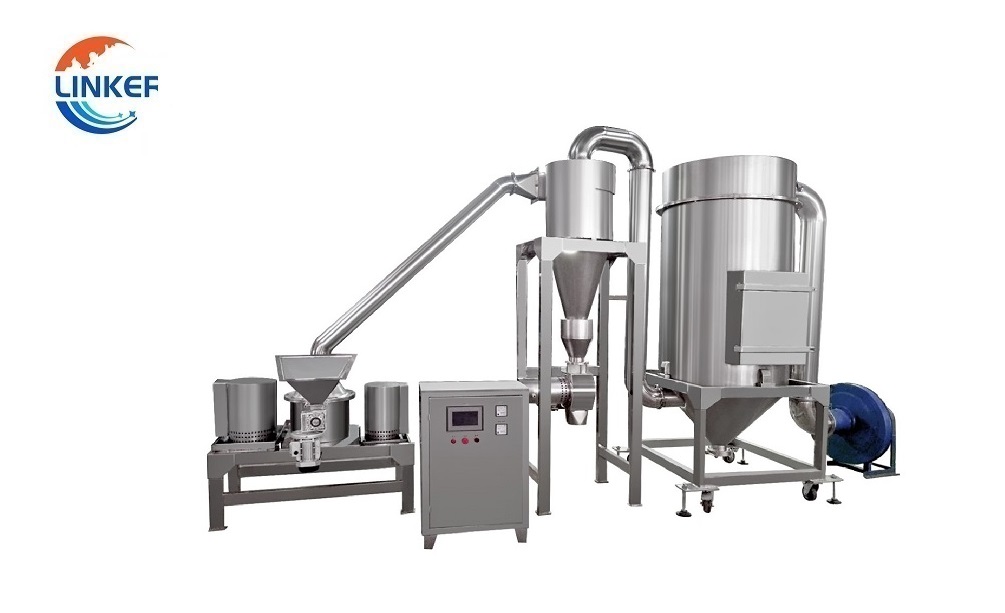
WFJ Ultrafine Cutting Type Pulverizer
- Powder Size: 80-320mesh
- Capacity: 10-2000kg/h
- Motor Power (KW):13.37-119kw;
- Dimension(mm):4200*1250*2700~8500*2800*4830.
- FOB Unit Price: 1 Unit: $12,000~$48,923; 5 Units Price: 10,800~58,154.
- Application: metal, Medicine, potato, pepper, bean, grain, rice, cannabis, Sugar, herb, food, salt, mushroom, seeds, corn,
Maintenance and Safety Measures
Proper maintenance practices for the machine
Proper maintenance practices are essential for ensuring the efficient and safe operation of a universal grinder. Here are some maintenance practices that should be followed:
- Regular cleaning – The machine should be cleaned regularly to remove any debris, dust, or coolant that may accumulate on the machine’s surfaces. This can be done using a soft brush, air hose, or a cleaning solution.
- Lubrication – The machine’s moving parts should be lubricated regularly to reduce friction and wear. The manufacturer’s recommendations for lubrication intervals and types should be followed.
- Inspection – The machine should be inspected regularly for any signs of wear, damage, or misalignment. Any issues should be addressed immediately to prevent further damage or safety hazards.
- Replacement of worn or damaged parts – Worn or damaged parts should be replaced immediately with genuine parts from the manufacturer.
- Calibration – The machine should be calibrated regularly to ensure that it is operating within the specified tolerances and accuracy.
- Operator training – Proper operator training is essential for ensuring the safe and efficient operation of the machine. Operators should be trained on the proper operation, maintenance, and safety procedures for the machine.
- Record keeping – A maintenance log should be kept to track the machine’s maintenance history, including cleaning, lubrication, inspection, and repairs. This can help identify any trends or issues that need to be addressed.
Following these maintenance practices can help ensure the safe and efficient operation of a universal grinder, prolong its lifespan, and reduce the risk of downtime and costly repairs.
Safety measures for operators and workers
Safety measures for operators and workers are crucial when using a universal grinder. Here are some safety measures that should be followed:
- Personal protective equipment (PPE) – Operators and workers should wear appropriate PPE, including safety glasses, hearing protection, gloves, and safety shoes.
- Machine guards – The machine should be equipped with proper machine guards to prevent access to the grinding wheel during operation. The guards should be in good condition and properly installed.
- Lockout/tagout procedures – Lockout/tagout procedures should be followed to ensure that the machine is not accidentally started or energized during maintenance or repair.
- Training – Operators and workers should receive proper training on the safe operation of the machine, including the use of PPE, machine guards, and lockout/tagout procedures.
- Inspection – The machine should be inspected regularly for any signs of wear, damage, or misalignment that may pose a safety hazard.
- Proper use of grinding wheels – Operators should ensure that the grinding wheel is properly installed, dressed, and aligned. The grinding wheel should not be overloaded or forced into the material being ground.
- Proper handling of coolant – If coolant is used, operators should ensure that it is properly mixed, applied, and contained. Coolant should not be allowed to accumulate on the floor, as it can create a slipping hazard.
- Emergency procedures – Emergency procedures should be established and communicated to all operators and workers in case of an accident or injury.
Following these safety measures can help prevent accidents and injuries when using a universal grinder. It is important to prioritize safety and ensure that all operators and workers are trained and informed about the potential hazards of the machine.
About LKMixer
LKMixer is a professional manufacturer for fertilizer production line, grinder, mixer and granulator, shredder. These machines are widely used in food, pharmaceutical, cosmetic, health care products and chemical industries. The Food materials like Peanut, mushroom, seeds, potato, bean, tobacco, salt, cannabis, tea, Sugar, corn, Coffee, rice, pepper, grain as so on. Grinders have many types such as Pulse Dust Grinder which suitable for zero pollution environment, Turbine Mill which is suitable for coffee bean, 12-120mesh all can meet, Ultrafine Grinding Mill covers 80-200mesh, and also Winnowing Dust Grinder or other grinding machines like SF Hammer. Welcome to contact us for details. Contact us for more information. Proposal, catalog, quotation. Mobile/WhatsApp: +86 18019763531 Tel: +86 21 66037855 Email: sales@lkmixer.com
Contact Us
Cutting Type Powder Grinding Mill Youtube Video (See More)
FAQ(Click and See More)
What is the difference between a pulverizer and a hammer mill?
Pulverizers and hammer mills are two common machines used for particle size reduction in various industries. While they share similarities in their function of reducing materials, there are distinct differences between the two. In this article, we will explore the dissimilarities between pulverizers and hammer mills.
A pulverizer, also known as a grinder or mill, is a mechanical device used for the purpose of grinding, crushing, or pulverizing different types of materials into smaller particles. Pulverizers typically consist of a rotating drum or cylinder, which contains grinding media such as steel balls or rods. The material to be pulverized is fed into the drum, and as the drum rotates, the grinding media crush and grind the material, resulting in size reduction.
On the other hand, a hammer mill is a machine that uses a series of rotating hammers or blades to crush or shred materials into smaller pieces. Hammer mills operate by the principle of impact, where the hammers strike the material and break it apart. The material is fed into the hammer mill chamber, and the rotating hammers or blades apply force to the material, reducing it to the desired particle size.
One significant difference between pulverizers and hammer mills lies in the mechanism of particle size reduction. Pulverizers primarily use the forces of compression, impact, and attrition to reduce the size of materials. The grinding media within the pulverizer drum collide with the material, exerting pressure and causing fractures and attrition. The resulting particles are typically finer and more uniform in size.
In contrast, hammer mills rely on the principle of impact to break down materials. The high-speed rotating hammers or blades strike the material with force, causing it to fracture and break apart. The impact forces generated by the hammers result in a range of particle sizes, from fine to coarse, depending on the size of the screen or grate used in the mill.
Another notable difference between pulverizers and hammer mills is the range of materials they can process. Pulverizers are versatile machines that can handle a wide variety of materials, including minerals, chemicals, plastics, and food products. They are commonly used in industries such as mining, pharmaceuticals, and food processing. In contrast, hammer mills are primarily used for processing agricultural and organic materials, such as grains, wood, and biomass. They find applications in industries such as agriculture, animal feed production, and wood processing.
Furthermore, the operating speed and energy consumption differ between pulverizers and hammer mills. Pulverizers typically operate at higher speeds compared to hammer mills, resulting in higher energy consumption. The high-speed rotation of the pulverizer drum requires more power to drive the grinding media and achieve size reduction. In contrast, hammer mills generally operate at lower speeds, requiring less energy for operation.
In conclusion, although both pulverizers and hammer mills are used for particle size reduction, they differ in their mechanisms, range of materials they can process, and operating characteristics. Pulverizers primarily use compression, impact, and attrition forces, while hammer mills rely on impact forces. Pulverizers are versatile machines used in various industries, while hammer mills are primarily employed in agriculture and wood processing. Understanding the differences between these two machines is crucial in selecting the appropriate equipment for specific applications.